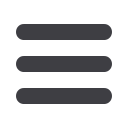
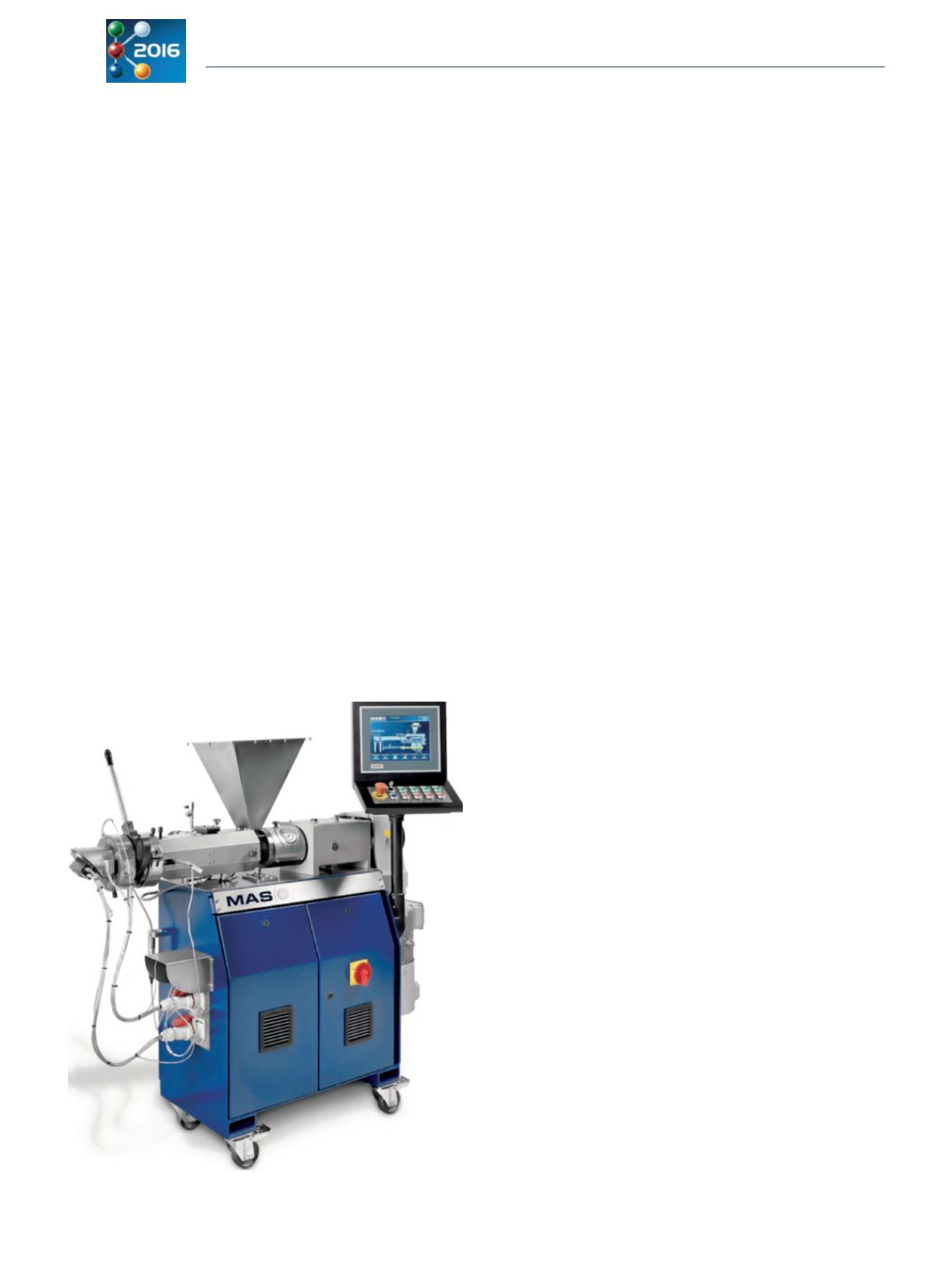
MAS:
new generation of extruder
and melt filter series
T
he Upper Austrian manufacturer of extrusion solutions
"MAS Maschinen- und Anlagenbau Schulz GmbH" will
present themselves 10 years after the company was founded
with an entirely new design at the K-2016. Now, an establis-
hed supplier of unconventional but proven technology suc-
cessful in many applications. The conical co-rotating
twin-screw extruder holds the central position in the portfolio
of MAS. Its gentle plasticization behaviour paired with very
large feeding opening makes it perfect for all extrusion appli-
cations that require the highest degree of thermal and me-
chanical polymer protection. This is especially the case for
recycling and compounding applications as well as for film ex-
trusion. 110 delivered units in ten years document that the
young company's development is on the right track and sets
a clear path for the future. The water-less DRD (Double-Rotor-
Disc) cleaning and drying system for film flakes and regrind
material, which has been offered since 2006, is as innovative
as it is new. More than 50 of these machines have been taken
into operation so far. The third pillar is the continuous melt fil-
ter, which was introduced in 2011. The construction principle
allows customers to individually adjust the filtration system ac-
cording to the contamination that has to be removed, in order
to ensure an effective as well as efficient filtration process.
MAS 24: conical, co-rotating twin-screw extruder in lab scale
The MAS 24 lab extruder has been developed specifically for
plastics manufacturers and compounders to develop recipes
in a practically oriented manner and produce them in very
small volumes. The highly compact build with a screw length
of just 400 mm and conical screws with a diameter of 48 mm
narrowing down to 24 mm are equipped with exchangeable
mixing elements, just like the larger types. The very large fee-
ding opening makes it possible to process in particular re-
grind, flaky and finely cut film material very well. Another
essential benefit is that the MAS system allows full control over
the shear strength and thus the melt temperature of the ma-
terial by varying the screw speed at unchanged feed rate (ad-
justable up to 300 rpm). Accordingly, the possible output is in
the range of 10 to 35 kg/h of the laboratory extruder. The
MAS 24 lab extruder will be presented in operation at the
trade fair stand in combination with an underwater pelletizing
unit.
MAS 75 – the new MAS extruder generation
The third generation of the conical co-rotating twin-screw ex-
truders is available in six different sizes, with output ranges
from 10 kg/h to more than 2,000 kg/h. The outer characteri-
sing feature of the new extruder generation is its new, ergo-
nomically optimised machine design. The most important
advanced technical development is the segmented cylinder
construction that is made up of several partial sections. It per-
mits the exchange of individual cylinders sections subject to
particular stress from abrasion instead of having to replace the
entire cylinder, or selective application of individual cylinder
sections with a special wear protection. The new series is pre-
sented by the example of an MAS 75, which is suitable for an
output of up to 1,100 kg/h (Fig. 2).
It should be noted that MAS has held the FDA "No Objection
Letter" for food grade recycling of PET since mid-2015, and
further meets all EFSA criteria.
CDF – continuous melt filter – the latest generation
The CDF (Continuous Disc Filter) melt filter series developed
by MAS is one of the leading continuous filter systems for re-
cycling applications globally available. The system has reached
this status in part thanks to its concept that permits previously
unachieved filter surface sizes. The smallest size CDF 300
works with a 300 mm disc at 792 cm² filter surface and is suit-
able for a melt throughput from 300 to 700 kg/h. All other
Fig. 1: The lab version of the conical co-rotating twin-screw
extruder type MAS 24 is characterised by a plasticising
unit that is just 400 mm long
Extrusion International 5/2016
60