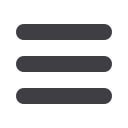
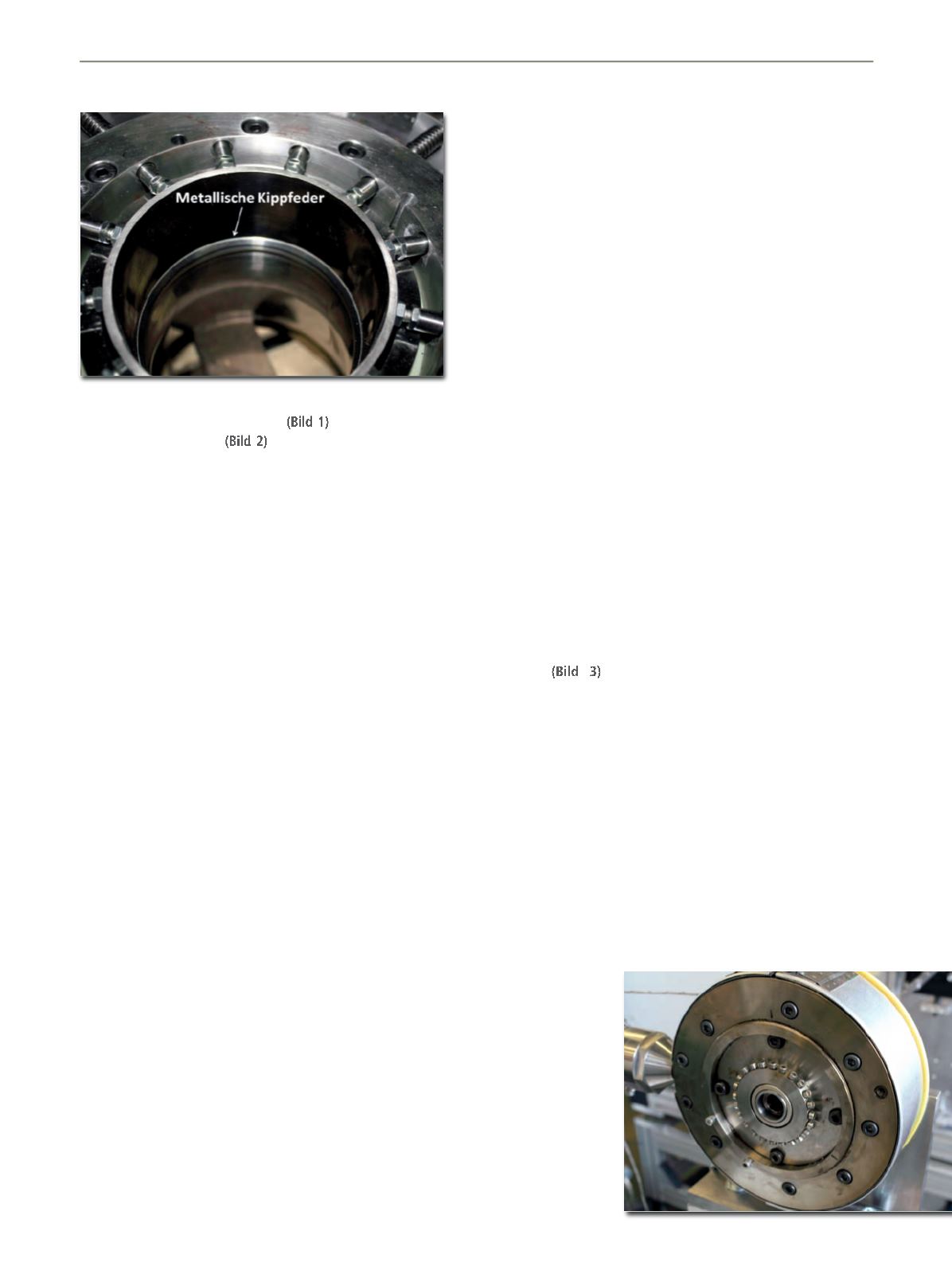
25
Extrusion 1/2016
Neuer Lösungsansatz
Bei Verwendung einer elastischen
oder einer metallischen
Kippdich-
tung werden diese Nachteile überwunden.
Mit Hilfe einer einfachen und sehr kosten-
günstigen Elastomerdichtung lässt sich die
Trennebene zwischen dem Kopf und der
Düse in einfacher Weise sicher abdichten
[3,4]. Für die Schmelze macht es keinen
Unterschied, ob sie an einer metallischen
oder einer elastomeren Fließkanalwand
haftet oder langsam entlang gleitet. Das
benachbarte Polymermolekül merkt be-
reits nicht, ob die Fließkanalwand aus ei-
nem Metall oder aus einem Elastomer be-
steht! Kippdichtungen aus Elastomeren
haben zudem den Vorteil, dass sie eine Ba-
jonettverschlusslösung zwischen der Düse
und dem Kopf zulassen, was einen sehr
einfachen und schnellen Düsenwechsel er-
möglicht. Solche Elastomerdichtungen
können zur Zeit allerdings nur bis zu einer
maximalen Dauertemperatur von 300 °C
eingesetzt werden. Auch verbietet sich ihr
Einsatz, wenn abrasive Schmelzekom-
pounds verarbeitet werden müssen. Die-
sen Einsatzbeschränkungen unterliegen
metallische Kippgelenke [4] nicht. Sie las-
sen allerdings keinen komfortablen Bajo-
nettverschluss zwischen dem Kopf und der
Düse zu.
Trifunktionelles Bauteil erweitert die
verfahrenstechnischen Möglichkeiten
Noch interessanter ist die Verwendung
eines neuartigen trifunktionellen Bauteils
[5] in einem Extrusionskopf. Bei der ela-
stomeren Lösung ist allerdings die maxi-
mal realisierbare Verschiebung mit weni-
gen Millimetern sehr gering. Die metalli-
sche Konstruktion erlaubt es, dass die
Düse über 20 mm axial verschoben wer-
den kann. Das ist besonders für das Blas-
formen interessant, wo die Position zwi-
schen der Düse und dem Dorn relativ zu-
einander verschoben wird, um die
Wanddicke des Vorformlings zu verän-
dern. Es wird nicht nur die Düse gegen-
über dem Kopf abgedichtet und ein Kip-
pen der Düse ermöglicht, sondern es
wird auch noch zugelassen, dass die Dü-
se axial zum Kern verschoben werden
kann. Mit derartigen Köpfen lässt sich
der Austrittsspalt am Kopfende bei lau-
fender Anlage stufenlos in einem vorge-
gebenen Bereich verstellen. Damit kön-
nen beispielsweise Köpfe zur Herstellung
von Bewässerungsschläuchen
hergestellt werden, mit denen man bei
konstantem Abstand zwischen der Düse
und der Kalibrierung unterschiedliche
Wanddicken des Schlauchs herstellen
kann, ohne den Extrusionsprozess unter-
brechen zu müssen. Je nach Anwendung
kann gewählt werden, ob manuell oder
motorisch gekippt und verschoben wer-
den soll. Bei der einfachen Schlauchher-
stellung reicht in aller Regel eine manuel-
le Verstellung aus. Beim Extrusionsblas-
formen ist eine motorische Verstellung
unabdingbar, um die Wanddicke des
Vorformlings während des Ausstoßens
verstellen zu können.
Vorteile der neuartigen Kipplösungen
• Sie sind sehr kostengünstig zu ferti-
gen, da jeweils nur ein einziges Bau-
teil, nämlich ein elastisches oder ein
metallisches Kippgelenk benötigt wird.
• Die Düse kann extrem feinfühlig,
wenn erforderlich im Mikrometerbe-
reich, gekippt werden.
• Eine vorhandene Position kann einfach
gemessen werden.
• Eine einmal erreichte Position kann
jederzeit reproduziert werden.
• Beim Kippen der Düse entstehen keine
Totstellen im Fließkanal.
• Durch eine Passung zwischen der Düse
und dem Kopf ist sichergestellt, dass
die Düse nur zentrisch montiert wer-
den kann.
• Die Kippgelenke lassen sich sowohl
manuell als auch motorisch betätigen.
Kippdüsen können somit automatisiert
betrieben werden und erfüllen bei
spielsweise alle Anforderungen, die an
eine Schiebedüse für das Blasformen
gestellt werden.
Beispiel: Schmelzeverteilung im
Rundkopf
Technische Anforderung, die eine gute
Schmelzeverteilung erfüllen sollte:
• Der Schmelzeverteiler sollte idealer-
weise betriebspunktunabhängig sein
• Die Verweilzeit sollte möglichst kurz
und das Verweilzeitspektum eng sein.
• Die Homogenität der Schmelze sollte
im Verteilersystem verbessert und
nicht verschlechtert werden.
• Die Unterschiede in der Schmelzede-
formation, die im Verteilersystem je
nach Strompfad, den das einzelne Mo-
lekül durchläuft, auftreten, sollten ge-
ring sein und sich am Düsenaustritt
nicht negativ auswirken.
Aktueller Stand der Technik
Die Notwendigkeit im Rundkopf den
vom Extruder zugeführten Schmelzevoll-
strang in eine Schlitzströmung überfüh-
ren zu müssen, führt zu unerwünschten
verfahrenstechnischen Konsequenzen,
die unvermeidlich sind. Dies gilt prinzi-
piell für alle gebräuchlichen Verteilerka-
nalsysteme, also für den Stegdornhalter,
Bild 2:
Flexringdüse mit
metallischer Kippdich-
tung, die die Flexring-
hülse gegenüber dem
Kopf abdichtet, die
aber gleichzeitig ein
Kippen der Flexring-
hülse relativ zum
Kopf zulässt
Bild 3: Quer angeschlossener Schlauch-
kopf mit Flexringhülse und stufenlos
verstellbarem Austrittsspalt