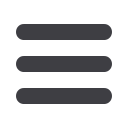
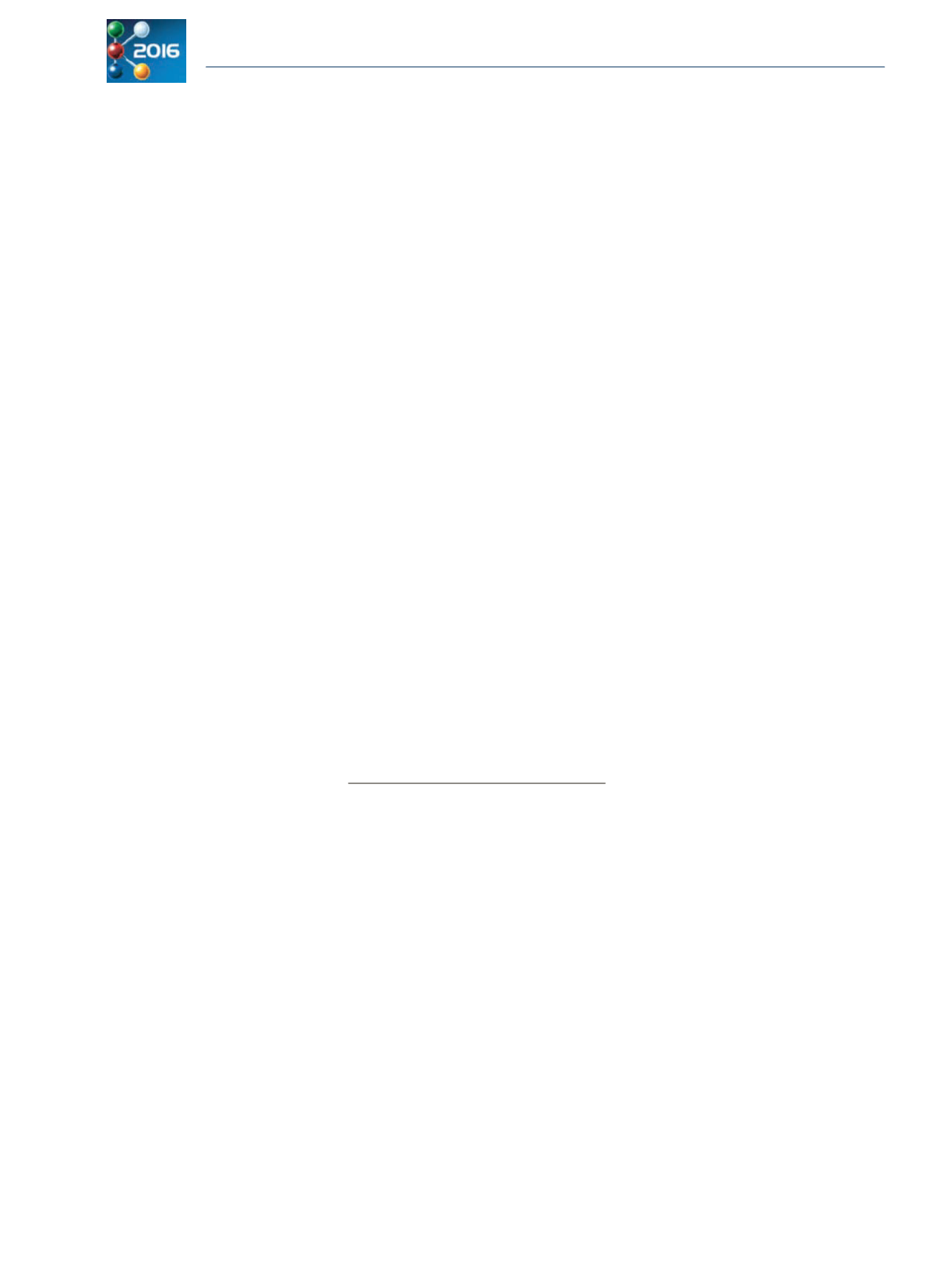
speed control system. Its 15-inch colour LCD touchscreen pro-
vides for easy operation, optimum process control and moni-
toring, storing thousands of operation conditions and process
parameters. It integrates with auxiliary equipment, from JSW’s
gravimetric feeders, side feeder, through to strand and un-
derwater pelletizer units.
The NIC special kneading barrel developed by JSW is discussed
as a possible option. It achieves good mixing/dispersion at re-
peated high-low shear rate and high viscosity for good com-
pound material properties – without dead zones at the mixing
zone through the introduction of several longitudinal grooves
of particular geometry on the inside barrel surface for more
screw to barrel clearance.
New “TEXenter”:
“We would also like to announce that we
will open our new technical center called “TEXenter” at
K2016 in Düsseldorf from January 2017,” says Hayato Hobo,
Sales Representative at JSW Europe since June 2016. The “TE-
Xenter” will be equipped with all high-end equipment for R&D
on extrusion processes, compounding, dewatering, devolatili-
zing, pelletizing etc.
The TEX44
α
III will be installed for high-end compound test
and a specialized TEX30
α
will be available for devolatilizing
test. The 700 square meter floor space “TEXenter” is combi-
ned with a 200 square meter office section. “We welcome
customers and prospects to come to us for TEX-
α
III demon-
strations,” promises Kenji Inagawa, Process Engineer. Apart
from hands on equipment, the “TEXenter” has the appro-
priate facilities for seminars, lectures and training on customer
demand.
vented or closed barrel sections and side feeding of abrasive
reinforcements, heat- or shear-sensitive compound additives
and materials into the melt via a downstream barrel section.
Wear resistant LSP-2 modified tool steel screws and barrels in
N60-S nickel based alloy made by JSW promise long life of bar-
rel and screw (high wear and corrosion resistance) for various
kinds of compounds containing abrasive and/or corrosive ma-
terials and additives.
TEX25
α
III series advantages include a new gearbox design
combined with enhanced gears and bearings, screw shafts and
barrels as well as individual barrel temperature control. The re-
sult is a surprisingly high torque of up to 194 Nm per shaft (or
387 Nm in total) combined with wider processing windows as
well as more aggressive kneading and mixing. Its torque den-
sity value is 18.2 Td i.e. reduced screw speed without redu-
cing the throughput and keeping the temperature at an
optimally reduced level. A standard torque limiting function
disengages motor and gearbox to stop the screw rotation and
protect the machinery. A low noise water-cooled motor is op-
tional, as is direct drive instead of the standard V-belt drive in
Europe.
A TKD Twist Kneading Disc screw element with a twisted tip
developed for energy-efficiency of kneading and mixing sup-
ports this “tip-clearance technology” by ensuring fast material
conveying and relatively low material temperature while retai-
ning appropriate mixing efficiency. “Such features make the
TEX25
α
III the worldwide highest performance compact twin-
screw extruder,” says Jun Kakizaki, JSW Europe General Ma-
nager since July 2016.
JSW’s patented TEX-FAN Flow Analysis Network R&D support
tool developed for TEX25
α
III analyses polymer melt pressure,
temperature, residence time and fill factor with special dedi-
cated software developed by JSW.
The TEX25
α
III comes with JSW’s EXANET 64-bit RISC high-
Hall 13, Booth B45
➠ www.jsw.co.jp/enGetecha:
increased efficiency without dancer
A
t this year's K in Düsseldorf, the plant engineering com-
pany Getecha will show numerous innovative solutions
for central and decentral granulation technology in plastics
processing. This year, the focus of the trade show in hall 9 is
above all the latest generation of the large hopper granula-
tors of series RS 45000 as well as a new control for the infeed
granulator RS 3004-E. Also part of this are the dustproof clean
room granulator GRS 180 and the compact beside-the-press
granulator RS 1615. The company from Aschaffenburg in Ger-
many will present the economically priced sprue picker GET-
pick 700, representing its automation portfolio. How to
skilfully combine high efficiency in granulation technology
with ergonomics at the industrial workplace will be demon-
strated by the plant engineering company Getecha at this ye-
ar's K in Düsseldorf with the example of its granulator series
RS 45000. As representative of this new generation of state-
of-the-art hopper granulators for hourly throughput rates bet-
ween 700 and 1200 kg, an RS 45090 will be presented at the
company's booth A21 in hall 9 with a new granulator hou-
sing. The special feature here is the highly effective integrated
sound insulation, which lowers the operating noise of the cen-
tral granulator to a minimum. Despite these ergonomic mea-
sures, the RS 45090 is very compact due to its drive integrated
at the top in the housing, with a relatively small footprint.
A single granulator for three tasks
Furthermore, Getecha will demonstrate at the K how the effi-
ciency and flexibility of this hopper granulator can be signifi-
cantly increased in practice: With an additional bypass hopper
attached on the side for feeding tubing and profiles from ex-
Extrusion International 5/2016
62