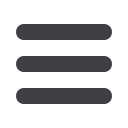
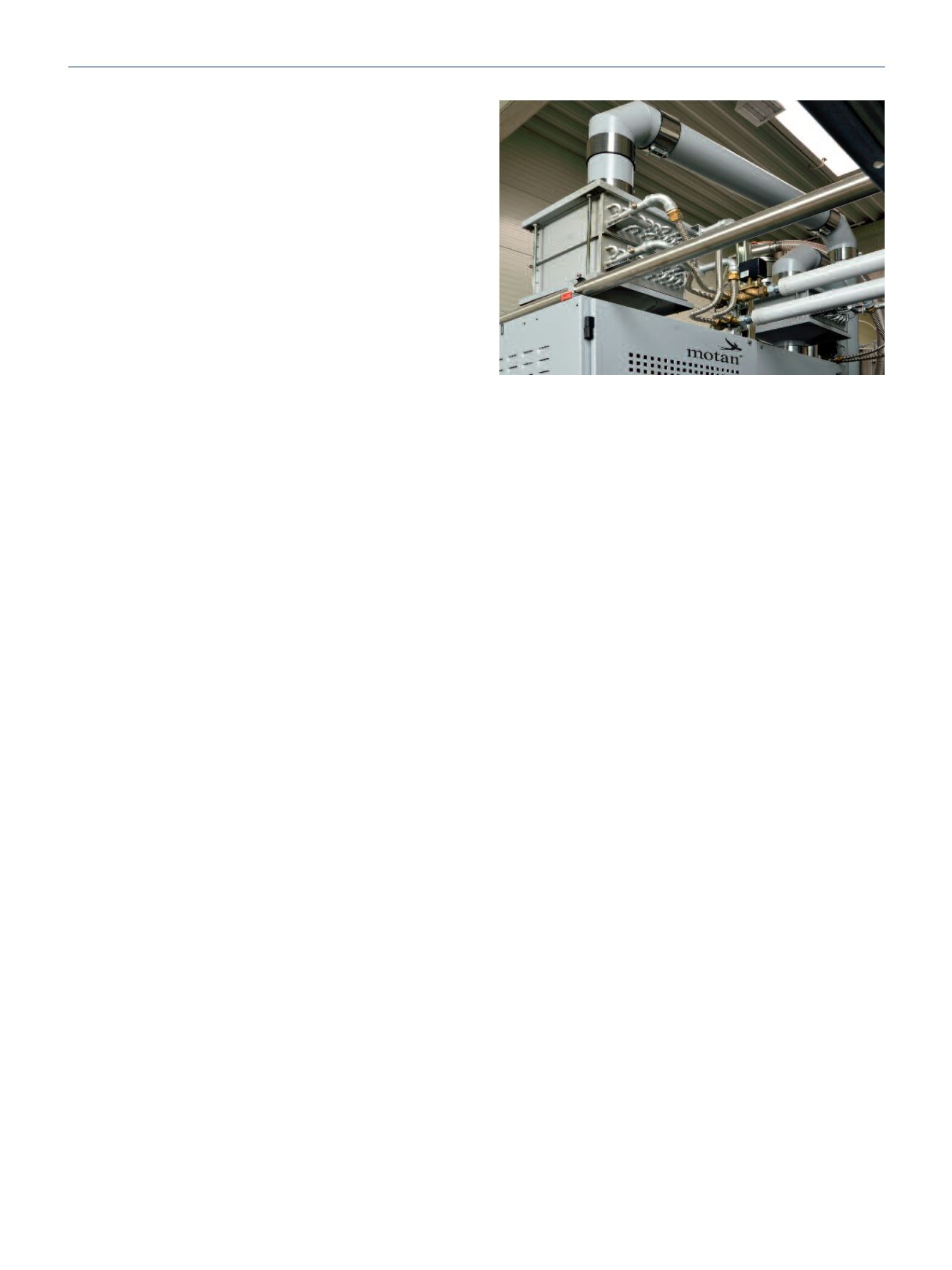
Extrusion International 1/2016
39
www.motan-colortronic.deFKT mainly assembles fabrics, nets, aluminum profiles - and
plastic injection moulding parts - into complex assemblies at
the location Pförring near Ingolstadt. In the last few years the
injection moulding sector was completely rebuilt, in September
2015 there were eleven machines up to 3000 kN clamp force
in use, further expansion is already being planned. From the
start of the injection moulding, a system by motan for the ma-
terial drying was installed.
As a distinctive feature FKT operates a cogeneration plant with
wood chips combustion for generation of district heating,
which also supplies several companies and buildings in the
area. FKT also uses the low-cost district heating through a
buffer tank for tool heating. In addition, the external heat sup-
ply was integrated into the granule drying. "We have accom-
plished this with motan-colortronic in the first expansion
phase" explains CEO Guido Günthner. The drying system with
13 Luxorbin A drying bins of various volumes and a coupling
station by motan-colortronic form the heart of the central ma-
terial supply at FKT. The energy supply of the drying system
demonstrates high environmental expertise: A dryer of type
Luxor A 900 feeds the drying bins with dry air, which is heated
by the heat exchanger from the district heating supply. Only
when temperatures above 80 degrees are required, does the
temperature difference get generated by conventional electri-
cal heating. For polyamide GF50 variants, for example, the dif-
ference is typically only 20 degrees. Some engineering plastics
processed in smaller quantities require drying temperatures
that are slightly over 100 degrees. Despite this unusual con-
figuration, the entire control and monitoring, including the one
of the heat exchanger was mapped by mere configuration in
the standard controller software of the motan dryer equipped
with ETA plus technology. ETA plus automatically regulates the
air temperature and volume depending on drying parameters
and extraction volumes. The energy supply is thus continuously
adapted to the actual demand - even with a reduced work-
load. The exclusive use of the standard software - in spite of
the very special conditions - creates investment security for the
customer, since software updates and future enlargement do
not require individual adjustments. There are already plans for
connection to a central control center.
Simple infeed of ground material
FKT processes predominantly reinforced materials with high
abrasiveness. Accordingly, the elbows of the conveyor system
and the coupling station were made out of glass. Similarly,
glass inserts are available in the drying bins to keep mainte-
nance costs minimal and achieve high process reliability. The
coupling station provides 13 inlets and six outlets. Occasionally,
a total of five mini color dosing devices of motan are used, to
be able to dose additives directly on the machines. These dos-
ing units can be exchanged freely between machines, suitable
adapters are available everywhere.
At FKT the use of ground material is the rule: Sprues are
ground directly on the machines and added to the virgin ma-
terial. Otherwise, a central grinding is used. The motan con-
veyor system sucks directly from the mill and routes the ground
material into the ongoing processes. The Metro HCG convey-
ors used have two inputs as a standard feature, the controller
can also use these in the standard. Additional switches are not
required. With 13 drying bins, FKT has comparatively high ca-
pacities and the ability of keeping a large part of the material
available parallel with an optimum degree of dehydration. The
typically small batch sizes of an average of only 4,000 to 5,000
pieces at FKT require an even faster and easier set-up than in
other injection mould productions in order to keep costs under
control. This especially applies to the central material supply: In
addition to the possible diversity of materials in the system, the
planners give special importance to fast cleaning, except for
maintainability, expandability and the possibility of integration
in the extraordinary FKT energy concept. When the material is
changed, the system is completed sucked empty, via the ex-
traction boxes below the bins they are emptied over a short
distance. Central material drying and supply are key building
blocks for FKT's efficient injection moulding production. Their
reliable, trouble-free and low-maintenance operation is an in-
tegral part of the expanded production with its exceptionally
small series for an automotive supplier, which has been built up
in the space of a few years.
FKT in Pförring
FKT predominantly delivers assemblies on average in rather
small numbers to the Volkswagen Group and BMW. After
changes in the ownership structure, the family business has re-
aligned its strategic focus since 2008: The mere assembly op-
eration changed in a few years into a system supplier of wide
vertical range of manufacture and comprehensive develop-
ment activity. Idea development, design, validation, production
and assembling are typical for the most current products. This
includes wind deflectors for convertibles, shading systems for
passenger cars and mobile homes as well as a number other
optically and functionally sophisticated assemblies that are pro-
duced in rather small series.
Dosing devices are only used depending on the order, adapters
are available on all machines. This reduces the investment costs