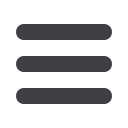
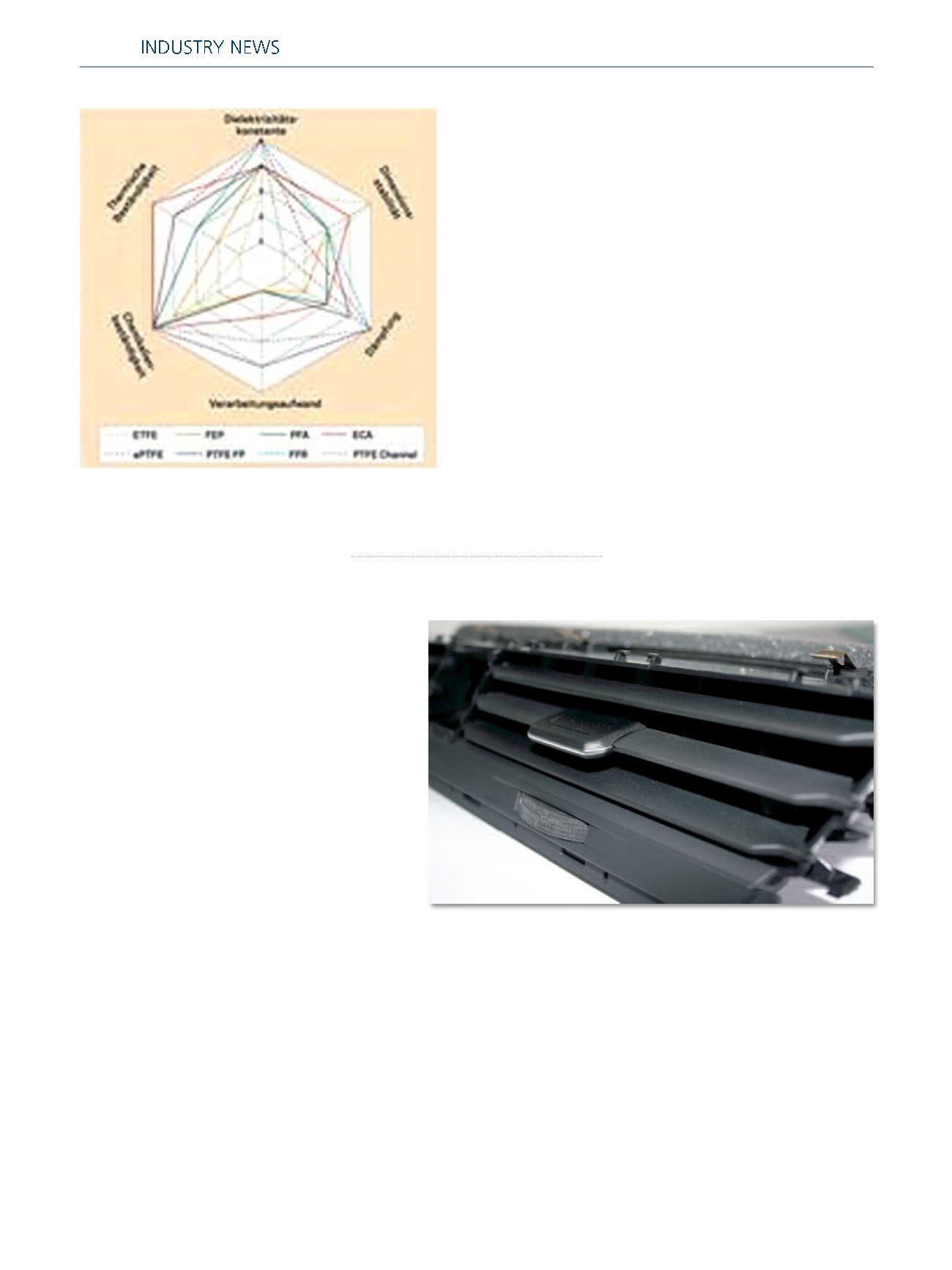
Extrusion International 1/2016
14
www.keyplastics.comcable insulations, which are exposed to extreme service con-
ditions such as very high temperatures, elevated pressures and
corrosive surroundings. Typical fields of application are the oil
and gas industry, aerospace, energy generation, semiconduc-
tor fabrication and the automotive industry. "This develop-
ment is our response to industry's challenge to offer a
high-temperature, melt-processable perfluoroplastic", exp-
lains Frenk Hulsebosch, Global Product Manager Melts Fluo-
roplastics at Chemours Fluoropolymer Solutions. Further
products presented on the stand will include Teflon™ fluo-
roplastic foam resins (FFR) produced using patented Airquick
technology. Cables made with foamed fluoroplastic insulation
have a lower signal return loss than conventional data cables,
so enabling miniaturization and weight savings thanks to
lower density and thinner insulation thicknesses. One current
example is the new KL24 Star-Quad data cable developed for
the aerospace industry by Draka Fileca, Sainte-Geneviève,
France which won a DuPont Plunkett Award in 2013. At iden-
tical diameter, it is up to 25 per cent lighter than previously
used quad cables and enables a reduction in aircraft fuel con-
sumption, so reducing environmental impact.
Wire & cable property performance of various
fluoroplastics and technologies
www.chemours.comNew Air Vent
Key Plastics Löhne supplies complete assemblies to
the automotive industry. For the VW Touran, the com-
pany developed a new air vent with longer slats than
in any other vehicle type. The Hamburg-based plastics
distributor K.D. Feddersen provided support in the pro-
duct selection. The material for the new slats had to
have a good surface finish yet still possess a high de-
gree of stiffness, while also offering good value for
money. For all other models, Key Plastics already used
a 50% glass fibre reinforced PA 6 compound with re-
duced moisture absorption from AKRO-PLASTIC. In this
case, however, the stiffness was inadequate. Christoph
Gerling, Business Development Manager at K.D. Fed-
dersen consequently recommended increasing the level
of reinforcement to 60 %, and the very first test using
AKROMID
®
B3 GF 60 4 RM-M satisfied the customer's
requirements.
AKROMID
®
RM-M (mechanical types) is suitable as a
design material for components subject to high mechanical
stress. This product range offers only reinforced compounds with
varying glass fibre content in three designs: standard, surface-
modified ("9") and with increased chemical resistance ("4"). The
material is a blend of polyamide and PBT, combining the favou-
rable properties of both polymers: the high degree of stiffness
and low water absorption of PBT and the large processing
window and excellent surface finish of the polyamide. Precisely
these properties were of key importance for the implementation
of the new design with significantly longer slats. The reduced
moisture absorption (1 %) is on par with partially aromatic
blends and thus enables a design with low tolerances. A further
advantage of the material is that the tensile modulus is only
slightly reduced and the slat therefore exhibits a consistently high
degree of stiffness under a wide range of climatic conditions,
thereby enhancing the value of the design.
Low moisture absorption results in good dimensional stability,
thereby ensuring consistent operating forces during adjustment
of the longer slats