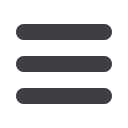
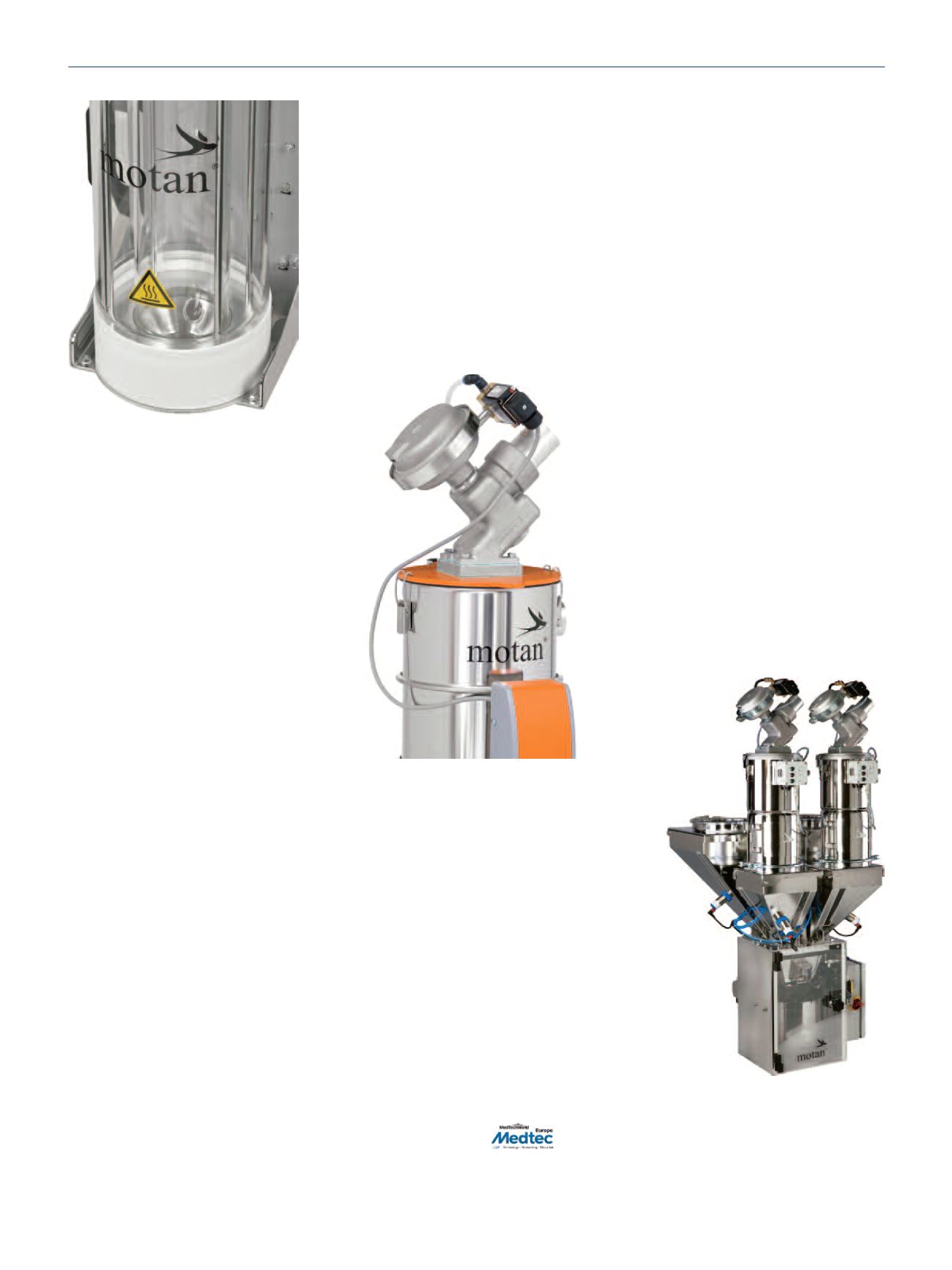
Extrusion International 2/2016
37
www.motan-colortronic.defeature prevents con-
tamination of high-
quality materials and
provides optimum dry-
ing conditions. The
complete drying bin
body is made from a
single piece of special
glass – ideal for con-
tamination critical
process applications.
An additional benefit of the all glass con-
struction is its transparency. The operator can
always see the actual status of material in the
bin. Constant and stable conditions in the en-
tire drying hopper are an essential prerequi-
site. Therefore, the complete drying hopper
right down to the material discharge is heat
insulated because of a double glass wall con-
struction. This design is an important energy
saving advantage. The expertly designed air
diffuser provides uniform distribution of the
dry air ensuring that the material – even at
the material bin outlet – is kept at a constant
temperature and in the required dry condi-
tion.
METRO G
motan-colortronic's spotlight this year will be
focused on its innovative METRO G range of material loaders.
This development by motan engineers combines the latest tech-
nologies from colortronic and motan and also enhances those
systems with a number of new features. METRO G's modular
building block system allows users to configure and create the
optimal material loader for any application. For example, a stan-
dard material loader unit can be expanded into a clean room
version just by adding special vacuum diaphragm valve. A dust
removal module provides for fine dust removal at the material
loader, essential for some critical engineering plastics where ab-
solutely no dust is allowed to enter the process. The system can
also be fitted with modules with a tangential material inlet to
provide a cyclone effect for processing those materials where a
more coarse dust separation is required. METRO G allows users
to configure the right material loader for their specific applica-
tion.
ULTRABLEND
ULTRABLEND offers clear advantages to manufacturers of ther-
moplastic medical devices. The processing of raw material com-
pounds that are sometimes extremely expensive in hygienically
clean operations into medical primary packaging, components,
implants, instruments and equipment requires the highest levels
of cleanliness, precision and cost discipline.
The gravimetric ULTRABLEND blender has been developed for
consistently precise dosing and mixing of free-flowing raw ma-
terials – plastic granulates and additives. It improves process
quality and stability and makes its own contribution towards
minimising production costs. With the design in electro-polished
stainless steel, motan has placed great emphasis on clear func-
tions, minimum maintenance and easy operation in a hygieni-
cally clean production environment. All material hoppers and
mixing chambers have been designed without any “dead
zones”. All seams are fully welded. As a
result, no residual amounts of material can
build up and contamination of subsequent
batches is therefore eliminated.
The ULTRABLEND is especially suitable for
precise dosing of extremely small amounts
of material directly into the injection
moulding, extrusion or blow moulding
machine. A maximum of four raw mate-
rial
components can be
dosed by weight, one
after the other, precisely
as required by the recipe.
They are then mixed to-
gether homogeneously
in the downstream mix-
ing chamber (4.5 litres
volume) and fed into the
feed throat of the pro-
cessing machine. The
minimum dosing amount
is 3 g per component
(900 g lot size).
When two components
are used a maximum
throughput of 260 kg/h can be achieved.
LUXOR CA S
Membran valve for clean
room applications
ULTRABLEND
Hall 7, Stand 7C16