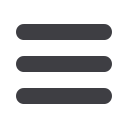
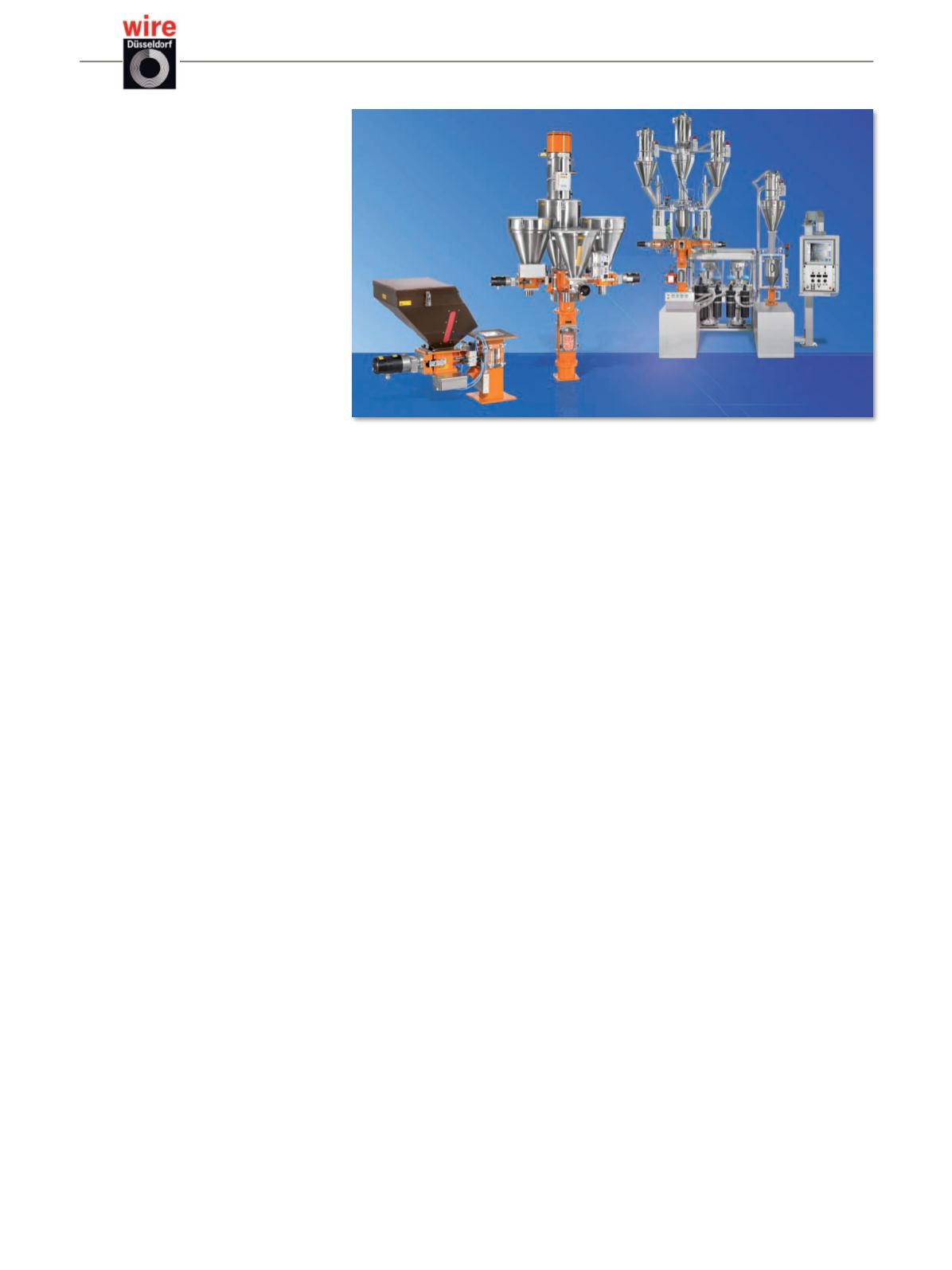
48
Preview
Extrusion 2/2016
Woywod Kunststoffmaschinen GmbH &
Co. Vertriebs-KG
www.plasticolor.deexakte Dosierung über den kompletten
Drehzahlbereich des Extruder ankommt,
sehr kleine Additivleistungen benötigt
werden, teure oder nicht sichtbare Addi-
tive verarbeitet werden, haben Mischan-
lagen grundsätzliche Vorteile.
Für die Lösung dieser komplexen Dosier-
aufgaben stehen, je nach Notwendigkeit,
unterschiedliche Systeme zur Verfügung.
Die Auswahl des Dosiersystems ist im Ein-
zelfall zu prüfen, um für die spezifische
Aufgabenstellung eine bedarfsgerechte
und damit prozess- und kostenoptimierte
Lösung zu verwirklichen.
Heute werden in der
Kabelextrusion
für
komplexere Aufgaben Mischanlagen ein-
gesetzt. Bei diesem Anlagentyp werden
alle Materialien dosiert und damit kontrol-
liert. Mischanlagen arbeiten völlig unab-
hängig vom Extruder bzw. der Extruder-
Drehzahl. Seit Ende 1970 hat die Firma
Woywod diese Entwicklung kontinuierlich
begleitet und aktiv mitgestaltet. So wur-
den und werden stets qualitativ hochwer-
tige, optimal konstruierte und verlässliche
PLASTICOLOR-Dosiergeräte und -Misch-
anlagen angeboten. Woywod bietet zwei
Haupttypen von Mischanlagen an:
• PLASTICOLOR Volumetrische
Mischanlagen
• PLASTICOLOR Gravimetrische
„Loss-in-Weight“ Mischanlagen
Für besondere Aufgabenstellungen und
bei der Extrusion von speziellen Materia-
lien stehen auch synchronisierte PLASTI-
COLOR Mischanlagen zur Verfügung, bei
denen der Materialpegel im Halsstück und
damit die Materialvorlage nicht schwankt.
Dosierung für die Extrusion von
vernetzten und geschäumten
Produkten:
Noch heute werden in Kabelwerken Mate-
rialmischungen von Hand hergestellt. Die
Gefahr von Fehlmischungen und Entmi-
schungen ist hier sehr hoch. Die Reprodu-
zierbarkeit kann nicht sichergestellt wer-
den. Die erste wirkliche Automatisierung
im Bereich Dosierung in der Kabelindustrie
erfolgte durch Scheiben-Dosiergeräte, die
auf dem Maschinentrichter montiert wur-
den. Hier wurde der menschliche Einfluss
minimiert. Die Nachteile lagen im hohen
Wartungsaufwand, der Gefahr der Entmi-
schung bei unterschiedlichen Schüttdich-
ten sowie Materialeigenschaften (es wird
Rührwerk verwendet) und dem damit ver-
bundenem Zwang überzudosieren, dem
schlechten „Handling“ und der Ver-
schmutzung im Umfeld der Anlage.
Mit Einführung der Schneckendosierge-
räte wurden diese Systeme nach und
nach ersetzt. Die Schneckendosiergeräte
werden zwischen den Maschinentrichter
und dem Einzug des Extruders montiert.
Eine Entmischung wird vermieden. Die
Umstellzeiten konnten drastisch gesenkt
werden. Handling und die Sauberkeit im
Arbeitsumfeld wurden verbessert.
Auch heute noch hat diese Lösung ihre
Berechtigung. In einfachen Produktions-
verfahren, bei denen die Drehzahl des
Extruders nicht oder nur sehr wenig ver-
stellt wird (Rampen) und bei denen der
Anspruch an die Mischungsqualität nicht
zu hoch ist, ist die Fahrweise mit syn-
chronisiertem Einzeldosiergerät ein ge-
bräuchliches System. Die Drehzahl des
Dosiergerätes folgt der Drehzahl des Ex-
truders und Leistungen werden nicht
synchronisiert.
Die Ansprüche an die Produkteigenschaf-
ten sind in den letzten 30 Jahren aber im-
mer mehr gestiegen. Neue Produkte be-
dürfen hoch genauer Dosierlösungen. Als
Beispiel sind vernetzte und geschäumte
(chemisches Schäumen) Produkte zu
nennen, bei denen es auf einen gleich-
mäßigen Vernetzungsgrat über die kom-
plette Produktionslänge ankommt resp.
auf eine einheitliche Zellstruktur und
gleichbleibenden Schäumungsgrat. Auch
bei allen Produktionen, bei denen es auf
Bild Woywod
Woywod
wire 2016: Halle 9 / A42
Chemours
wire 2016: Hall 17 / D66
Teflon
TM
Fluorkunststoffe für die
Draht- und Kabelindustrie:
Chemours präsentiert ihr breites Portfo-
lio an Fluorkunststoffen für die Draht-
und Kabelindustrie. Dazu gehören neue
Typen aus der ECCtreme™ ECA Familie,
eine Klasse thermoplastisch verarbeitba-
rer Perfluorkunststoffe. Diese vereinen
die vorteilhaften mechanischen, elektri-
schen und chemischen Eigenschaften
von PTFE mit hoher Temperaturbestän-
digkeit. So besitzt der Werkstoff nach UL
746B die RTI-Einstufung (RTI = Relativer
Temperaturindex) bei 300 °C bei einer
Dicke von 0,75 mm. Mit seiner Dauerge-
brauchstemperatur von 300 °C übertrifft
ECC-treme™ ECA damit die bisherige
Obergrenze von 260 °C für herkömmli-
che Perfluorkunststoff-Isoliermaterialien.
ECCtreme™ ECA Typen können auf her-
kömmlichen Extrusionsanlagen für Hoch-
temperatur-Fluorkunststoffe mit Stan-
dardparametern verarbeitet werden.
Nachgeschaltete Wärmebehandlung (epi-
taxiale Ko-Kristallisation, ECC) verbessert
die thermische Beständigkeit des Werk-
stoffs und ermöglicht vorteilhafte mecha-
nische Eigenschaften wie Langzeit-Zug-
modul und hohe Spannungsrissbestän-
digkeit.
Das Material eignet sich zur Ummante-
lung von Kabeln und Leitungen, die unter
extremen Bedingungen wie sehr hohen
Temperaturen, hohen Drücken und korro-
siven Umgebungen zum Einsatz kom-
men. Typische Anwendungsbereiche sind
die Öl- und Gasindustrie, Luft- und Raum-