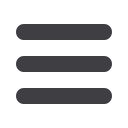
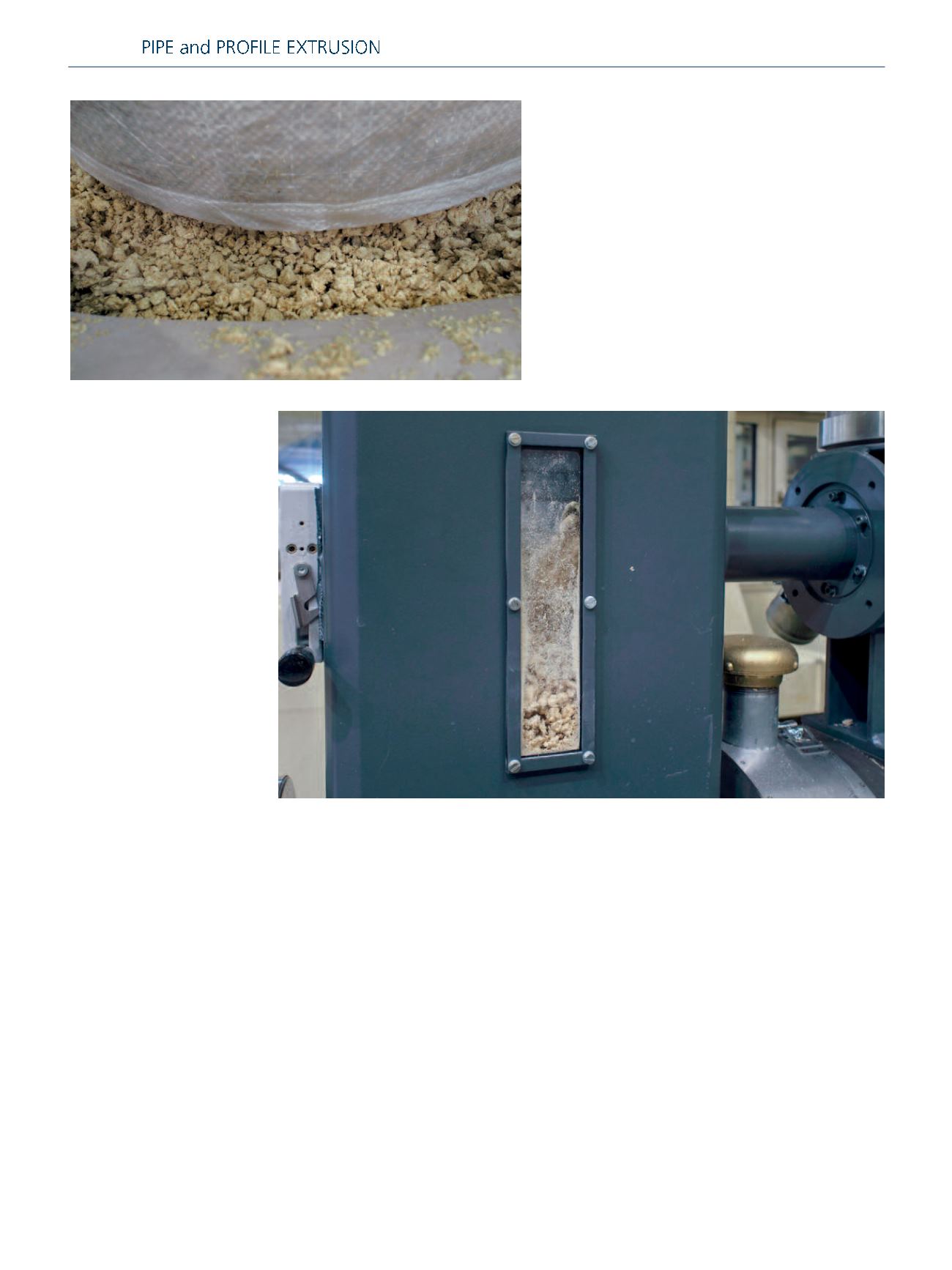
prevents leakage of melt par-
ticles from the processing
chamber and ensures a high
degassing performance with
easy access to the degassing
aperture during operation.
The complete line was de-
monstrated in cooperation
with system partners for too-
ling (Beologic, Belgium), ma-
terial conveyance (EMDE,
Germany) and the gravimetric
dosing system (ConPro, Ger-
many). A 160 x 30 mm H pro-
file was manufactured, which
is used as a connecting ele-
ment in assembling a house
made of WPC profiles. In this
context, the formulation of
the compound used, with a
low bulk density of 270g/l
and consisting of 72% wood
fibers and 28% PP with additives, deserves special attention.
The material was processed as an agglomerate that was pro-
duced in a heating/cooling-mixer system. This solution consti-
tutes a particularly cost-efficient compounding alternative,
especially since the agglomerate was fed into the extruder wit-
hout using a dosing unit, simply by using the material’s hy-
drostatic pressure.
A special advantage of the compound used in this case is its
high wood content, which ensures a pleasant, well-balanced
indoor climate in its final application for building houses in re-
gions of varying climatic conditions. Thanks to their high wood
content and because PP, which is based exclusively on hydro-
carbons, is used, the profiles also fall under the Waste Wood
Ordinance, which means that thermal disposal is permitted. If
the WPC profiles are used to build hospitals, antibacterial ad-
ditives can be blended into the agglomerate to minimize bac-
terial growth.
A house consisting of such WPC profiles can be built for a
The formulation had an extremely low bulk density of
270 g/l and was processed in the form of an agglomerate
The agglomerate was compounded cost-efficiently in a
heating/cooling mixer system; it was subsequently fed
into the extruder without a dosing unit, simply by using
the hydrostatic pressure of the material (shown in the
picture: material feeding unit in operation, half-filled
with WPC agglomerate)
price starting at 200 EUR per square meter and is therefore
very cost-efficient. With the extrusion line demonstrated, units
of about 60 m² can be produced in less than one day. Thanks
to an easy-click system, the assembly of such a house is very
simple and does not require expert personnel. Therefore the
profiles are ideally suited for use in temporary housing or for
hospitals in crisis areas, and so they provide answers to many
geopolitical issues.
“That we have addressed a highly topical issue with our line
demonstration has been confirmed not only by the partici-
pants of the AMI conference, but also by the fact that both cu-
stomers and investors have shown very lively interest after the
conference, and several test runs have been carried out as
well”, Sonja Kahr, WPC Product Manager, comments the po-
sitive response with pleasure.
www.battenfeld-cincinnati.comExtrusion International 3/2016
20