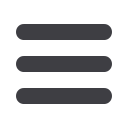
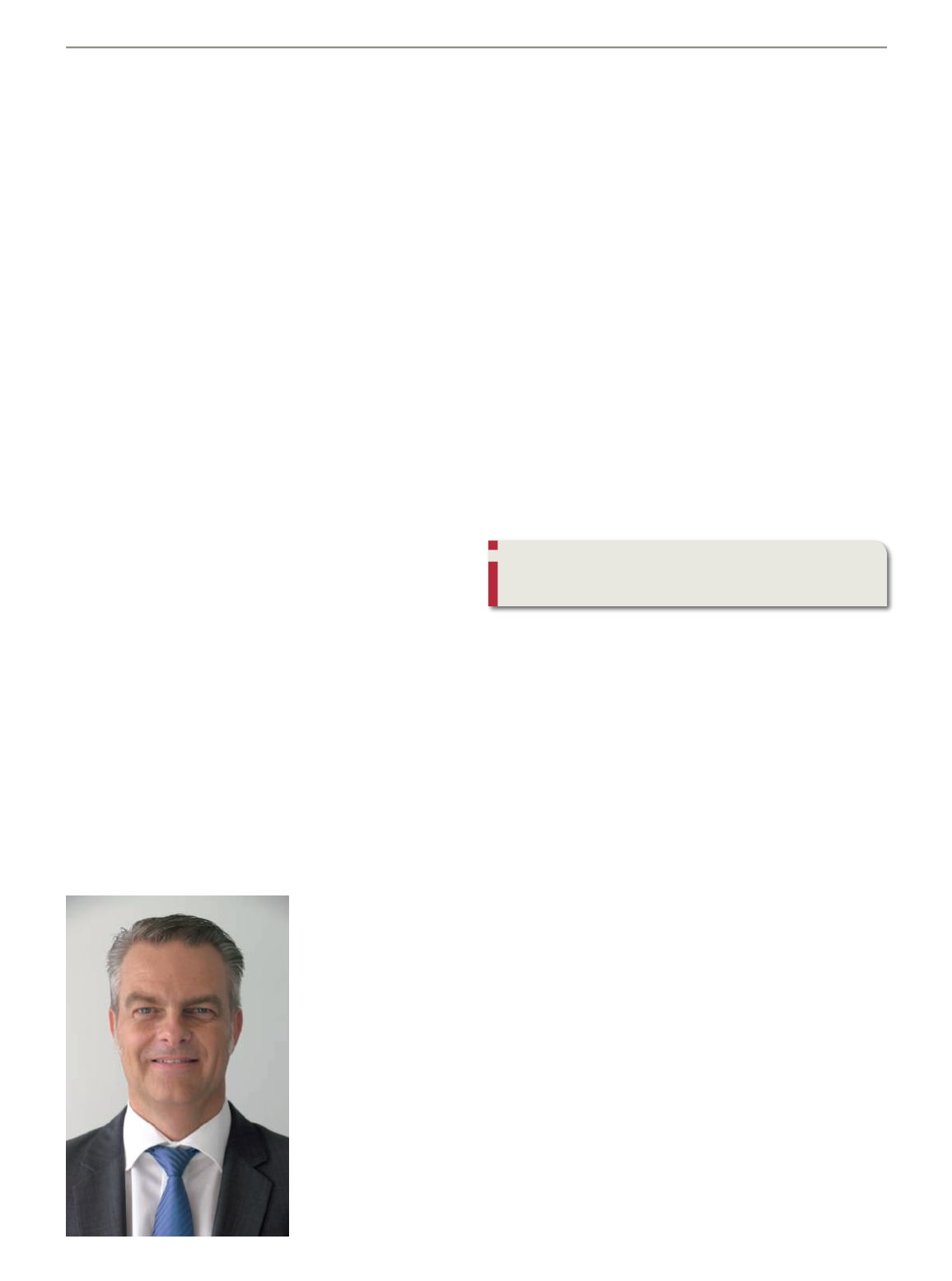
A
ll the new MacroPack™ blown film dies feature stream-
lined material flow passages and reduced wetted surface
areas. Both features can help customers reduce purge time by
up to 50%, and widens the process window by 30 to 40%
compared to competitive designs in the field. MacroPack™ dies
have diameters of 3 to 80 inches (76 mm to 2.0 m) and can
produce films 20 to 300 microns thick, in constructions of up to
24 layers depending on the applications.
The MacroPack-TP die is designed to have three times less bolts
than competitive dies of similar sizes. It is easy to clean and
maintain. It is often used with double-bubble technology but
can also be used for regular blown film of smaller diameter
tubes from 3 to 11 layers.
The MacroPack-CP die is designed for mainly polyolefins appli-
cations with reduced wetted surface area for quick material
changeover. It is available in diameters from 8 to 40 inches
(200 mm to 1.0 m) and produces films of up to five layers. The
innovative design which eliminates the use of a traditional
feedblock minimizes pressure drops in the die. This broadens
the process window of the die, as well as shortening the purge
time. Compared to competitive dies of similar designs, the
MacroPack-CP die reduces pressure drops by about 20%.
Macro’s MPC die features a tapered mandrel, and is the only
die in the field to have a self-centering assembly; this is crucial
especially in large diameter dies to prevent non-concentric bub-
ble shape. The special design uses up to half the bolts of com-
peting dies of the same sizes for ease of maintenance. The pro-
prietary design features a large area in the center that is not
available in the traditional stackable or the concentric dies. This
allows an optimal air exchange for high-throughput internal
bubble cooling (IBC) applications as well as large diameter bub-
bles such as in the agriculture and geomembrane applications.
This die is available up to 80 inches (2.0 m) in die diameter and
produces films of up to 11 layers.
MacroPack-FP coextrusion die not only has flow mixing chan-
nels to improve temperature uniformity in the die, but it also
has round channeled flow passages to improve purge time and
melt quality. This die is designed especially for running barrier
materials such as EVOH, Nylon, PVdC and PETg. Due to the
special features of this design, the transition time between Ny-
lon and PE can be as short as 15 to 20 min. In other competitive
dies, the comparative purge time can be from 45 min to 12
hours. This die can also be used in special applications contain-
ing up to 24 layers.
Chinaplas 2016: Booth W1 S21
2016中国国际橡塑展 展台号 W1 S21
Macro Advanced Extrusion Systems
199 Traders Blvd E, Mississauga, Ontario, Canada L4Z 2E5
www.macroeng.com, www.macrotech.ca,
软包装在亚洲市场的趋势和发展
Film Technologies at Chinaplas 2016:
Trends and Developments in the Asian Flexible
Packaging Market
软包装在亚洲
是一个不断扩展的
市场。采访中,德
国温德默勒与霍尔
舍公司的亚太区首
席执行官 Michael
Fischer先生谈到亚
洲市场的重要性,
在工业领域的发展
以及2016 年中国国
际橡塑展的创新。
Michael Fischer,
CEO Asia Pacific at
Windmöller & Hölscher
Flexible packaging is a growing market in Asia.
Michael Fischer, CEO Asia Pacific at Windmöller &
Hölscher, talks about the importance of the Asian
market, the trends in the industry and the innova-
tions shown at Chinaplas 2016.
Mr. Fischer, Chinaplas 2016 is coming up – how is the mar-
ket for flexible packaging in Asia-Pacific developing?
Rising expectation on quality, productivity and sustainability
gave a boost to the already growing market of flexible pakkag-
ing. More and more rigid packaging solutions like glass bottles
are being replaced by flexible ones, always considering environ-
mental friendly raw materials to be used. PVC products were
replaced by PP and HDPE. These developments fueled the
growing importance of the flexible packaging market.
Which technological trends where especially important
during the last years?
There are a few important developments, especially driven by
28
2016中国国际橡塑展上的薄膜技术
Extrusion Asia Edition 1/2016