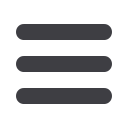
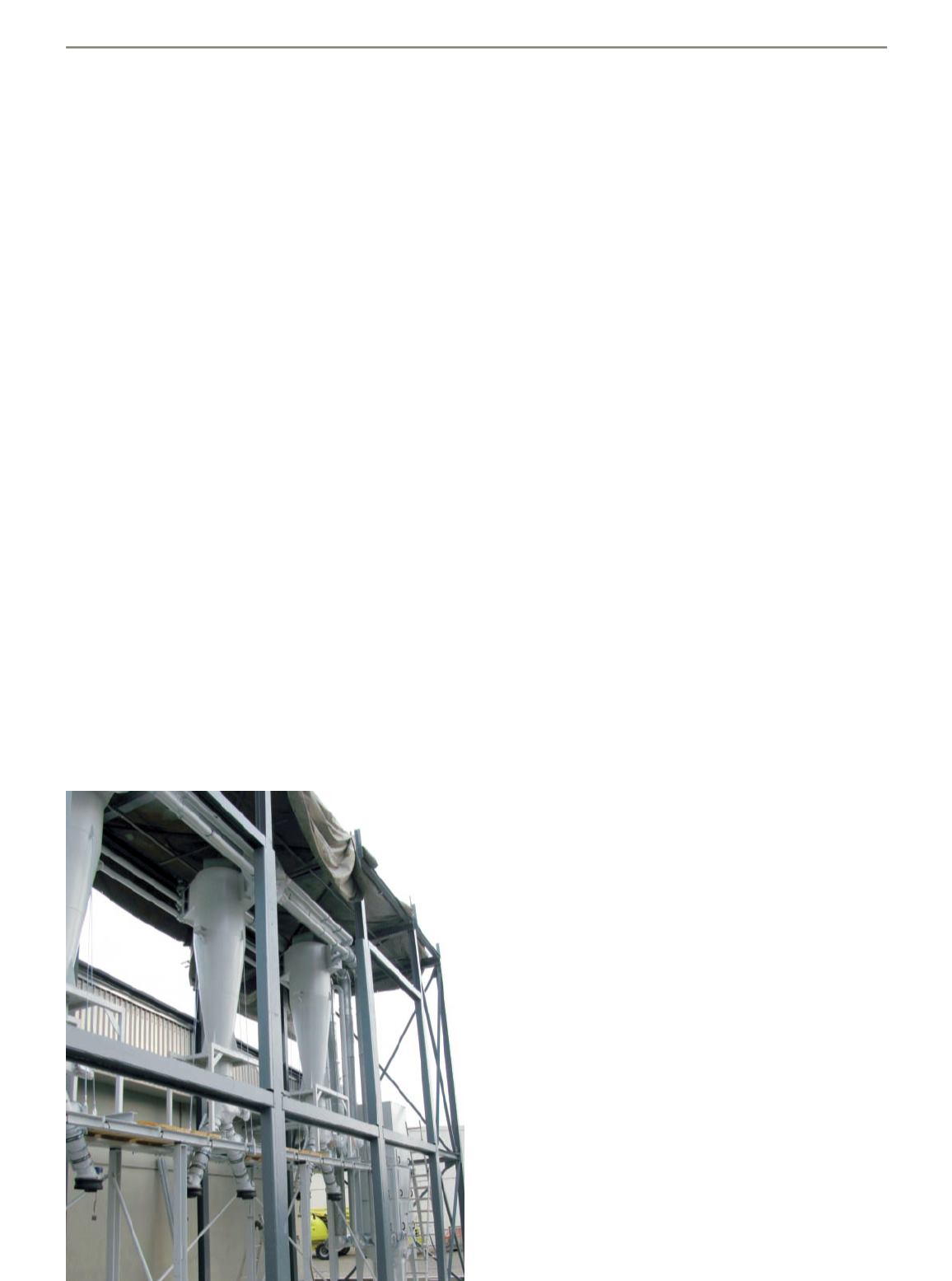
T
hermoforming is one of the most important processes in the
mass production of foodstuff packaging from PP and PET
film. Unavoidable, however, are the large amounts of residual
material which must be reground. The plant manufacturer
Getecha delivers package solutions with a high degree of auto-
mation ranging from granulating the material residues to trans-
porting the granulated material until it is packed in BigBags.
The first process step is the granulation of blanking skeletons or
film fragments. Getecha has four rotary cutter model series
with 17 different base models of infeed granulators available
ensuring that the suitable granulation solution is ready for any
thermoforming application. The Compact series RS 2400 ma-
nages infeed widths from 210 to 900 mm and achieves peak
throughputs of 300 kg/h. By contrast, the RS 3000 and RS
3800 model series with their three-blade rotors (cutting circles
of 300 and 380 mm) master infeed widths from 390 to
1500 mm and throughputs up to 1300 kg/h. The granulators of
the RS 4500 model series are designed for top throughputs up
to 1500 kg/h. Their infeed widths range from 580 to 1480 mm
and their blades rotate at a diameter of 450 mm.
Modular concept simplifies process integration
Because all Getacha granulators feature a modular concept,
each model can be optimally adapted to its application. Already
by selecting the appropriate infeed system, the granulator can
be optimized for very different granulating tasks: For thick
films, lean blanking skeletons with little film portions, blanking
skeletons of round molded parts, for film with unpunched
structures or for very thin PET film residues (< 0.20 mm). If the
infeed width requires greater dynamics (more than 8 mm), an
infeed with belt drive can be employed. Utilizing powerful dual
infeeds, production residues can be fed from two directions
with a single RS granulator!
Thanks to the automatic speed feature from Getecha where a
floating roller control continuously compares the infeed speed
of the granulator with the cycle of the thermoforming line, the
film web remains taught and the otherwise common – often
manually performed – setpoint adjustment with the production
plant is no longer required. This simplifies the process integra-
tion of the infeed granulator and reduces interruptions. Beyond
this, Getecha equips their infeed granulators with a frequency
converter on the main drive or an EnergySave controller which
controls the current peaks, lowers the motor output during
idling and partial loads and minimizes reactive current.
Transporting and bagging
Coordinated with its infeed granulators, Getecha also offers ef-
ficient system solutions for the transport of the granulated ma-
terial. Especially manufacturers of foodstuff packaging utilizing
thermoforming benefit from this fact since the technical clean-
liness in production is a critical factor for them. The infeed gra-
nulator is therefore usually positioned closely after the thermo-
forming line and the granulated material is transported directly
to the extruder or silo or a BigBag station at a remote facility.
Image 3: Getecha realizes extraction systems for the transport
of granulated material both in pressurized and suction opera-
tion
55
Extrusion Asia Edition 1/2016
(厚度大于8mm),可采用带驱动装置的横向喂料带输送物
料。如果采用强有力的双横向进料方式,生产中的边角料可
以从两个方向喂入一台RS粉碎机!
Getecha产品的一大特色是采用了自动速度调节技术连续
控制浮动辊筒,使其与粉碎机的横向进给速度相适应,而横向
进给速度又是与热成型生产线的节拍相吻合的,因此膜材能保
持张力状态,不再需要针对生产线速度对进行设定调节。通常
的设备需要手动调节以适应生产线速度。这就简化了横向喂料
粉碎机联机到生产线的过程,减少了生产的中断时间。除此以
外,Getecha的横向喂料粉碎机的主电机配备了变频器或者节
能控制器以控制电流峰值,在电机空载或部分负载时降低电机
的功率,从而将无功电流降低到了最小值。
输送和装袋
与横向喂料粉碎机相协调,Getecha同时能提供有效的
系统解决方案,输送粉碎的物料。尤其是那些采用热成型工
艺制造食品包装的生产商将由此而获益,对他们而言,生产
中的清洁技术是关键因素。因此,横向喂料粉碎机通常放置
于靠近热成型生产线下游的位置,粉碎物料直接输送到挤出
机或者位于远处的料仓或者大袋装袋设施。粉碎物料的输送
可以通过正压或负压抽吸两种方式来完成,Getecha可提供
这两种方式供客户选择。
如果采用正压方式,粉碎后的物料通过管线被风机叶轮
从粉碎机输送到旋风分离器和大袋装袋站。如果采用负压抽
吸方式,粉碎后的物料被中压风机通过管道系统“拉动”。这种
方式有着若干好处:不需要用到易于磨损的风机叶轮(考虑
到磨损物料这一事实),由于管道中形成真空,因此没有粉
尘逸散到环境中。还有,因为负压抽吸输送的方案中,风机
不是位于粉碎机的内部,而是在装袋设施所在处,这样就节
省了热成型生产线所在处的空间,同时还降低了生产车间的
噪声水平。
对于大袋装袋站,Getecha可提供不同的选择。高度调
图3:Getecha采用正压输送和负压抽吸输送两种方式实现粉碎物
料的输送