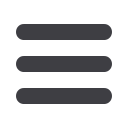
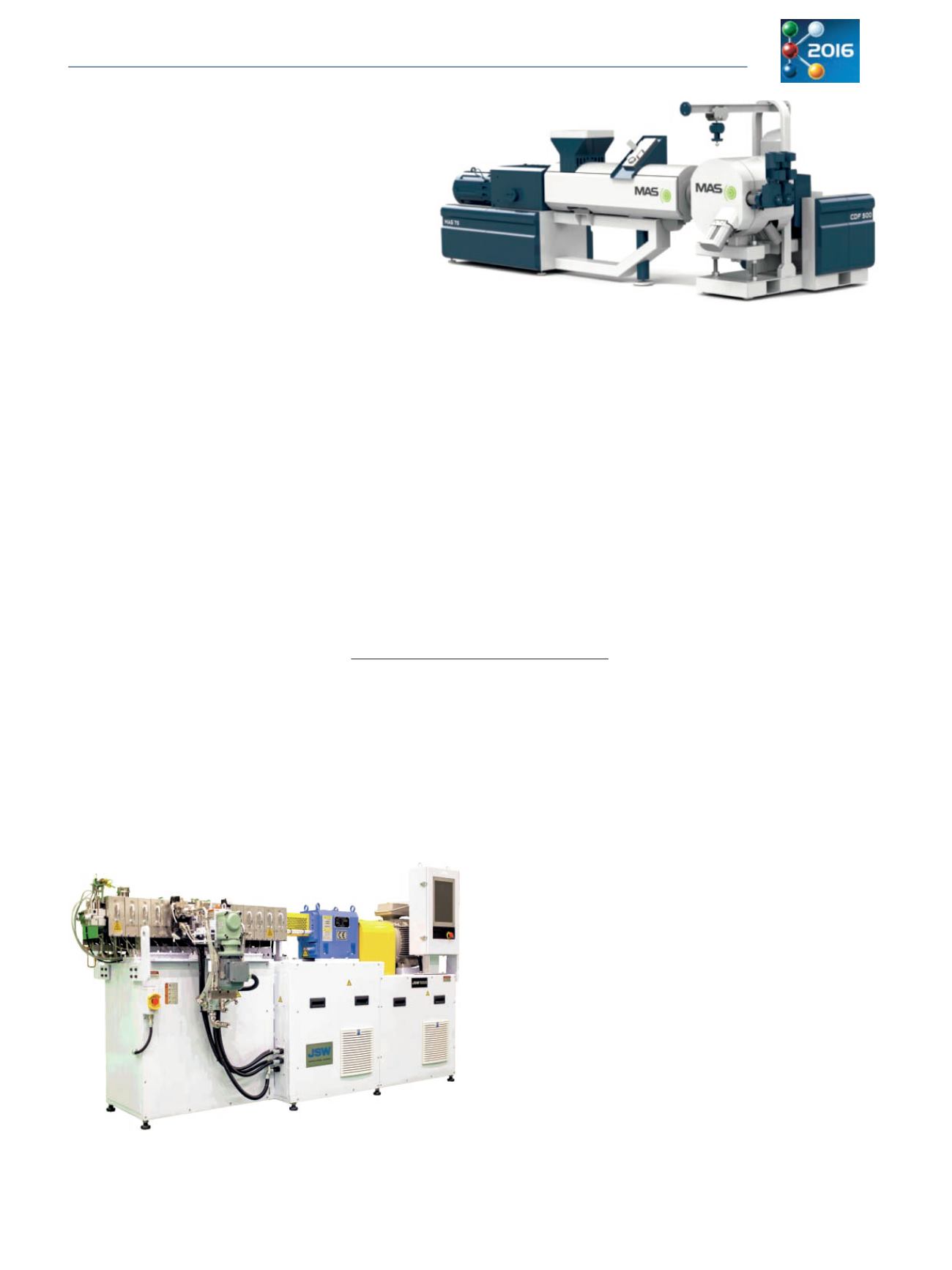
sizes use a 510 mm filter disc. Specifically, the CDF 500
with one disc offers a filtration area of 1,640 cm² for
700 to 1,600 kg/h. The next-larger filter type, CDF-500-
D with two parallel discs, offers twice the filter surface
at 3,280 cm² and permits a throughput of 1,300 to
2,000 kg/h. The largest filter unit with the type desi-
gnation CDF-500-D-P consists of two parallel CDF-500-
D units with a total of 4 filter discs and a filter surface
of 6,560 cm² with a possible melt throughput of up to
4,000 kg of polyolefins per hour, which makes it cur-
rently one of the highest-performing units of its size on
the market.
The basic concept of the filter is a circular carrier plate rotating
in a melt-conducting housing with an exchangeable filtration
disc. The filter disc is made of surface-hardened steel and avai-
lable in filtration fineness ranging from 90 to 750 µm. The fil-
tration disc in the housing continuously transports the
contamination towards the scrapers, which lift the contami-
nation from the screen surface and feeds it to a discharge
screw.
One of the latest developments for the CDF filter is the pneu-
matically actuated scraper system. This latest feature allows
dynamic control of the actual pressure exerted on the scrapers
clearing the contamination from the filter surface. This unique
development allows quick changes in setup for different melt
pressures and levels of contamination offering wider process
windows adjustable ‘on the fly’. In cases of more heavily or
varyingly contaminated melts, an adjustable fluctuating scra-
per pressure can be implemented in order to remove the ad-
ditional impurities and keep a stable process without causing
excessive wear on the filter disc.
Further features of the latest filter generation include optimi-
sed melt channels inside the housing to minimise melt pressure
as well as a new heating layout with heating plates and hea-
ting bands instead of heating cartridges to improve the hea-
ting coefficient. (Fig. 2).
Fig. 2: At its 10th anniversary, MAS presents itself with
a new corporate design and a new machine design
for the extruder and melt filter series
Hall 9, Booth D42
➠ www.mas-austria.comThe Japan Steel Works:
TEX25
α
III
high-performance twin-screw extruder
T
he Japan Steel Works, Ltd. JSW, shows its TEX25
α
III labo-
ratory extruder with a special side feeder, the compoun-
ding range of which extends to super engineering plastics and
rubber/elastomer compound. The compact 26.5 mm diame-
ter co-rotating twin-screw extruder (first worldwide debut in
2014), for product development of various compounds and
masterbatches in engineering and high performance thermo-
plastics is the smallest one of eight types in the TEX-
α
III series
(up to 129.5 mm diameter) available in Europe.
The TEX25
α
III compounding range covers all general pur-
pose/engineering plastics recipes and extends to super engi-
neering plastics such as PEEK, PPA, PPS, LCP, PEI, and PI, also
rubber/elastomer compound such as TPV. This makes the
compounder ideal for research and development with fre-
quent material and process changes, as cartridge heaters and
a barrel clamping mechanism enable easy and rapid barrel sec-
tion block changes., The total screw length/diameter (L/D) ra-
tios can be selected from 42 with 12 blocks, 52.5 with 15
blocks, and 70 with 20 blocks. The machine accommodates
TEX25
α
III, co-rotating twin-screw extruder
Extrusion International 5/2016
61