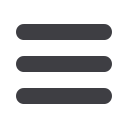
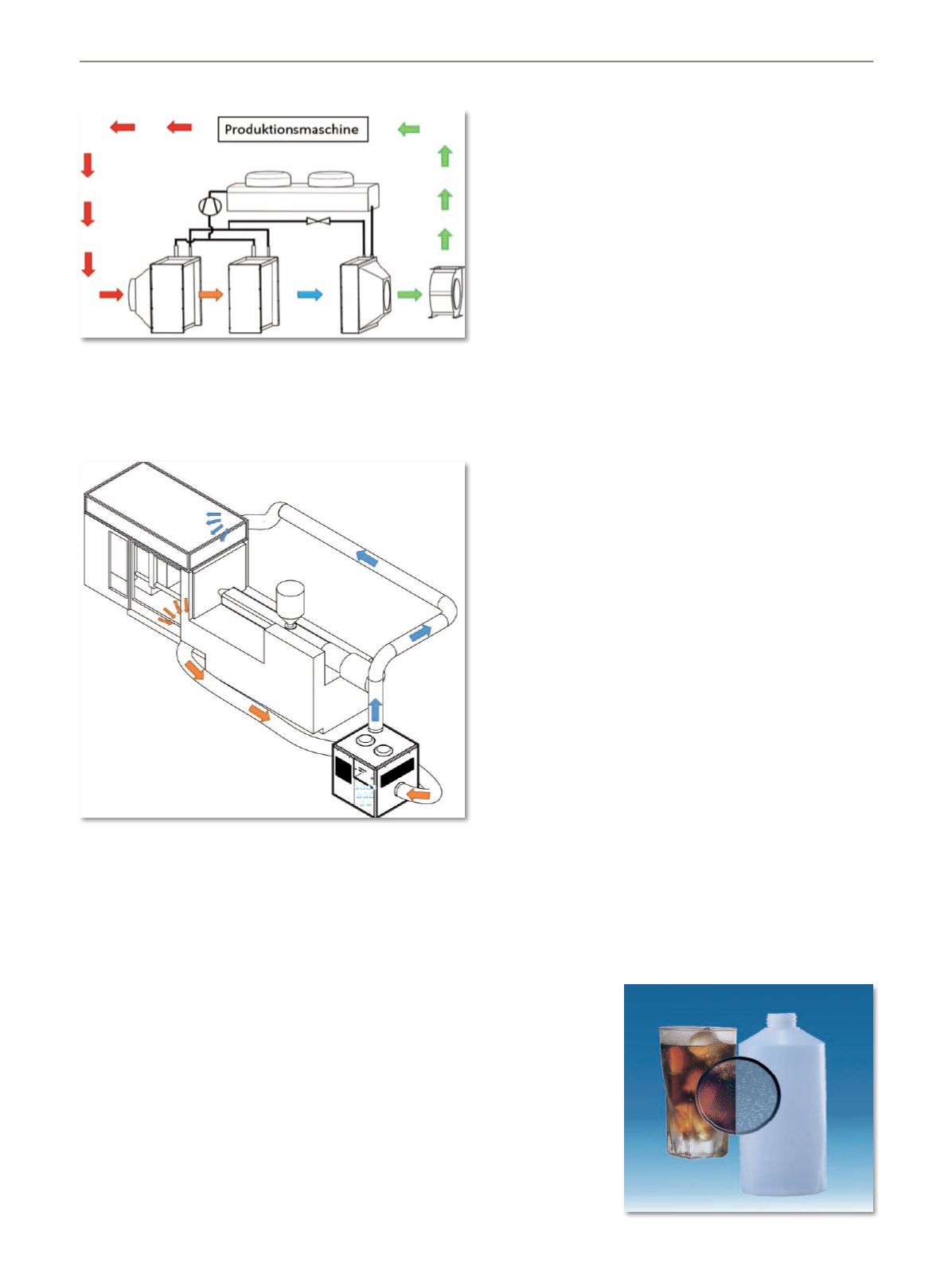
und höhere Produktivität an Spritzguss-, Thermoforming- und
Extrusionsblasmaschinen. Die DMS-Serie konnte sich unter sub-
tropischen und tropischen Produktionsbedingungen bereits be-
währen. Erste Referenzen stehen für ein deutliches Plus an Ef-
fektivität und Effizienz.
Das Phänomen der Kondensation in der Werkzeugtechnik
Wenn die Oberflächentemperatur bestimmter Objekte unter
dem Taupunkt der Umgebungstemperatur liegt, entsteht Kon-
densat. Dieses Problem tritt speziell an den mit Kühlwasser ge-
kühlten Formen von Kunststoffverarbeitungsmaschinen für das
Spritzgießen, Extrusionsblasen oder Thermoforming auf. Die
Kühlzeit, in den meisten Fällen der zeitlich längste Teil der Zy-
kluszeit und des Formprozesses, ist ein teurer und wichtiger Be-
standteil des Herstellungsprozesses. Durch die Reduzierung der
31
Extrusion 2/2016
Kühlwassertemperatur in der Form kann eine kürzere Zykluszeit
erreicht werden. Sinken die Temperaturen jedoch unter den Tau-
punkt der Umgebungsluft, entsteht Kondensat auf der Form-
oberfläche. In vielen Produktionsbetrieben in heißen und feuch-
ten Klimazonen wird daher die Kühlwassertemperatur zur Kom-
pensation angehoben, um eine Kondensatbildung zu vermei-
den. Diese, in der Praxis übliche Strategie hat einen entschei-
denden Nachteil – die Effizienz wird durch die Effektivität einge-
engt: Die Erhöhung der Kühlwassertemperatur verlängert die
Kühlzeit, reduziert die Produktivität und vermindert den Ertrag
(Faustformel dazu: 1°C Erhöhung der Wassertemperatur bedeu-
tet circa 2 % Produktionsrückgang). In vielen Fällen führt die
lange Kühlzeit zu einer vermehrten Kristallisierung im geform-
ten Kunststoff. Ebenso führt das Kondenswasser am Werkzeug
zu Wassermarkierungen (sogenannte „Orange Skin“) am Pro-
dukt und somit zu einer minderwertigen Produktqualität.
Einschränkungen konventioneller Technologie zur
Werkzeugentfeuchtung
Gängig ist eine Sorptionstrockung mit einem Sorptionsrotor.
Dieser uneffektive Ansatz verursacht vergleichsweise hohe
Energieverbräuche. Die energetischen Ineffizienzen entstehen
durch die zum Einsatz gebrachte Regenerationsheizung, die
Ventilatoren, die Antriebe sowie die Vor- und Nachkühlung mit-
tels Chiller. Daher bildet alternativ die Werkzeugentfeuchtungs-
anlage MSP (Mold Sweat Protection) einen wichtigen Pro-
grammschwerpunkt von Blue Air Systems. Viele dieser Geräte
sind weltweit im Einsatz und bringen auch nach vielen Jahren
im Produktionsbetrieb ihre volle Leistung und ermöglichen eine
kondensatfreie Produktion bei optimaler Kühlwassertempera-
tur. Sie ermöglichen höhere Produktivität und kürzere Kühlzei-
ten als vergleichbare Anlagen. Ein Nachteil aller Entfeuchtungs-
anlagen ist die Tatsache, dass sie relativ große Mengen von
Kaltwasser für die Vorentfeuchtung benötigen. In vielen Fällen
ist das vorhandene Kühlwassersystem nicht ausreichend dimen-
sioniert, um die notwendigen Kaltwassermengen bereitzustel-
len. Auch unter Wirtschaftlichkeitsbetrachtungen gelten Be-
schränkungen: Der Kunde ist nicht nur mit den Kosten des Ent-
feuchters, sondern auch mit den Kosten der Erweiterung des
Kaltwassersystems mit Chiller-Technologie konfrontiert.
Neuer Ansatz mit dem kaltwasserlosen DMS-System
(Dry Mould System) im geschlossenen System
Die DMS-Serie ist ein Entfeuchtungssystem auf Basis eines
Kondensationstrockners. Der Unterschied zu den anderen Va-
Funktionsprinzip des DMS (Dry Mould System): Der Prozess-
luftstrom im geschlossenen System wird in der DMS-Einheit
vorbehandelt, zum Werkzeug geführt und wieder zurück.
Die Zwei-Stufen-Kälteanlage mit der Mikro-Prozessor-
gesteuerten Chargenkondensation kühlt und entfeuchtet
die Prozessluft
Kondensationsfreie Produktionsbedingungen mit der
DMS-Serie: Das Umströmen eines Werkzeugs im
geschlossenen System – mehr Leistung, weniger Energie und
konstante Produktqualität
Konstante
Produktqualität
durch konden-
sationsfreie
Produktions-
bedingungen