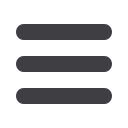
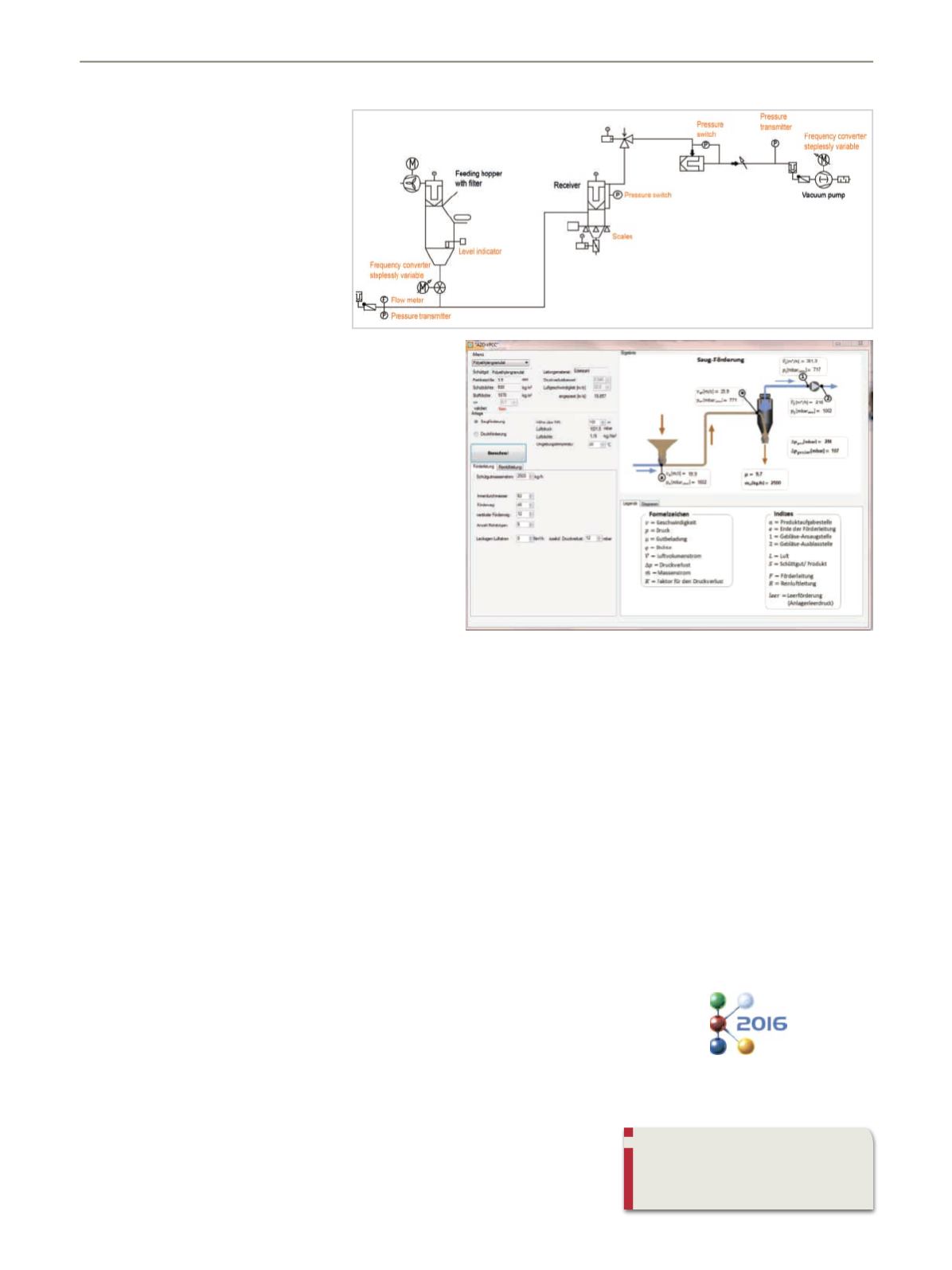
AZO GmbH + Co. KG
Industriegebiet Ost, 74706 Osterburken,
Germany
www.azo.comHalle 9, Stand C42
ches Produkt mit zusätzlicher Sensorik
und Intelligenz ausgestattet werden soll?
Bußbach erläutert: „Wir haben uns ge-
fragt: Wo ist der Mehrwert für unsere
Kunden und uns? Bei welchen Produk-
ten ist er am höchsten? Wollen das unse-
re Kunden überhaupt? Und hat unsere
Entwicklung die Ressourcen, das umzu-
setzen?“ Mindestens eines der 4 P – Pro-
dukte oder Produktion von AZO oder die
seiner Kunden – müsste nachhaltig vom
Plus an Intelligenz profitieren, damit AZO
die Entwicklung im Hinblick auf I4.0
nachhaltig vorantreibt.
Datenhandel innerhalb der
Anlagenkette
Auch das RAMI-4.0-Modell, eine Refe-
renzarchitektur für Industrie 4.0, wurde
dabei intensiv genutzt. Automatisie-
rungsexperte Herzig schildert: „Wir ha-
ben uns gedanklich auf die verschiede-
nen Layer gesetzt und uns gefragt: Wel-
che Frage könnte dieser Layer an unser
Gerät haben.“ So gewann man überra-
schende Erkenntnisse, etwa, dass es
sinnvoll sein könnte, einen Feuchtesen-
sor einzubauen, obwohl an dieser Stelle
des Prozesses die Feuchte keine Rolle
spielt. „Doch wir können sie an dieser
Stelle im Produktstrom auf einfache Art
und Weise bestimmen“, erläutert Herzig,
„und den Wert an ein anderes Equip-
ment ,verkaufen‘, der aus dem Feuchte-
wert eine nutzbringende Information ab-
leiten kann.“
Industrie 4.0-System „Intelligente
Förderung“
Das mag sich nach Zukunftsmusik anhö-
ren. Doch AZO ist mit seiner ersten In-
dustrie 4.0-Komponente schon in der
Realität angekommen: Die selbstopti-
mierende pneumatische Förderung kön-
nte schon bald von den ersten Kunden
genutzt werden. Die Daten, die dazu be-
nötigt werden, sind zum Teil auch bei be-
stehenden Anlagen vorhanden: Sie resul-
tieren aus der Auslegung der Förderanla-
ge. Zudem sind beispielsweise die physi-
kalischen Grunddaten über den gerade
geförderten Rohstoff von Vorteil, um mit
den richtigen Grundeinstellungen zu
starten. Für die intelligente Förderung im
Sinne von I4.0 ist dann noch Zusatzsen-
sorik nötig. Ziel ist, dass sich Luftmenge
und Schleusendrehzahl immer automa-
tisch auf den optimalen Betriebspunkt
einstellen. Das senkt die Betriebskosten
und reduziert Inbetriebnahmezeiten.
Durch Condition Monitoring wird auch
Predictive Maintenance möglich, was die
Verfügbarkeit der Anlage weiter erhöht.
(Bild 5 und 6)
Zusätzliche Intelligenz wird auch in die
Differenzial-Dosierwaage einziehen, ist
Bußbach überzeugt. Der Mehrwert?
Bußbach erläutert: „Wir können bei-
spielsweise aus Veränderungen in der
Schüttdichte, in Verbindung mit anderen
Daten wie etwa Schneckendrehzahl,
Rückschlüsse auf mögliche Systemfehler
ziehen: etwa ein Zuwachsen der Schne-
cke. Auch Parameter wie die Nachfüll-
punkte können so automatisch justiert
werden.“
Wegbereiter in die digitale Zukunft
Noch steht viel Arbeit an, Arbeit für Jah-
re, bis alle AZO-Produkte und -Prozesse
im Hinblick auf integrierte Sensorik,
Kommunikationsfähigkeit und andere
I4.0-Merkmale unter die Lupe genom-
men und gegebenenfalls verbessert wur-
den. Als Performance-Anbieter will man
so selbstverständlich dem Wettbewerb
ein Stück voraus sein. Der größte Nut-
zen, da sind sich Herzig und Bußbach ei-
nig, resultiert jedoch, wenn Anlagenbau-
er und -betreiber eine übergreifende
Perspektive einnehmen und danach fra-
gen, welche Informationen für vor- oder
nachgeschaltete Systeme wichtig sind.
Bußbach hebt hervor: „Alle Hersteller
müssen sich Gedanken machen, welche
Datenschnittstellen sie in Zukunft zur
Verfügung stellen.“ Auch, wenn Indu-
strie 4.0 noch in den Anfängen ist – An-
lagen- und Maschinenbauer wie AZO,
die sich von der Komplexität nicht ab-
schrecken lassen, sondern gut überlegt
systematisch die ersten I4.0-Projekte um-
setzen, werden die Wegbereiter in das
digitale Zeitalter sein.
Bild 5 und 6:
Voraussetz-
ungen für eine
intelligente
Förderung:
Auslegungs-
software und
zusätzliche
Sensorik
Bild 6
30
Materialhandling
Extrusion 7/2016