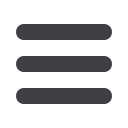
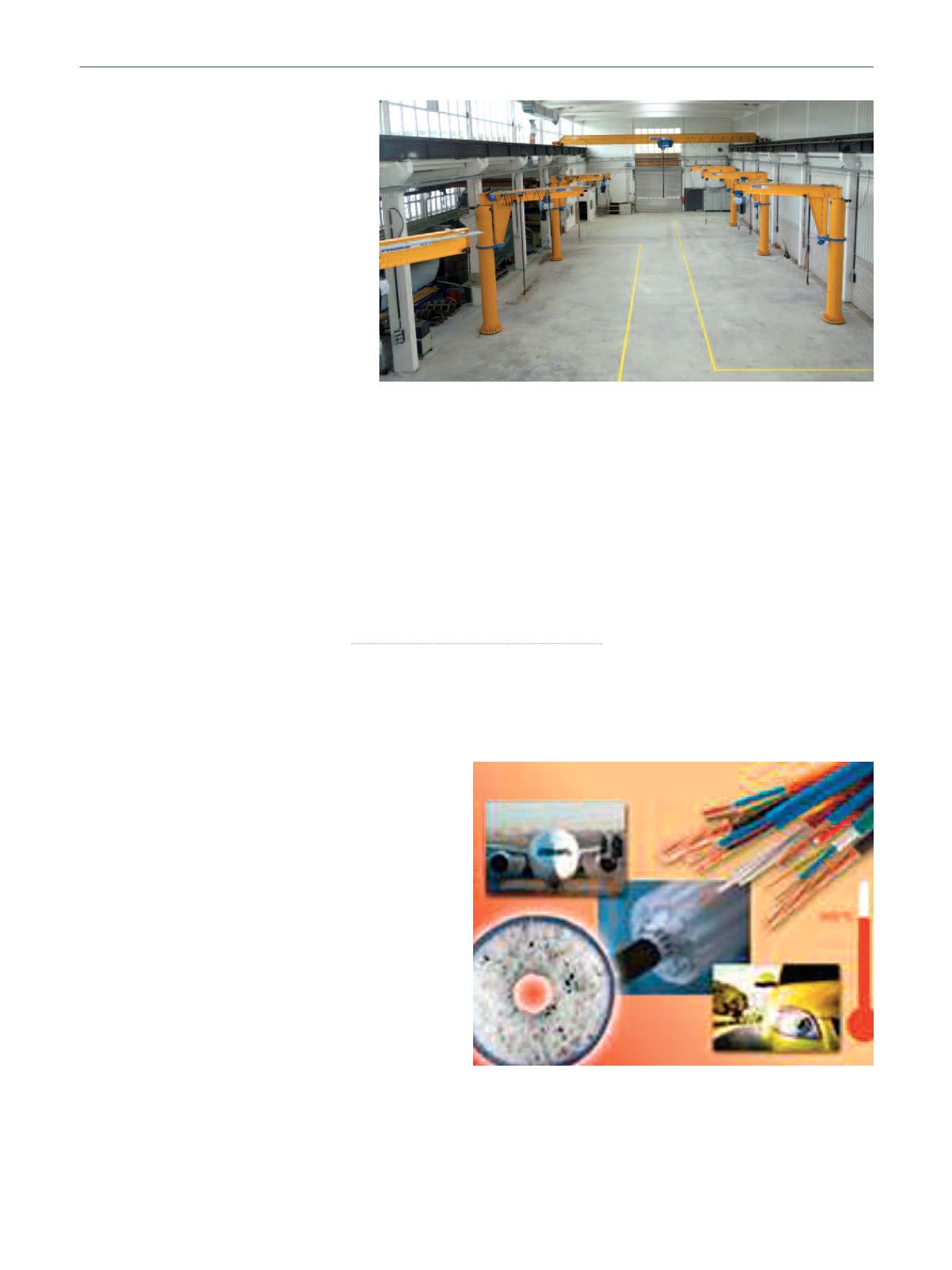
13
Extrusion International 1/2016
After the renovation
Herbold Meckesheim GmbH in Meckes-
heim, manufacturer and supplier of size re-
duction equipment, consisting of 150
employees, launched their completely rebuilt
production hall at the beginning of October.
The 1400 m² crane hall was built in 1962
and only used as a warehouse during the last
decades. The production hall contains 6 co-
lumn-mounted slewing cranes at 12 different
sites. Machine parts weighing up to 3 t can
be mounted simultaneously. The heavier
parts and finished machines are conveyed by
a gantry crane.
This renovation is part of a larger, new con-
struction and rebuilding project. With the investment 5 million
EUR, the production will be modernized and a new technical
lab will be built. The technical lab will be used for demon-
stration and trial purposes of the machines that are part of
Herbold’s product range consisting of machines and plants
for recycling plastics. By size-reducing, washing, separating,
drying and densifying, clean product waste and used, mixed
and contaminated plastics from trade, commerce and yellow
bags are recycled so they can be used again. Each kilogram of
plastics that is recycled by Herbold’s customers saves 2 kilo-
grams of crude oil and between 1.5 and 3.2 kg of greenhouse
gases.
Two-thirds of production is destined for export as is the case
with many machine factories based in Baden-Württemberg.
The machines and plants are mainly exported to Europe,
North and South America, North Africa and Asia.
www.Herbold.comCompletely renovated production hall Herbold Meckesheim
At Wire 2016 The Chemours Company presents its broad portfolio
of Teflon™ resins for the wire & cable industry
The Chemours Company (“Chemo-
urs”) (NYSE: CC), a global chemical
company with leading market positions
in titanium technologies, fluoroproducts
and chemical solutions will be exhibiting
its wide range of fluoroplastics for the
wire and cable industry in hall 17, stand
D66 at Wire 2016. Further additions to
the ECCtreme™ ECA family, a class of
meltprocessable perfluoroplastics which
combines the advantageous mechani-
cal, electrical and chemical properties of
PTFE with high thermal stability. For in-
stance, at a thickness of 0.75 mm, the
material has an RTI (Relative Thermal
Index) listing of 300 °C according to UL
746B. Thanks to its continuous service
temperature of 300 °C, ECCtreme™
ECA thus exceeds the previous upper
limit of 260 °C for conventional perf-
luoroplastic insulating materials.
ECCtreme™ ECA grades can be pro-
cessed on con-
ventional extru-
sion equipment
for hightempe-
rature fluoropla-
stics
using
standard pro-
cessing condi-
t i o n s .
Down s t r e am
heat treatment
(epitaxial co-cry-
stallisation) im-
proves
the
material's ther-
mal resistance
and offers bene-
ficial mechanical
properties, such as long-term tensile
modulus and improved stress cracking
resistance.
The material is suitable for wire and
Key solution topics are highest service
temperatures of up to 300 °C,
miniaturization, superior data
transfer, weight savings as well as
patented PTFE Channel Extrusion
Technology providing improved
electrical properties