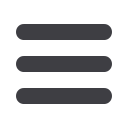
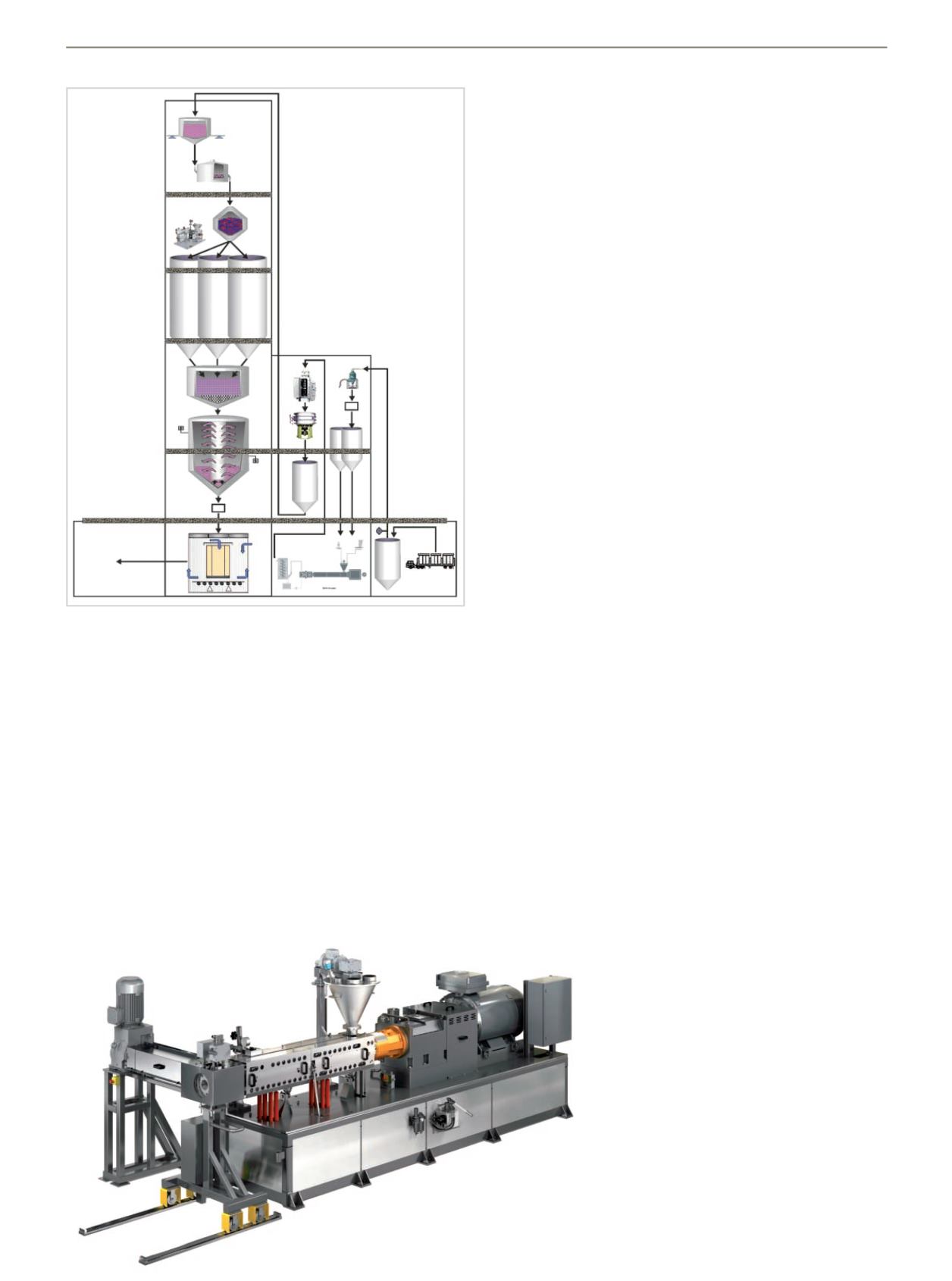
When BUSS initially discussed the project with the customer
some years ago, it rapidly became clear that this producer was
looking for a one-stop shop, providing a single-source turnkey
line, from preliminary planning to final realization, commission-
ing, start-up and acceptance.
BUSS’ engineers and process specialists accordingly developed
a detailed concept for the entire plant and its components, in-
cluding a BUSS Kneader, melt filtration, hydraulic conveying
system and peroxide absorption modules. Special attention was
paid to all aspects of production under cleanroom conditions.
Work and product flow were optimized in close cooperation
with the future plant operators. The new compounding line
(
figure 1
) comprises two stages:
• Compounding and screening
• Peroxide absorption
Compounding and Screening
The feedstock for the XLPE compound is a low-density poly-
ethylene (LDPE) in pellet form, stored in a cleanroom – together
with high-purity additives and stabilizing agents – for subse-
quent gravimetric dosing to the BUSS Kneader (
figure 2
).
Using BUSS’ well-proven compounding technology, the LDPE
pellets and the additives (excluding the peroxide) are melted
and dispersed in the BUSS Kneader, avoiding any de-gradation
of the polymer chains. The required discharge pressure is gene-
rated via a melt pump flanged to the Kneader. This is followed
by ultrafine melt filtration and underwater pelletizing of the re-
sulting high-purity intermediate compound.
To meet high-purity requirements, the water used in the process
is deionized and filtered to eliminate any possible contamination
(
figure 3
). All mechanical components comply with the same
high cleanliness requirements, some of them being specially de-
signed. Only abrasion and corrosion resistant materials are used,
and all surfaces in contact with the product are highly polished.
Peroxide absorption
Immediately after pelletizing, the intermediate compound is hy-
draulically conveyed to the upper level of the building, avoiding
abrasion and fines generation. Here the second processing
stage starts, using gravity for all further con-
veying and movement of the material.
In this stage, the purified intermediate com-
pound is converted into ready-to-pack XLPE
granules, used for producing power cable
electrical insulation. The associated peroxide
absorption and diffusion step takes place in
what is known as the absorption tower
(
figure 4
).
The peroxide absorption process has four
main zones (
figure 5
):
• Dewatering the intermediate compound in
a centrifuge and drying.
• Wetting with peroxide, using a high-preci-
sion pump dosing system. The product is loa-
61
Extrusion Asia Edition 1/2016
(图2),生产线采用了布斯公司极为成熟的原料混合技
术。LDPE粒子和添加剂(不包括过氧化物)在混合机内被融
化并且被非常温柔地混合,避免了任何高分子链的降解。融
体泵通过法兰连接到混合机,所需要的送料压力由融体泵建
立。融体泵的下游就是超细融体过滤器和生产出高纯度中间
料的水下造粒机。
为了满足高纯度的要求,工艺用水经过了去离子化,并
且进行过滤以剔除任何可能的污染物(图3)。 所有机械部
件都遵守同样高的洁净度要求,有些还进行了特殊的设计。
仅仅使用抗磨损和耐腐蚀的材料,所有接触混合料产品的表
面都进行了高等级的抛光处理。
过氧化物的吸收
造粒之后,中间料立即由水力输送到建筑物的上一层,
避免了磨损和任何污染物。在这里,开始第二阶段的加工。
图1. 高纯度XLPE生产线概览
Figure 1: Overview of high-purity XLPE production
Figure 2: BUSS Kneader used
for compounding and screening
图2: 用于混合和过滤物料的布斯
混合机
吸收塔
Absorption Tower
仓库
Warehouse
混合生产线的建筑物
Compounding Building
接收原料并
进行除尘
Raw Material
arrival
Dedusting