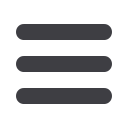
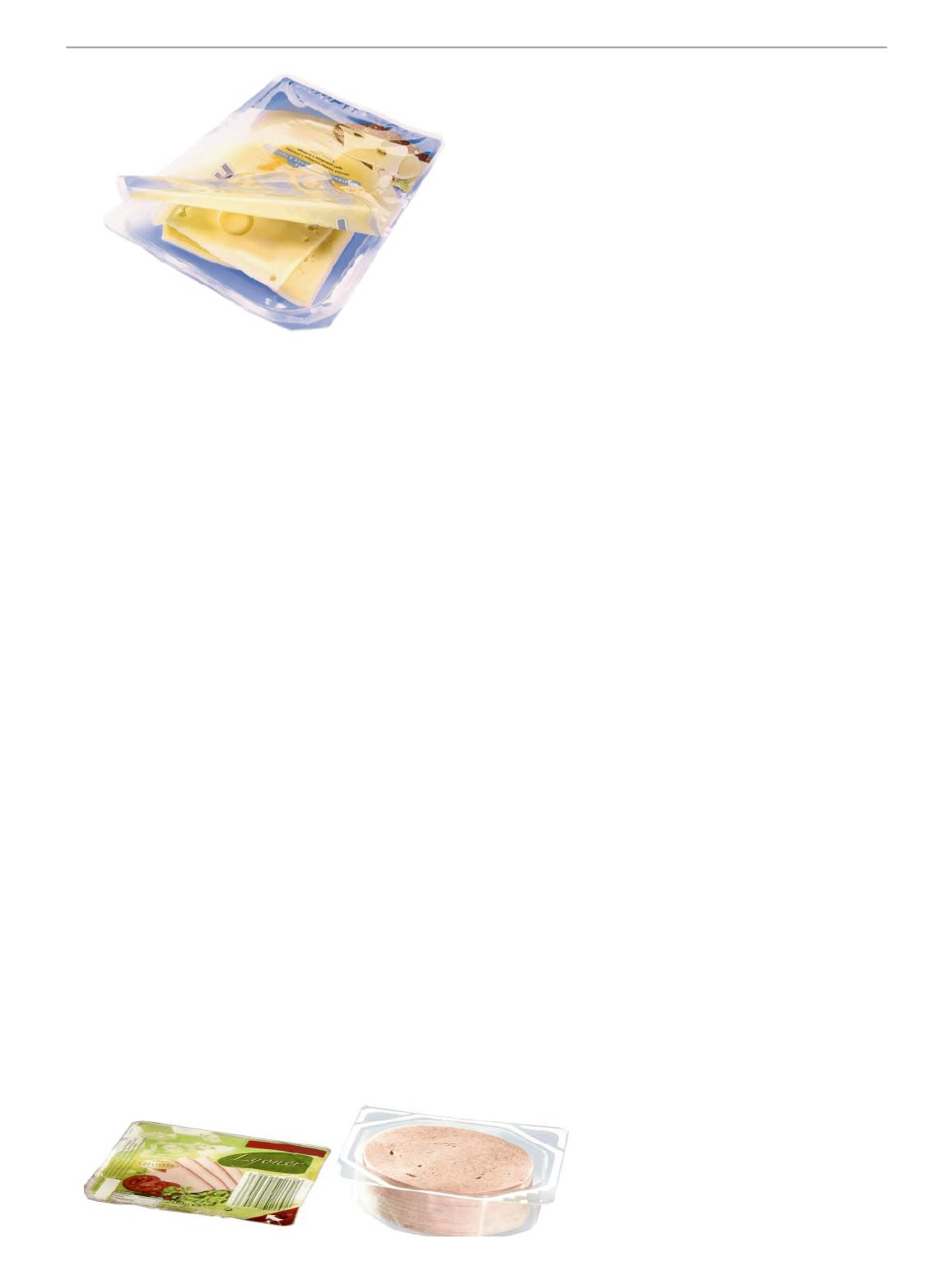
数量巨大的各种各样用途的原材料。对高度的灵活性起关键
作用的是细川阿尔派新的拥有专利的X系列11层模头。作为
吹膜生产线制造行业市场领袖之一,该公司以非常成功的X系
列模头为基础,开发出了11层螺旋流道分配器共挤模头。 模
头设计的关键点在于使挤出生产线从11个同等的层次结构中
获得巨大的灵活性。各层结构可以有着无穷无尽的变化,原
料的适用性也涵盖了宽广的范围。尽管任意一台挤出机所采
用的原料有着非常不同的粘度,各式各样的原料也可以进入
任何一层,而不需要更换螺杆。不管是对称结构的薄膜(例
如复合基材膜)还是非对称结构的薄膜(例如应用于热成型
的薄膜)都是可以生产的,同样,各层结构的厚度可以是相
同的也可以是非常不同的。较厚的层,例如采用低成本原料
的层,可以采用相邻挤出机挤出相同原料的方式,形成相邻
层。
最后一点然而同样重要的是:11层生产线层数的增加提
供了全新物料组合的可能性,并因此而导致减小层厚和节省
成本,或者可以开发出新的产品,例如不再需要采用下游设
备进行复合的薄膜产品。
不到一年即可摊回投入的成本
为确保能够在生产的条件下充分利用极大的灵活性,在
模头的设计阶段就对快速物料转换和缩短清除时间给予了极
大的关注。例如,从采用11层生产线生产PE薄膜转换到生产
高阻隔薄膜,所需要的时间可以缩短到一个小时以内。为了
使客户自行证实这一点,细川阿尔卑那在其具备测试条件的
客户测试中心开机运转11层吹膜生产线。在这条生产线上,
可与客户一起,实际生产新结构的薄膜 ,同时还可与原料制
造商一起,开发新的原料和原料组合,并研究新原料的加工
特性。
采用11层生产线实现了高度的灵活性,下面的例子体现了生
产线是物有所值的:
lity, not only in respect of 5 to 11 layer barrier films but also in
respect of the enormous versatility of raw materials. Primarily
responsible for the high degree of flexibility is the new 11 layer
die head of the patented X Series from Hosokawa Alpine. One
of the market leaders in the field of blown film lines the com-
pany developed a co-extrusion die head with 11 spiral distribu-
tors based upon the highly successful X-die heads. The focus of
the die head design was the enormous flexibility of the extru-
sion line which is facilitated by 11 equal layers. An unprecen-
dented variety of layer structures is possible as the whole spec-
trum of suitable materials despite their very differing viscosities
can be employed in any of the extruders and thus any layer
without changing the screw. Both symmetrical for example for
lamination film and asymmetrical structures for thermoforming
applications are possible as well as layer structures with equal
or very differing layer thicknesses. Thicker layers, for example
from low cost materials, can be achieved by extruding the same
material through neighbouring extruders and hence neigh-
bouring layers.
Last but not least the increased number of layers of an 11 layer
line offers the possibility of completely new material combina-
tions which could lead to a reduction in layer thickness and re-
sult in cost savings or enable new products to be developed
which e.g. eliminate the need for downstream lamination.
Amortisation in less than one year
To ensure that the enormous flexibility can be fully exploited
under production conditions short material change-over and
purging times were given a great deal of attention in the design
phase of the die head. For example the change over from a PE
film, which of course can also be produced on an 11 layer line,
to a high barrier film can be achieved in less than one hour. To
enable customers to verify this themselves Hosokawa Alpine
operates an 11 layer line in their customer test center which is
available for customer tests. On this line, together with custo-
mers, new structures are implemented and, with raw material
manufacturers, new materials and material combinations are
developed and their process properties investigated.
That the flexibility achieved with an 11 layer line is affordable is
shown by the
following example
:
Based upon the assumption that the personnel requirement
and energy consumption per produced kilogram of film remain
constant a production comparison between a 2000mm wide,
40µm thick film with a symmetrical 9 layer structure and an 11
layer film with the same dimensions is made. The layer struc-
ture is as follows:
5 % mLLDPE, 33 % LLDPE, 5 % TIE, 5 % PA, 4 % EVOH, 5 %
PA, 5 % TIE, 33 % LLDPE und 5 % mLLDPE.
With the 9 layer film a maximum output of
420 kg/h can be achieved whereas with the
11 layer film the output is 30% higher at
550kg/h. The higher output is achievable
with the 11 layer structure as the two indivi-
dual LLDPE layers in the 9 layer structure are
each replaced by two neighboring layers
with each layer totaling 16.5% layer ratio.
Thus higher outputs are possible as the limi-
ting factor is the throughput in the melt
高阻隔薄膜用于食品包装
High barrier film for food packaging
高阻隔封盖薄膜
High-barrier lidding film
32
2016年中国国际橡塑展上展出的薄膜技术
Extrusion Asia Edition 1/2016