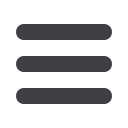
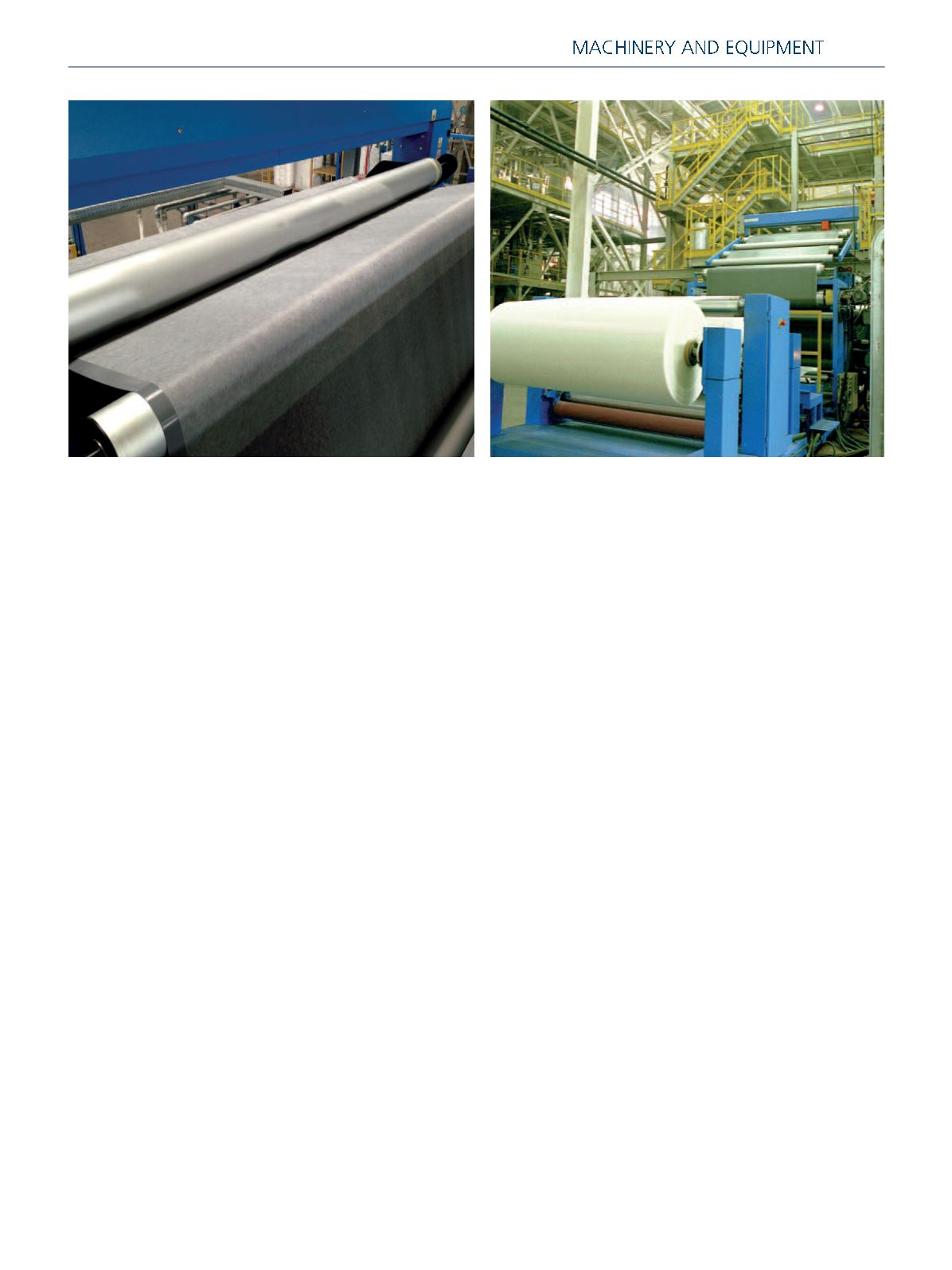
Improves waterproofing
membranes performances
T
he recent market trend is gradually growing more in
favour of synthetic components than bituminous ones,
AMUT manufactures extrusion lines producing waterproof-
ing membranes capable to process different thermoplastic
materials, such as F/PVC, TPO, TPE. The use of these materi-
als definitely improves the technical performances and the
physical features of the membrane, complying with interna-
tional standards and requirements in the civil works sector.
AMUT technology allows to:
1-multi-layers membrane production in one-step
(no off-line lamination required) using a single calender prop-
erly designed. This process reduces the costs and simplifies
the running operations for the operator;
2- flexible production guaranteed in terms of different ma-
terials processing on the same line;
3-multi-layer reinforced membranes production in one-step
by means of reinforcing elements laminated among the lay-
ers to enhance the mechanical resistance of the finished
product;
4- support base (fleece-back) lamination, usually on the
lower side of the membrane.
AMUT has recently supplied to a large Turkish customer, an
www.amut.itHYBRYD TYPE Line, capable to produce F/PVC
or TPO membrane 2.200 mm width, three layers of thermo-
plastic material and thickness range from 1 to
3 mm. The extruders’ screws special design is suitable for
both materials, so NO SCREW CHANGE is required. Within
the membrane’s configuration, it is included an inner rein-
forcing scrim and a bottom protective/supportive fleece
(fleece-back).
The total output is 1800 kg/h for F/PVC and 1250 kg/h for
TPO, giving an annual membrane production of more than 4
Million m².
A double-inlet calender consents to obtain a “sandwich”
geometry in a single step: the external layers, with insert-
ing/laminating of reinforcement in polyester or in glass fibre,
and coating of fleece-back.
The line is also equipped with thickness gauge measuring de-
vice, high accuracy winder unit to produce
jumbo and custom rolls and PC/PLC system to control all run-
ning operations of the line.
Extrusion International 1/2016
31