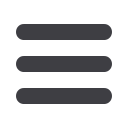
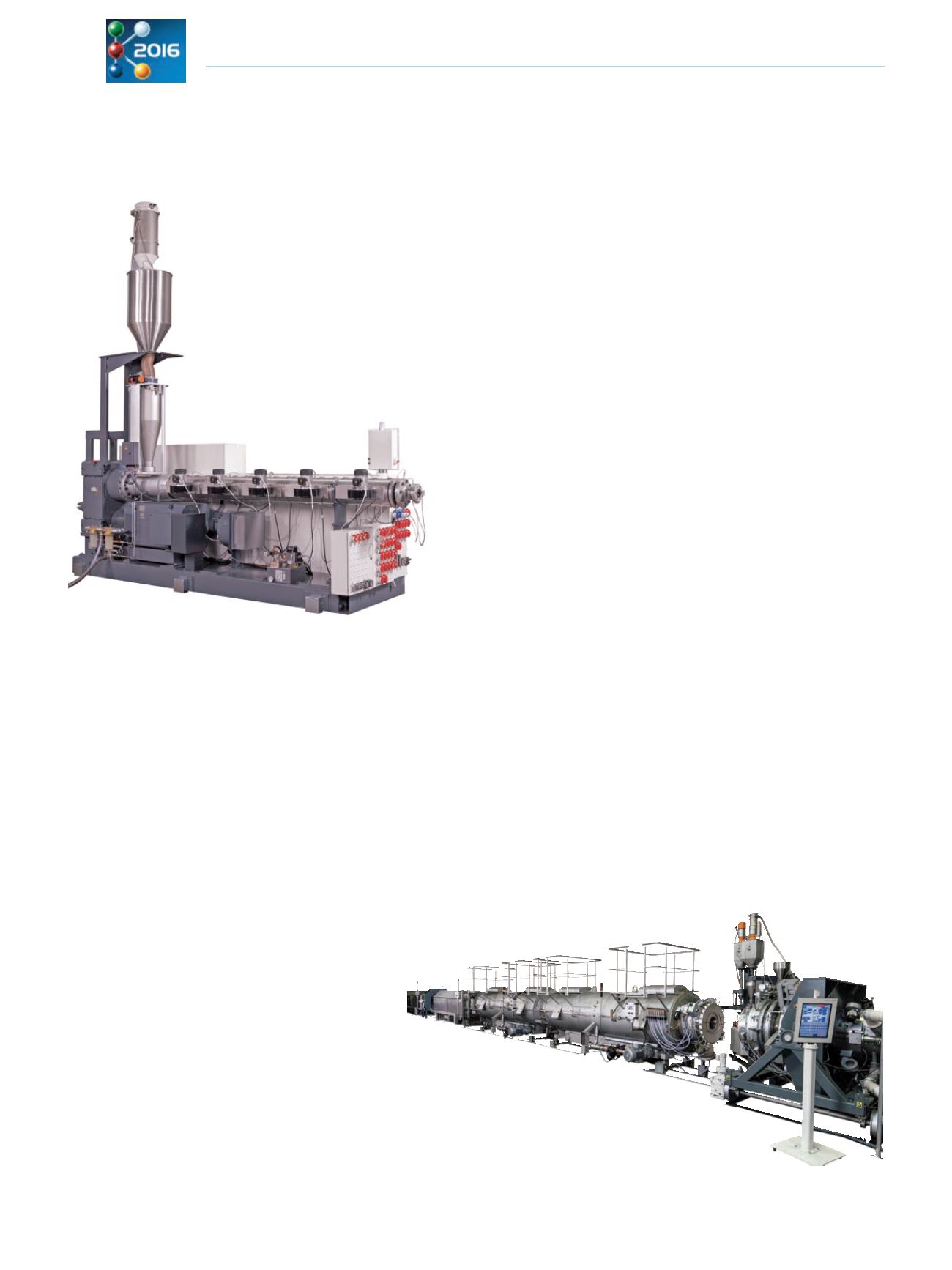
battenfeld-cincinnati:
“Driven by innovation”
T
he new single screw extruder solEX NG 75 for the production
of PO pipe will definitely be a highlight at the booth. Based
on solEX series, which is already established in the market, the
NG series offers a completely re-designed barrel-screw combi-
nation. With this, battenfeld-cincinnati sets new benchmarks in
the market in terms of output and energy consumption. The ad-
vantages of the “Next Generation” are lower melt temperatures,
optimized, con-stant pressure build-up and reduced mainte-
nance costs with sig-nificantly higher outputs compared to the
previous models. Thanks to the lower drive energy and reduced
energy losses, energy costs can be decreased by up to 15%.
“With the design of the new NG series we again prove our in-
novativeness. We have succeeded in developing an
extremely powerful and energy-efficient processing
unit that has not yet been seen on the market in this
form,” em-phasizes Grant Flaharty, battenfeld-
cincinnati’s Chief Sales and Marketing Officer.
In combination with the new PO extruder, the ma-
chinery manufacturer will show another innovation:
the Fast Dimension Change (FDC) system. At the
booth, three components will be shown – the pipe
head, the calibration sleeve and the vacuum tank.
With the FDC pipe head, die changes are largely un-
necessary, thanks to an adjustable melt gap. There-
fore, it can be used uni-versally for a wide pipe
diameter range. For the first time, an adapter for
the outer layer has been integrated in the adjustable
The solEX NG extruder series features a completely
new processing unit that offers a multitude of advantages,
such as a lower melt temperature and energy costs reduced
by up to 15%
The FDC (fast dimension change) system enables pipe dimension
changes during production. Three components of the system will
be shown at battenfeld-cincinnati’s booth: pipe head, calibration
sleeve and vacuum tank
Extrusion International 5/2016
42
die, offering the shortest purging times currently available, for
example during a color change. Instead of a rigid calibration
cylin-der, the FDC calibration sleeve consists of movable ele-
ments that can be adjusted to almost every diameter, but do not
leave any markings on the final product. Finally, the 1.5 m long
FDC vacuum tank has scissors lift tables that allow the adjust-
ment to every height with servomotors. A unique flexible and
above all easily adjustable sealing technology ensures a secure
sealing of the vac-uum tank.
Multi-Touch roll stack reaps success worldwide
“We have proven in the past years that we are optimally pre-
pared for the growth market packaging sheet with our high-
speed ex-truders and the Multi-Touch roll stack which is unique
in the indus-try. Customers all over the world have decided in
favor of this technology and we have installed numerous sys-
tems worldwide,” Dr. Henning Stieglitz, Chief Technology Offi-
cer, is pleased to report about the market success of
thermoforming sheet extrusion equipment. This is why the ma-
chinery manufacturer will show a Multi-Touch roll stack at its
booth – this time in a XXL-version. Multi-Touch roll stacks work
with a combination of a roll stack with two rolls for pre-calibra-
tion and three, give or seven rolls in post-calibration. So they
produce stress-free sheet with thickness toler-ances of
≤
1% at
high speeds. The newly developed XXL roll stack shows excep-
tionally high performance. Outputs of more than 3 t/h can be re-
alized depending on the width and thickness of the sheet while
at the same time there are no compromises in sheet quality.