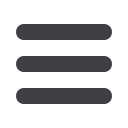
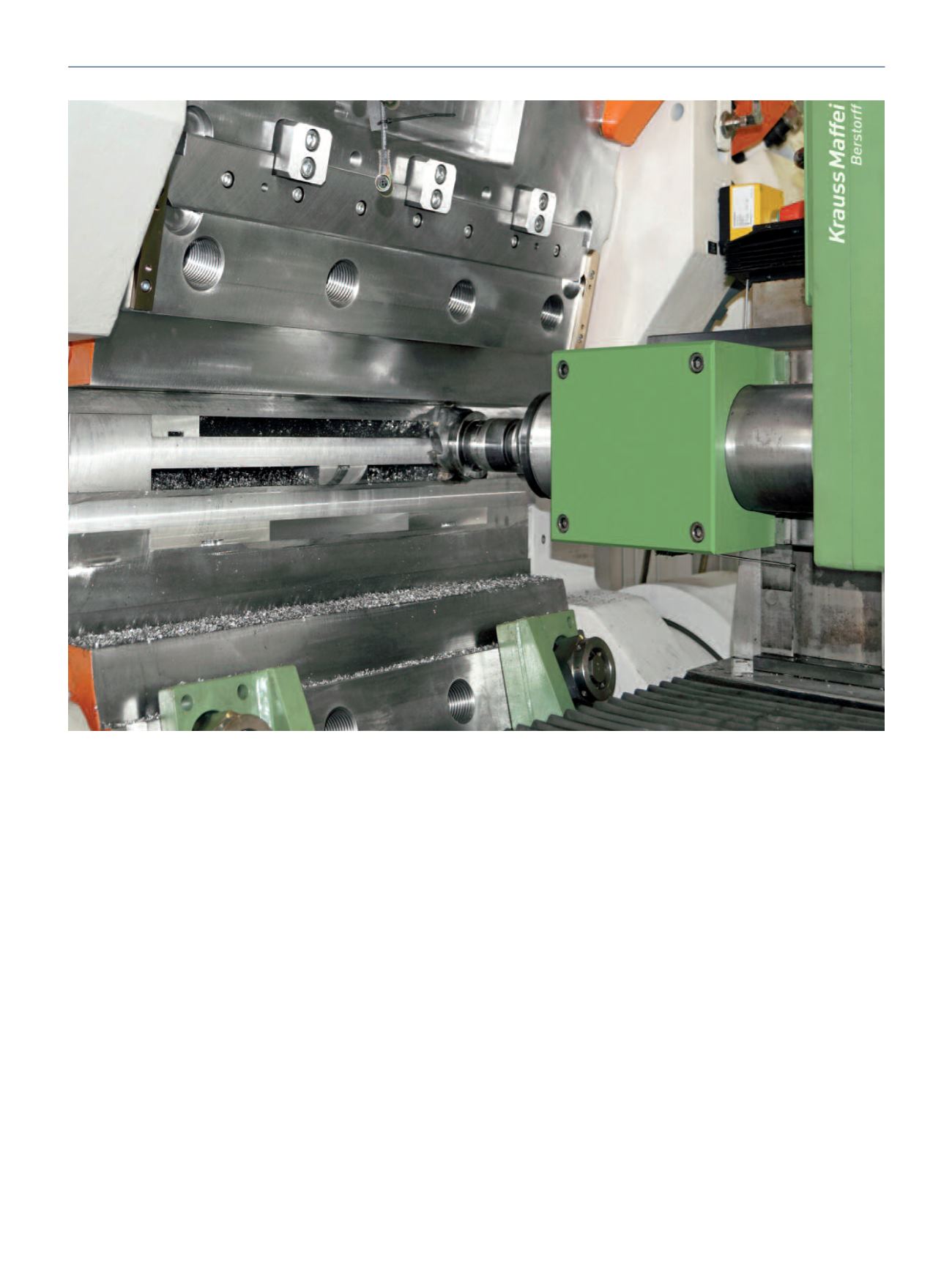
Extrusion International 1/2016
27
Wear- or damage-induced pressure losses
"Our mobile milling service is designed for tire producers
faced with leaks in the die area are after having operated
their extrusion heads for years on a 24/7 basis. The dam-
aged areas result from increased wear produced by com-
pounds with high silica shares or by cleaning operations due
to frequent formulation and profile changes", explains
Maik-Marcel Poppe, Head of KraussMaffei Berstorff's Tech-
nical Spare Parts Service. "This leads to pressure losses in the
extrusion head and to undesired material leakage."
The milling system was specifically designed for on-site high-
precision machining of Multiplex extrusion heads with work-
ing widths ranging between 360 mm and 1050 mm. The
system features brackets developed in-house that can be
firmly connected with the extrusion heads and perfectly
aligned. Various face-milling tools with a maximum number
of cutting edges and adapted geometries ensure optimum
chipping results and outstanding surface qualities.
www.kraussmaffeiberstorff.comTire producers benefit from mobile milling service
Thanks to the milling operation, the specified tolerances can
be met again. In addition, the sealing face of the die com-
ponents is substantially improved, which reduces material
and pressure losses. Upon completion of the milling process,
KraussMaffei Berstorff issues a detailed measuring report so
that the new coordinates can be considered in future extru-
sion tool or flow channel orders. The tire producer merely
needs to provide lifting gear and power supply and heat up
the head to extrusion temperature – that's it. Everything else
will be taken care of by the KraussMaffei Berstorff service
staff.
The mobile milling system is composed of milling heads in
different sizes, brackets and milling tools. Stored in a mar-
itime container, the milling system can be sent to produc-
tion sites all around the globe within shortest time.
The extrusion tools perfectly fit after the face-milling operation