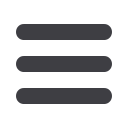
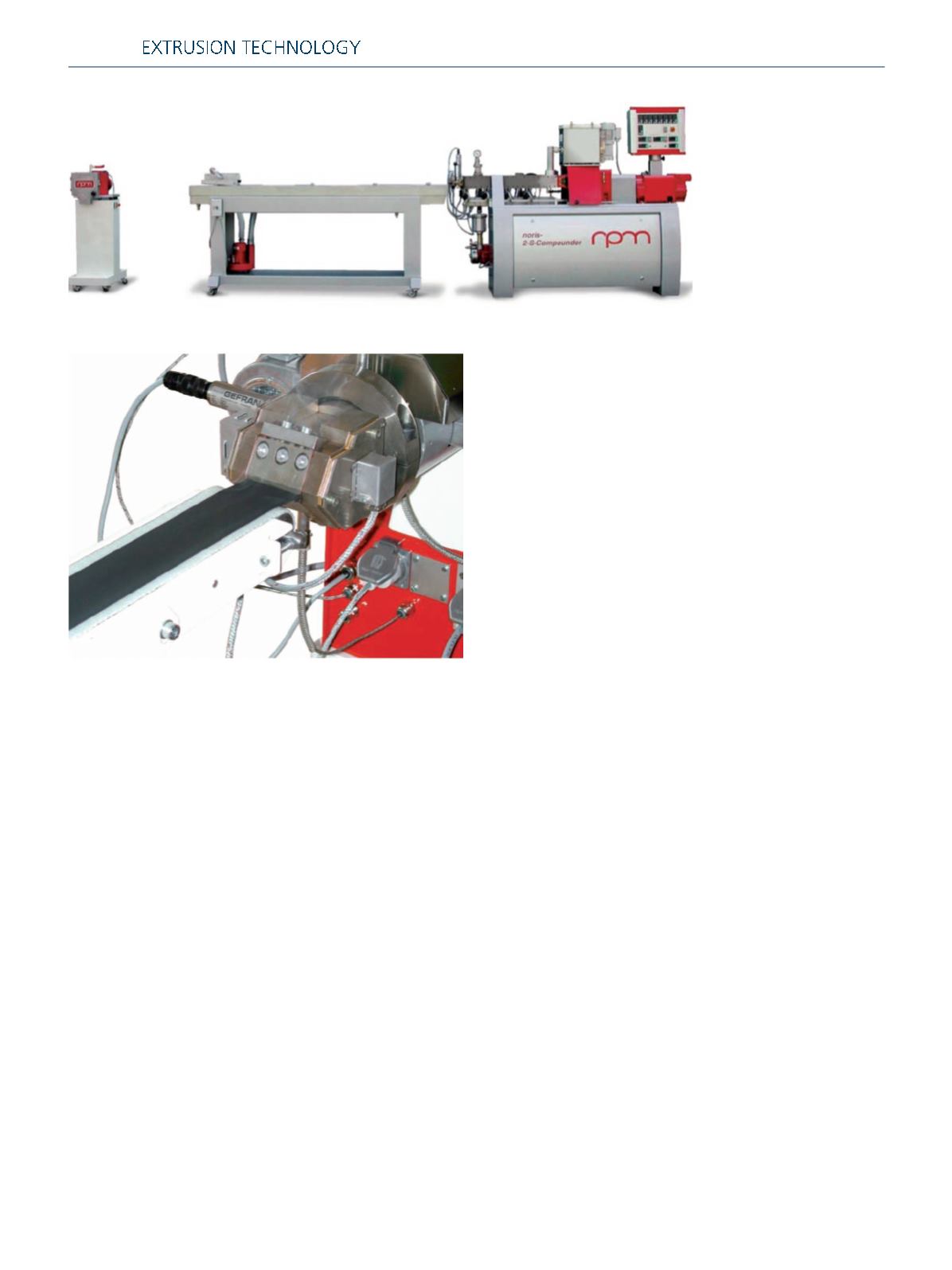
time, because the synchronized extruders that were more
suitable for this task were still protected by patents.
We succeeded in successfully using counter-rotating twin-
screw extruders for this task, thanks to suitable screw confi-
gurations and the development of mixing and homogenizing
elements. The complete system shown in Figure 1 consisted
of a pre-mixer, the extruder with metering and a screen
changer for the separation of coarse particles that were pre-
sent either as foreign bodies, or were created by the use of
powdered pigments.
The granulate nozzle head is followed by the strand cooling
bath, the granulator, classification and the intermediate silo.
Systems like these have been used to produce performance
ranges of between 30 and 300 kilograms per hour.
If no fine grist is available for the polymer, part of the total
polymer content, 50% for example, must be crushed to a
grain size of about 50 microns by a pulverizer. Together with
the non-crushed polymer, this mixture can be very success-
fully used as a starting material.
In the initial phase of masterbatch production, simple pro-
duction colors like black, white, green, etc. were preferred –
but the plastics world became increasingly more colorful and
the number of required color settings increased rapidly. Sy-
stems like the one shown in Figure 2 are often used to ma-
nufacture these concentrates, which are very often required
in smaller batch sizes.
The advantage of this machine is its universal application,
since screw configurations, cylinder structure and other pa-
rameters can be adjusted to match the task at hand. Apart
from the low investment costs of a machine like this, another
advantage gained by using this type of modular screw and
cylinder is that you can change your processing parameters
and materials very quickly. This is why the laboratory twin-
screw extruder – or compounder as it’s called nowadays –
has an extraordinary wide range of uses.
Besides the manufacturing of color masterbatches, a system
like this can also be designed to manufacture additive ma-
sterbatches of all kinds such as stabilizerbatch, lubricant-
batch, anticorrosivebatch, etc. Batches of any kind with such
plants can be produced with systems like these during the
course of development.
Colorimetric tests are relatively expensive, so a check using
test strips is often used as an alternative. These test strips,
either extruded by single-screw test extruders or by the test
foils method enable a simple, uncomplicated comparison bet-
ween the color quality actually achieved and the desired qua-
lity. Figure 3 shows a system like this. It consists of a
single-screw test extruder, a strip extrusion tool and a disch-
arge conveyor belt.
A particularly high dispersion quality is required for a ma-
sterbatch used in the field of foil production. The quality can
be tested by a laboratory film blowing system as shown in Fi-
gure 4.
In 1966 and 1967, we delivered the first machines for testing
masterbatch quality and manufacturing masterbatches to
customers in Germany, such as the Schleeberger Company
in Wuppertal and the masterbatch manufacturer Zvesda in
the former Yugoslavia. These and many other companies
subsequently became manufacturers of high-quality master-
batches. The variety of colors and masterbatch quality con-
stantly increased. One of the largest masterbatch consumers
is still foil industry, mainly in the LTPE, HDPE and polystyrene
fields – and this meant that the masterbatches had to be pro-
duced from the base polymer with these materials. The cable
industry with basic materials of soft PVC and polyolefin also
provided interesting applications.
Fig. 2: LAB strand
granulation plant
(Source: Noris Plastic)
Fig. 3: Discharge conveyor belt (Source: Noris Plastic)
Extrusion International 5/2016
26