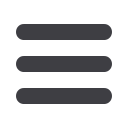
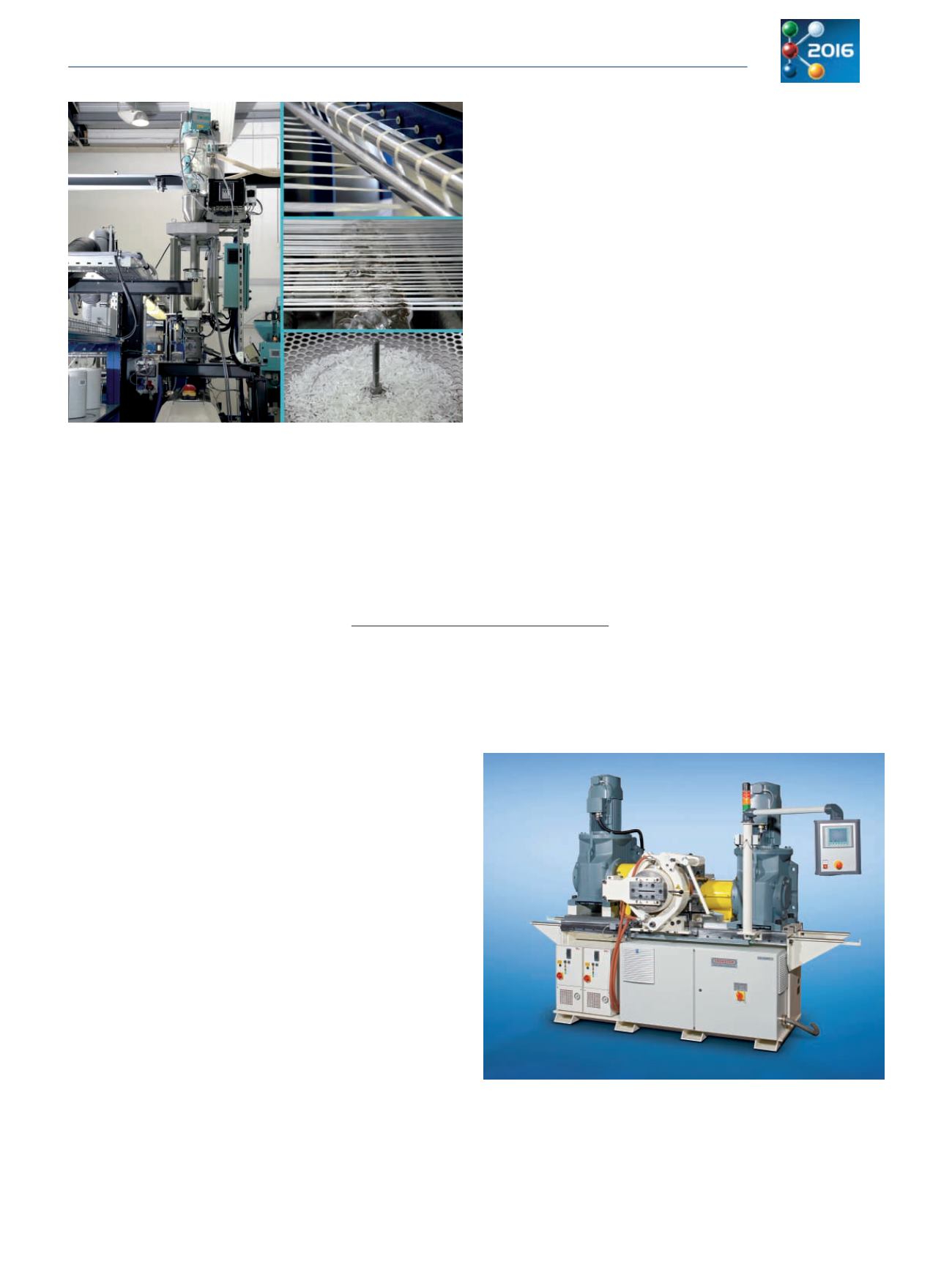
Flexible, versatile LFT technology
ProTec's LFT technology is suitable for producing a wide range
of materials with variable fibre reinforcement along the length
of the pellets and many different polymer matrices. Even the
difficult pairing of carbon fibres with PP can be reliably pro-
cessed. A high-performance compounding extruder is the key-
stone of the line, permitting highly flexible production of a
broad range of individual polymer matrix formulations directly
in the process. Recycled material and additional fillers may li-
kewise be included in the material formulation.
ProTec is capable of designing and supplying turn-key LFT lines
tailored to specific requirements from materials development
to testing and commissioning on the customer's premises.
These lines are capable of handling fibre contents of up to
65 wt.% and throughputs of up to 1,000 kg/h. Any conven-
tional thermoplastics or even biopolymers such as PLA (poly-
lactic acid) can be used as the matrix, while glass, steel, aramid
or carbon fibres can be used as the reinforcing fibres.
ProTec's LFT pultrusion technology is suitable for producing high
quality long-fibre-reinforced pellets with many different polymer
matrices and variable fibre reinforcement.
Photos: ProTec Polymer Processing
Hall 9, Booth D60
➠ www.sp-protec.comTROESTER:
ROTOMEX technology
T
ROESTER GmbH & Co. KG has extended the ROTOMEX
technology, also known as ZX series, for straining of rubber
compounds.
The new developed ZX 150/120 and ZX 170/130 also meet to
the demand for more output and reach up to 4,800 lbs/h de-
pending on construction size. The ZX series, which belongs to
the group of gear extruders, reaches henceforth an output of
up to 590-4,800 lbs/h with corresponding rubber density and
viscosity. The compact construction with proven feed gear
shaft technology and the usual simple handling enable the use
in mixing room and extrusion line.
To take into account rubber compound properties of tires and
technical rubber goods, the drive shafts as well as housing and
head are designed to be tempered separately. At a processing
pressure of up to 35 MPa and a continuous monitoring of all
relevant process parameters it is ensured that the now availa-
ble ZX 150/120 and ZX 170/130 meet the requirements and
there is nothing to prevent from a reliable operation.
Gear Extruder ROTOMEX Type ZX
Hall 16, Booth F40
➠ www.troester.deExtrusion International 5/2016
55