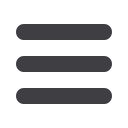
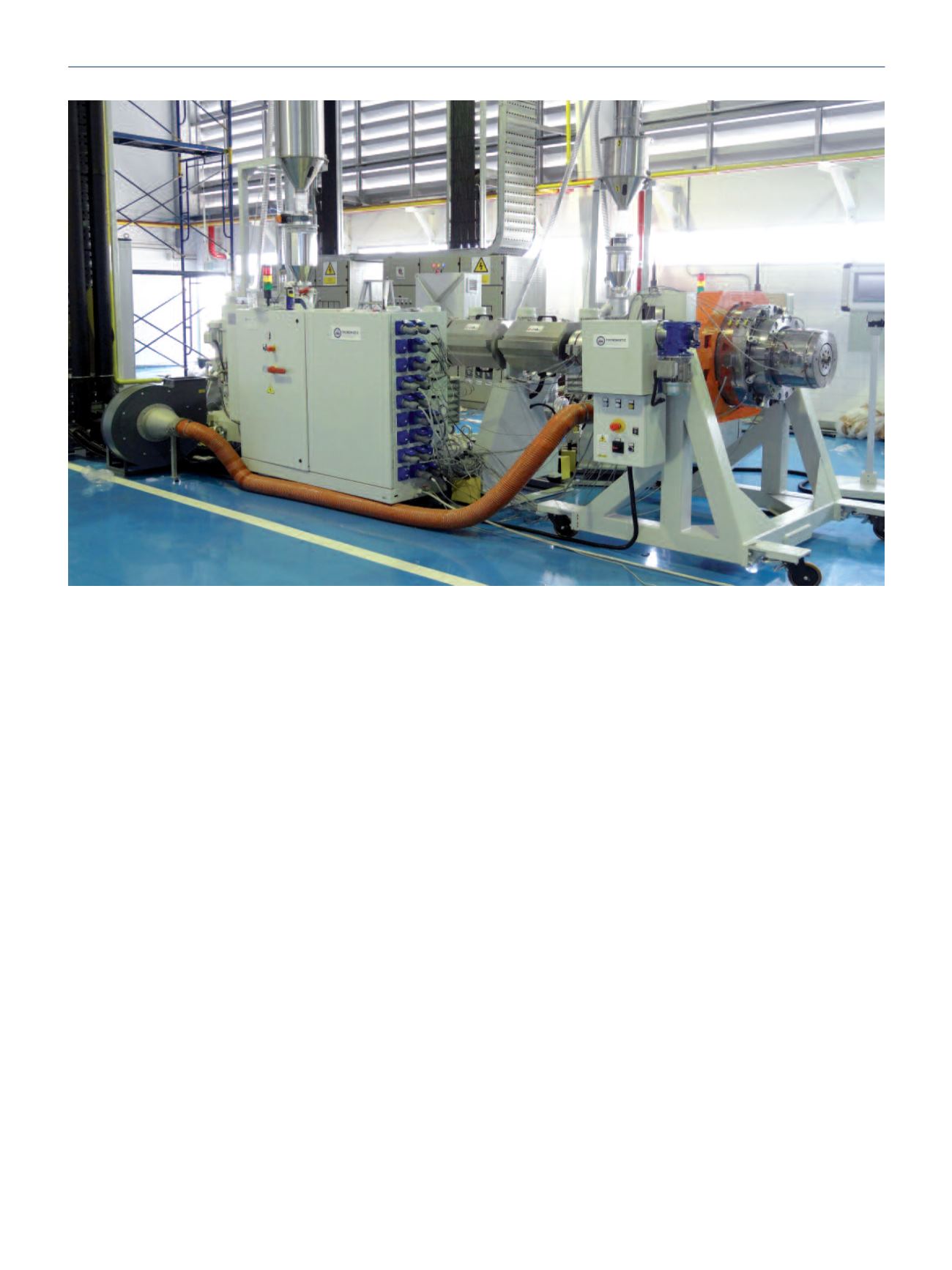
Extrusion International 3/2016
29
www.tecnomaticsrl.netT
he project is expected to have considerable environmental
and social impacts. The climatic context (drought and de-
sertification), the degradation of natural resources as well as
poverty, particularly among the least privileged segments of
the population, have increased the pressure on and demand
for water facilities and the need for integrated resource ma-
nagement planning to cope with climate change. The UN De-
velopment Programme (UNDP) estimates that total budgetary
spending in the water and sanitation sectors in sub-Saharan
Africa is currently around $800 mn a year. This amount could
likely be increased to $2.5 bn through “cost recovery”.
The manufacturing of pipes will help to support the develop-
ment and major infrastructure works under way in the coun-
try. The customer, representing an important group of
companies in the construction and trading business, even if
has started its pipe production recently, has rapidly gained re-
putation because of its choices quality oriented.
Technical details of the line
The lines, characterized by reliable technological solutions –
such as the extruders Vega with L/D ratio of 37 and Venus
heads with internal pipe cooling (PAC) – will produce HDPE
pipes with diameters up to 400 mm.
The VEGA series are the result of years of experience manu-
facturing extruders and of a constant effort to develop each
part of them. A constantly updated screw design, matched
with the water cooled straight feed bush, ensure excellent pro-
duction values with optimal plasticizing, even at high output
rate. The specific output has been further increased and it
maintains constant across the whole screw speed range or
even at high backpressures values.
The machines are equipped with synchronous AC motors spe-
cifically designed to be used in applications at high dynamic
performances with variable speeds. The selected motors are
mechanical sturdy to withstand high overloads while a highly
effective insulation avoid a gradual deterioration caused by
operation at high frequencies. Italian gearboxes characterised
by single block cast iron frame, for large oil capacity cooled by
an independent unit, and high performance bearing unit (up
to 500 bars) fit out the transmission system of the VEGA se-
ries. To process the high throughput with low backpressure
and stress load to the material VENUS die-heads are the pro-
per tools. Based on a spiral distributor concept with a com-
pact design thanks to their innovative geometries and the
internal air cooling (PAC system) ensure an optimal wall thick-
ness distribution, ovality and low sagging. The lines are syn-
chronized using gravimetrics on each extruder, to guarantee a
continuous raw material feed and to record variations in mass
throughput, thereby ensuring a perfect control of the weight
per meter and wall thickness distribution. The downstream
equipment includes Tecnomatic vacuum & cooling tanks, haul-
offs with caterpillar tracks controlled by an independent vector
AC motor and planetary saws with knife cutting and universal
clamping device, for a very accurate swarf-less pipe delivery.
VEGA extruder 75.37 with VENUS 400 and PAC air cooling system, for efficient pipe production