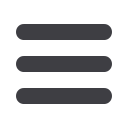
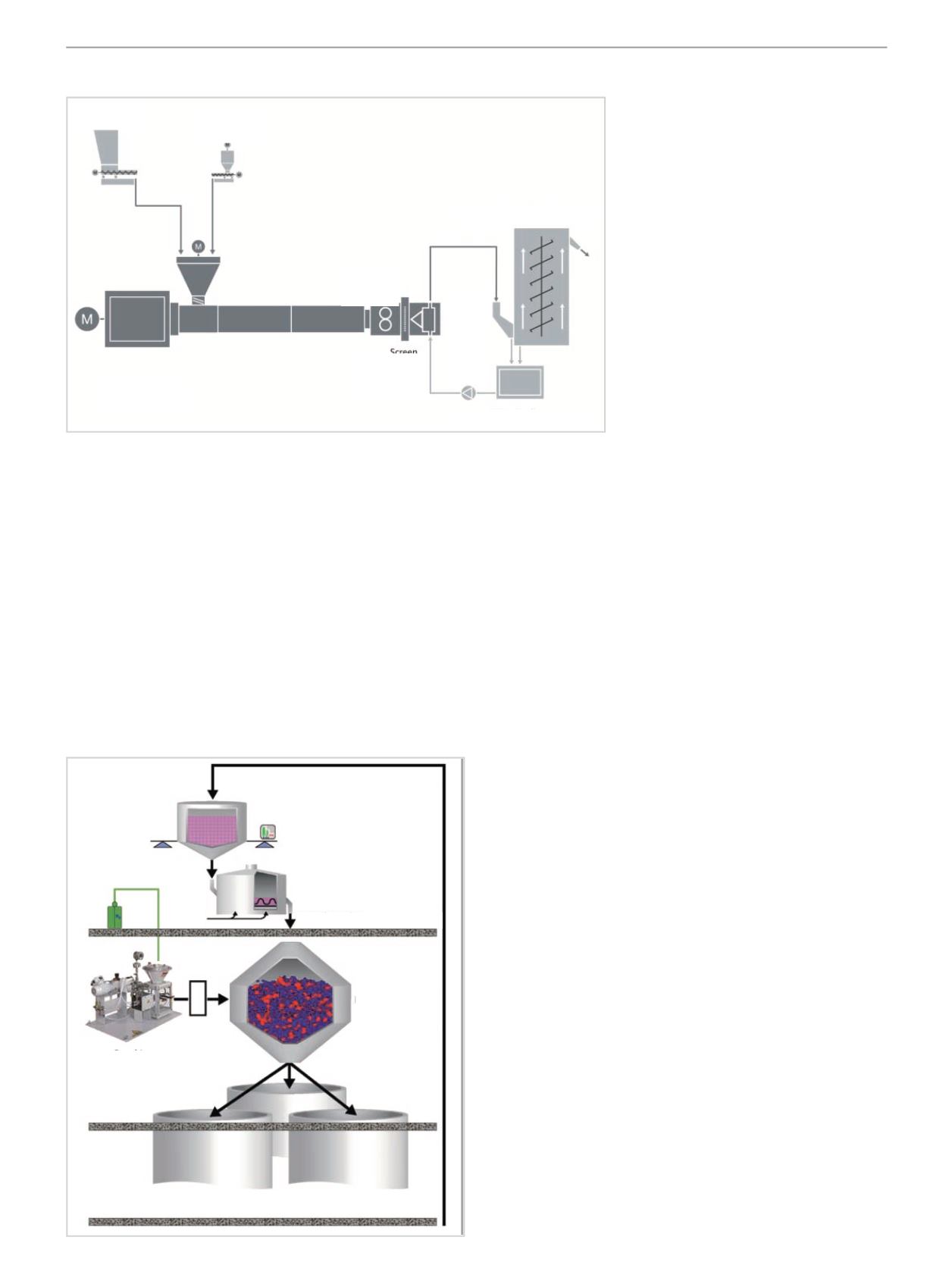
接下来,物料的所有输送和移动都采用重力方式完成。在这
一阶段,精制的中间混合料将转换为等待包装的XLPE颗粒料
,产品可用于生产电力电缆的绝缘层。原料的过氧化物吸收
和 扩 散 的 综 合 过 程 在 被 称 为 吸 收 塔 的 装 置 中 进 行
(图4)。
过氧化物的吸收过程包含四个主要的过程(图5):
• 采用离心机对中间混合料进行脱水和干燥
• 使用高精度计量泵系统添加过氧化物,润湿中间混合料。产
品装填到经过特别设计的慢速移动并带温度控制的混合器
中,混合器避免了接触原料的金属部件的相关移动。在这
里,液态的经过过滤的过氧化物在确定的时间精确地注入到
中间混合料中,并与其均匀混合。
• 中间混合料的表面涂覆了过氧化物,然后进入到可加热的吸
收罐,精心安装的吸收罐可以使热损失降到最低并保持恒
ded into a specially designed slow mov-
ing, temperature-controlled mixer, which
prevents relative movement of the metal-
lic parts coming in contact with the pro-
duct. Here, the liquefied and filtered per-
oxide is precisely injected over a defined
time and uniformly mixed with the inter-
mediate compound.
• Surface-coated with peroxide, the inter-
mediate compound enters a heatable ab-
sorption tank, which is well insulated to
minimize heat losses and maintain a cons-
tant temperature. Thanks to its special de-
sign and mode of operation, the material
flows down with a narrow residence time
distribution, whilst the peroxide diffuses
uniformly into the pellets.
• After leaving the absorption tank, the
pellet temperature is reduced quickly to an atmospheric packa-
ging temperature. The finished product then passes through a
highly sensitive metal separator, being ready for packaging un-
der cleanroom conditions to eliminate any potential risk of con-
tamination during transport.
Special aspects of XLPE production purity
BUSS has used its know-how and experience to design the en-
tire line as a self-enclosed system, providing the XLPE granules
with the level of purity required for HV cable insulation and en-
suring that every single production step takes place under the
specified clean conditions. Since it is human factors which par-
ticularly complicate maintaining cleanroom conditions – people
bringing in contaminants despite airlocks and protective cloth-
ing – BUSS has designed the entire line to be operated with mi-
nimum access by personnel. The process runs fully automatical-
ly with there being no need to access any part of the produc-
tion line under normal operating conditions.
Apart from the production monitoring and control system, pro-
duct quality is checked systematically using strict sampling and
record-keeping procedures. Samples are taken from several
plant locations to monitor quality trends. These samples are
analysed simultaneously and systematically in the plant labora-
tory. Beyond operating under very clean conditions, this innova-
tive XLPE granulate production line has further outstanding
features:
• The plant is fully enclosed and uses state of the art air ma-
nagement systems.
• Hydraulic transport and subsequent gravity feeding ensures
minimal damage to pellets with little or no fines generation.
When first commissioned, an XLPE production line has to be
operated for two to four weeks before meeting the product
purity level demanded for HV cable insulation. Despite all the
precautions taken during manufacture with respect to compo-
nents in contact with the product, and despite thorough pre-
cleaning after assembly, it is only then that the residual conta-
62
混料设施
Extrusion Asia Edition 1/2016
图4:第二阶段生产示意图,加入过氧化物
Figure 4: Schematic layout of production step 2, peroxide
introduction
预称重罐
Pre Weight Tank
热空气
Hot Air
过氧化物融化单元
Peroxide Melting Unit
过滤
Filtration
热粒子出口
Hot Pellet Outlet
预热罐
流化床
Pre Heat Tank
Fluidized bed
批次混合器
Batch Mixer
图3: 第一阶段生产示意图,融体泵换网器和水
下造粒
Figure 3: Schematic layout of production
step 1 with melt pump, screen changer and
underwater pelletizing
高分子材料
Polymer
添加剂
Additives
布斯混合机
BUSS Kneader
融体泵
Melt pump
换网器
Screen changer
水下造
粒机
Under
water
pelletizer
水箱
Water tank
粒子干燥机
Pellet dryer