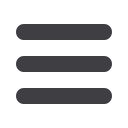
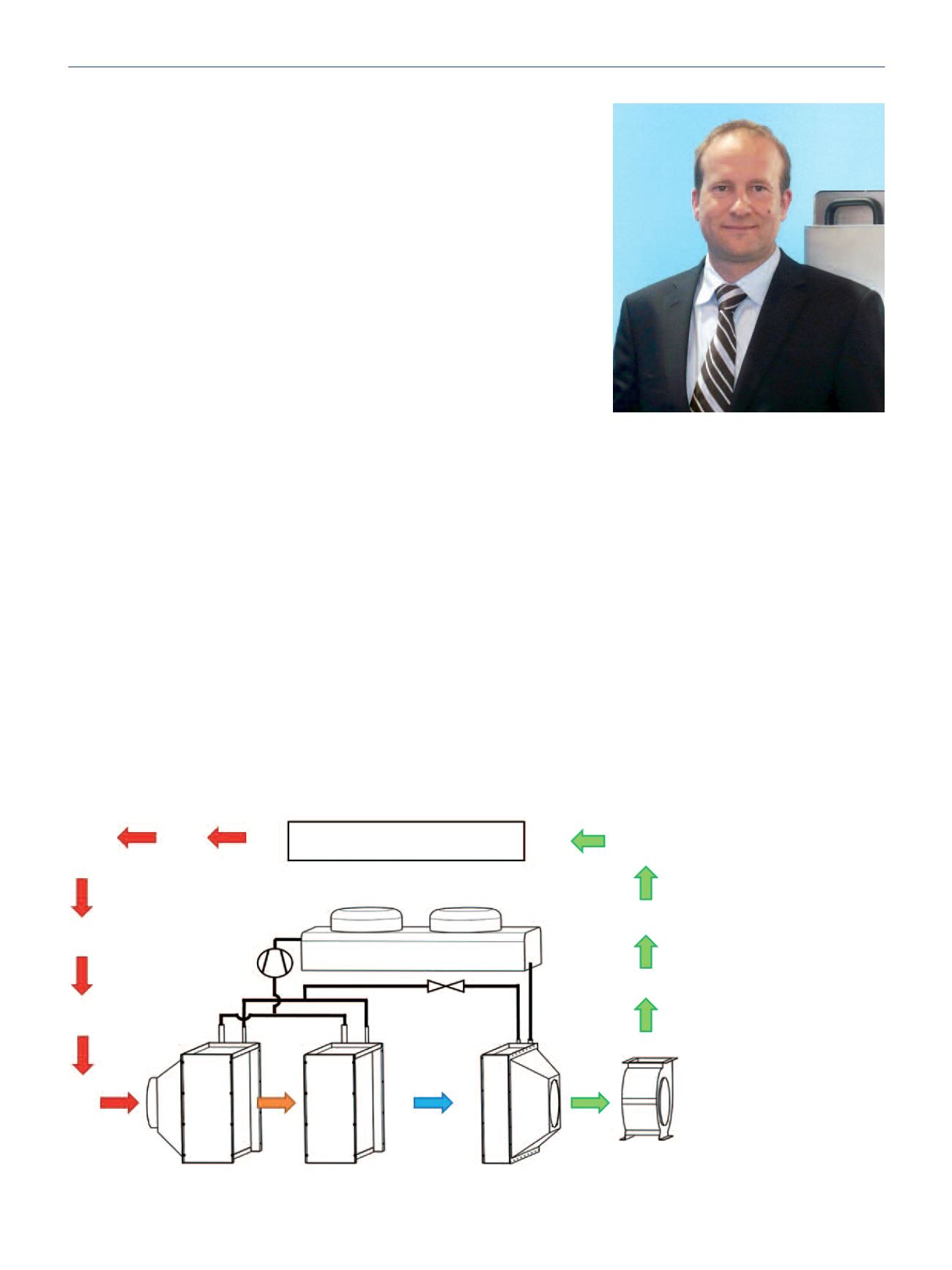
Extrusion International 3/2016
37
By reducing the cooling water temperature of the mould, a
shorter cycle time and subsequently a higher production out-
put can be achieved. If the water temperature sinks below the
dew point of the ambient air, the moisture in the air will con-
densate on the surface of the mould. To avoid this condensa-
tion in facilities located in hot and humid climate zones,
process engineers of manufacturing plants tend to increase
the water temperature above the ambient dew point of the
air. This standard procedure has a crucial disadvantage - the ef-
ficiency confines the effectiveness: increasing the cooling
water temperature extends the cooling time of the item in the
mould, thus reducing productivity and profit (rule of thumb:
1°C increase in cooling water temperature = 2% reduction of
productivity).
In many cases a longer cooling time increases the crystalliza-
tion rates in the moulded plastic resulting in inferior product
quality. Furthermore, condensation on the mould leads to pos-
sible water marks (“orange skin”) on the final product causing
rejects or low product quality.
Limitations of conventional technology
for mould dehumidification
A popular way of drying air for mould dehumidification is with
the adsorption system. This technology, that uses a desiccant
wheel for dehumidification, needs a comparatively high
amount of energy. The energetic inefficiency occurs due to the
use of large regeneration heaters, ventilators, motors and pre
and after cooling with the need for chilled water. Mould de-
humidification with the condensation technology, using a re-
frigerant system, is an alternative to the desiccant system. The
MSP (Mould Sweat Protection) units based on this technology
have been the backbone of Blue Air Systems for years. Many
MSP units have been in-
stalled in facilities world-
wide. Thanks to their
reliability and stability, these
units bring their full per-
formance even after many
years and allow a condensa-
tion-free production with the
optimal cooling temperature
in the mould. A disadvan-
tage of all dehumidifiers,
whether they operate on the
basis of adsorption or con-
densation drying, is that rela-
tively large cooling loads are
needed to pre-cool the am-
bient air.
In many cases, the chilled
water capacity of the facility
is not dimensioned suffi-
ciently to supply the neces-
sary cooling load of chilled
water. When investing in a
new dehumidification sys-
tem, besides the cost of the
Bernhard Stipsits, managing director of Blue Air Systems:
“The DMS units from Blue Air Systems guarantee condensation-free production
conditions in a closed system, even when using very low chilled water temperatures for
the moulds throughout the year, making you independent from ambient climatic
weather conditions. The MPSCS (Micro Processor Controlled Segment Condensation)
technology provides controlled parameters at all times, making sure the optimal
energetic conditions are automatically adjusted. What you get is higher productivity and
constant product quality in the production process at lowest possible energy
consumption. It’s time to start reducing our ecological foot print and the DMS is a huge
step in this direction!”
Functional Principle DMS (Dry Mould System): The process air is run in a closed loop, circulating back to
the DMS unit for pretreatment and dehumidification of the air to a 3°C dew point. The MPSCS (Micro
Processor Controlled Segment Condensation) technology guarantees perfect and consistent conditions
at the lowest possible energy consumption
Production Plant