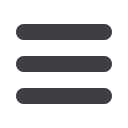
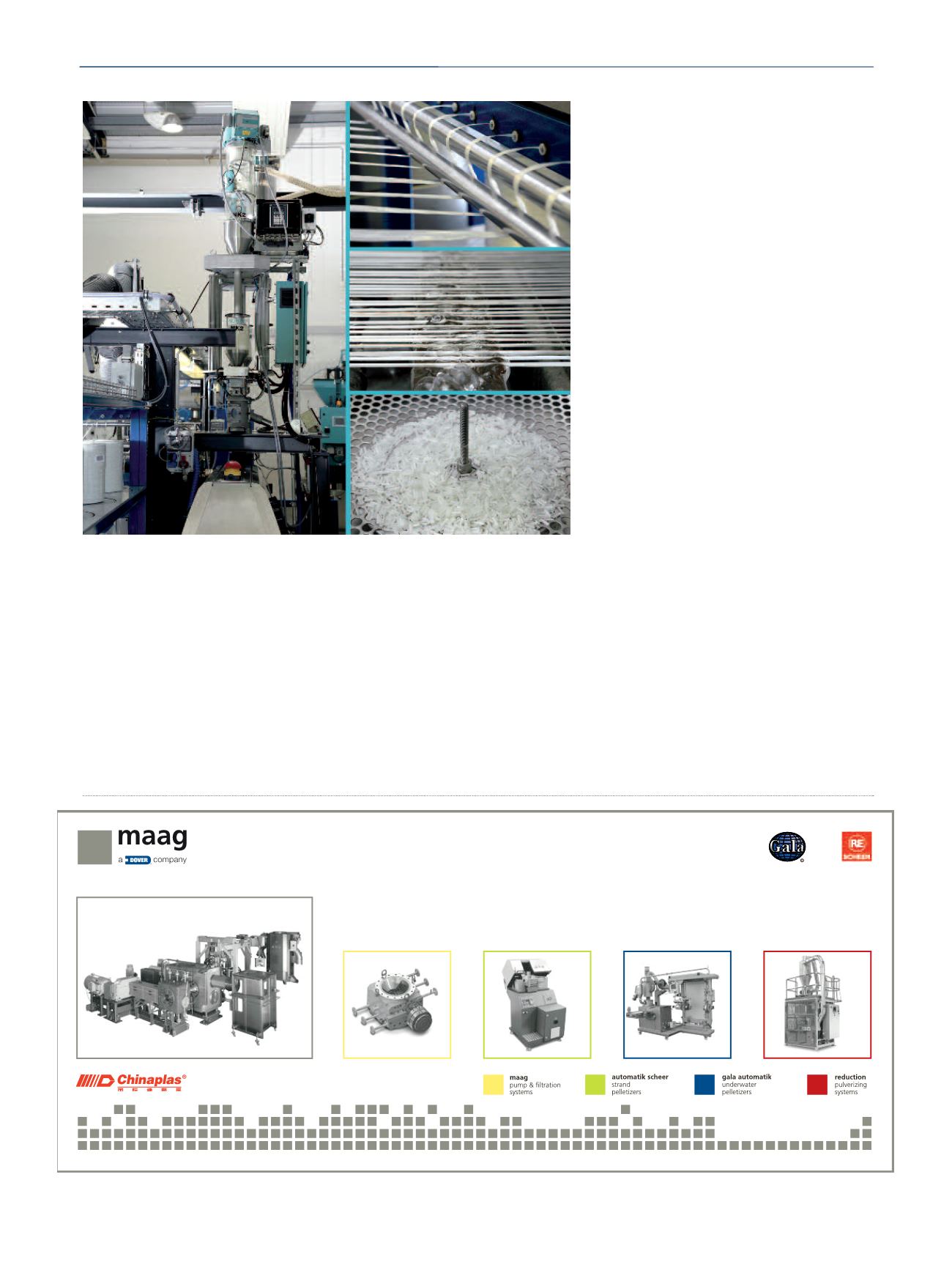
Extrusion International 2/2016
19
Producing LFT compounds by pultrusion invol-
ves continuously drawing fibre strands through
a polymer melt, so impregnating the individual
fibres with the polymer matrix and, once the re-
sultant fibre/polymer strands have cooled, pelle-
tising them. In order to be impregnated, in the
first process step, the fibre strands are guided
from the creels by a specially designed guide into
the impregnation die. Downstream from the die,
the hot fibre/polymer strands are then finally
shaped, for example into round strands or flat
tapes, in a profiling system. After cooling in a
cooling unit adapted to the polymer, they addi-
tionally pass through a puller which controls the
continuous passage of the strands through the
line.
ProTec is a one-stop shop capable of designing
and supplying complete turn-key lines tailored
to specific requirements from materials develop-
ment to testing and commissioning on the cus-
tomer's premises. The lines are capable of
handling fibre contents of up to 60 wt.% and
throughputs of up to 1,200 kg/h. Any conven-
tional thermoplastics or even biopolymers such
as PLA (polylactic acid) can be used as the ma-
trix, while glass, steel or carbon fibres can be
used as the reinforcing fibres.
The LFT line and all its modules are operated
from the central line controller. Variable parameters include line
speed, extruder throughput and pellet chopping length. Additio-
nal functions, located upstream or downstream depending on ap-
plication, may also be incorporated into the control system. These
include drying, conveying, dispensing and mixing of the feed com-
ponents.
www.maag.comMAAG – 4 STEPS AHEAD FOR YOUR SUCCESS
GEAR PUMPS, FILTRATION, PELLETIZING AND PULVERIZING SYSTEMS
Come and see us at Chinaplas: Hall E1, Booth J21
ProTec's LFT pultrusion technology produces high grade long-fibre-reinforced
pellets with a wide range of polymer matrices and huge variety of reinforcing
fibres. This technology also permits reliable and flexible adjustment of matrix
properties (Photo: ProTec Polymer Processing)
www.sp-protec.comprocess and materials development. A keystone of the line is a
high-performance compounding extruder equipped with a
SOMOS
®
Gramix S gravimetric dosing system capable of accura-
tely dosing and mixing up to nine components. As a result, a very
wide range of individual formulations of the polymer matrix can be
produced very flexibly directly in the process. Recycled material
and additional fillers may likewise be included in the material for-
mulation.