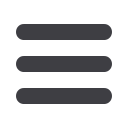
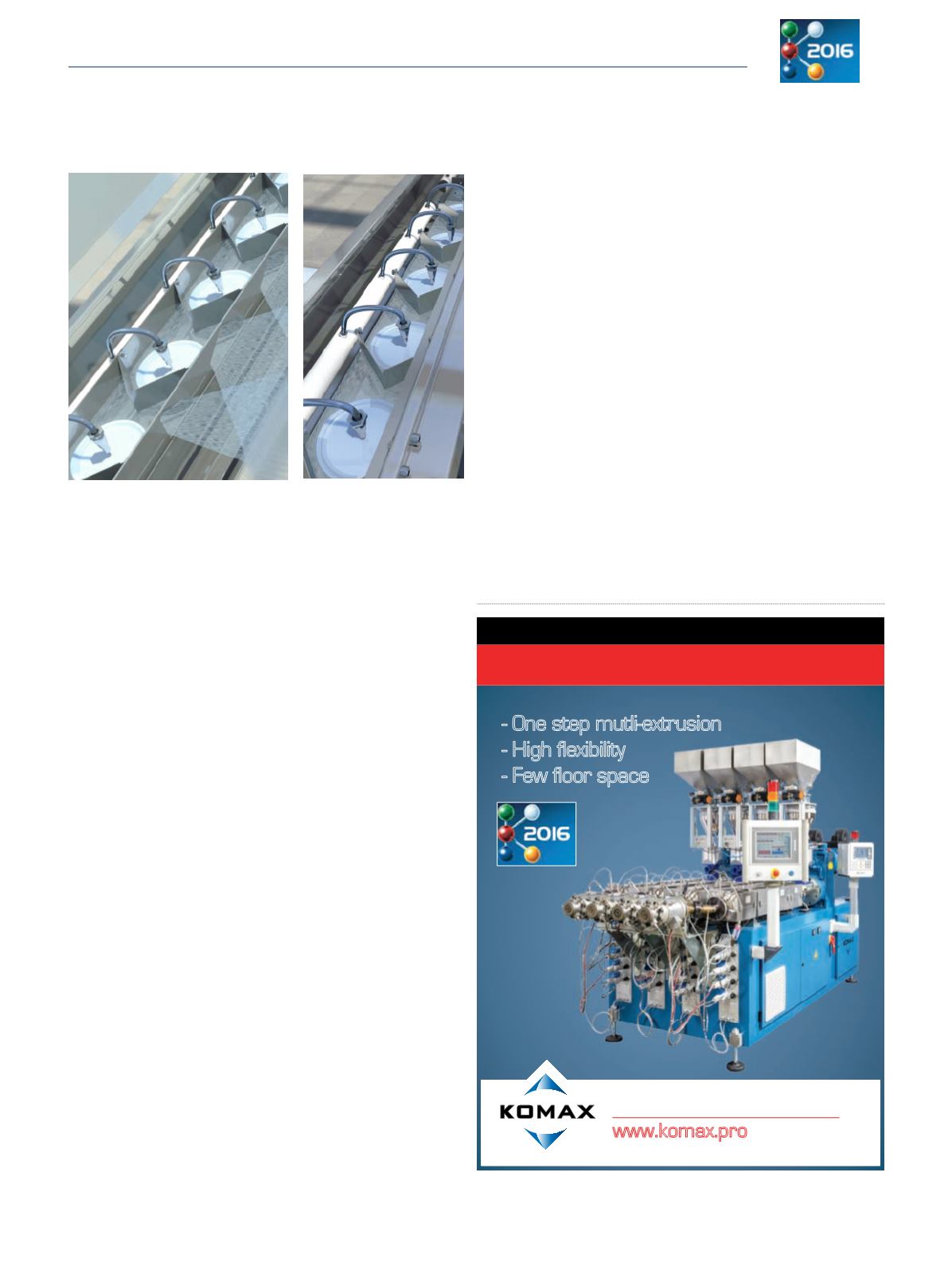
A
t the K fair 2016 in Düsseldorf, Weitmann & Konrad
GmbH & Co. KG showcases a variety of applications gi-
ving films special properties – true to the motto "Don't play
– work with precision!". The focus is on adding functional
properties to films through non-contact spray application of
anti-blocking, anti-fog or anti-static additives. Anti-curling
uses and the application of primers supplement varied the
application options.
The WEKO motto "Don't play - work with precision!" un-
derscores the fact that the WEKO-Fluid-Application-System
is no gadget but a high-precision system applying finishing
chemicals exactly metered and clean onto the plastic film
web. WEKO – on the market for more than 60 years – has
specialised in pre-cise and non-contact applications of mini-
mal liquid or powder quantities on plastic film and other ma-
terial webs. Many flexible films are finished with special
surface-active substances to opti-mise the physical proper-
ties. Many of the world’s renowned plastic film manu-factu-
rers already rely on the WEKO coating technology and
achieve significant cost and quality advantages compared to
the use of batch additives.
The extruded film webs are finished with a very thin liquid
functional coat im-mediately following the extrusion process.
Contrary to batch additives external coating neither affects
the behaviour of the melt in the extruder nor the flow cha-
racteristics at the extrusion nozzle and not even the barrier
effect, and thus the thickness of the different film coats. The
function is effective immediately after application and retains
its effective-ness continuously even after very long storage
periods. Another advantage is that the film retains its trans-
parency, entirely without opaqueness.
Release agent application – the classic
WEKO application systems are most often found in the area
of release agent coating of PET film. These thicker single or
WEKO:
functional coatings for plastic films
multilayer films are used for ther-moforming trays. When ma-
nufacturing products by thermoforming, silicon emulsions
make it easier to release the trays from the moulds and to de-
stack the final products. Thanks to the minimal and very exact
application of anti-blocking agents uniform and high-quality
plastic trays are produced. At the same time, the thermofor-
ming process represents cost benefits by increasing the cycle
rates, reducing downtimes and minimising the release agents
used.
Polyolefins – the divas
Naturally, in addition to PET films, polyolefin products can also
be coated. Be-cause of the surface energy water-based coating
of polyolefins usually re-quires corona pre-treatment. From a
surface energy of the film of 38-40 mN/m very thin, uniform
coats can be produced with dry thicknesses in the nanome-tre
range. Common applications in this area are anti-fogging, an-
tistatic and antibacterial coats.
Another use is the reduction of curling effects of co-extruded
blown and flat films. Due to different cooling characteristics of
the individual film layers, ten-sions – and thus significant rolling
Extrusion International 5/2016
71
0 X O W L 6 W U D Q G ( [ W U X V L R Q / L Q H
+ ( / , % $ 5
7 ( & + 1 2 / 2 * , (
2QH VWHS PXWOL H[WUXVLRQ
+LJK IOH[LELOLW\
)HZ IORRU VSDFH
UXH GX 0DLQH
:,77(1+(,0
7pO
)D[
ZZZ NRPD[ SUR
LQIR#NRPD[ SUR
Hall 16
Stand B19