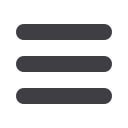
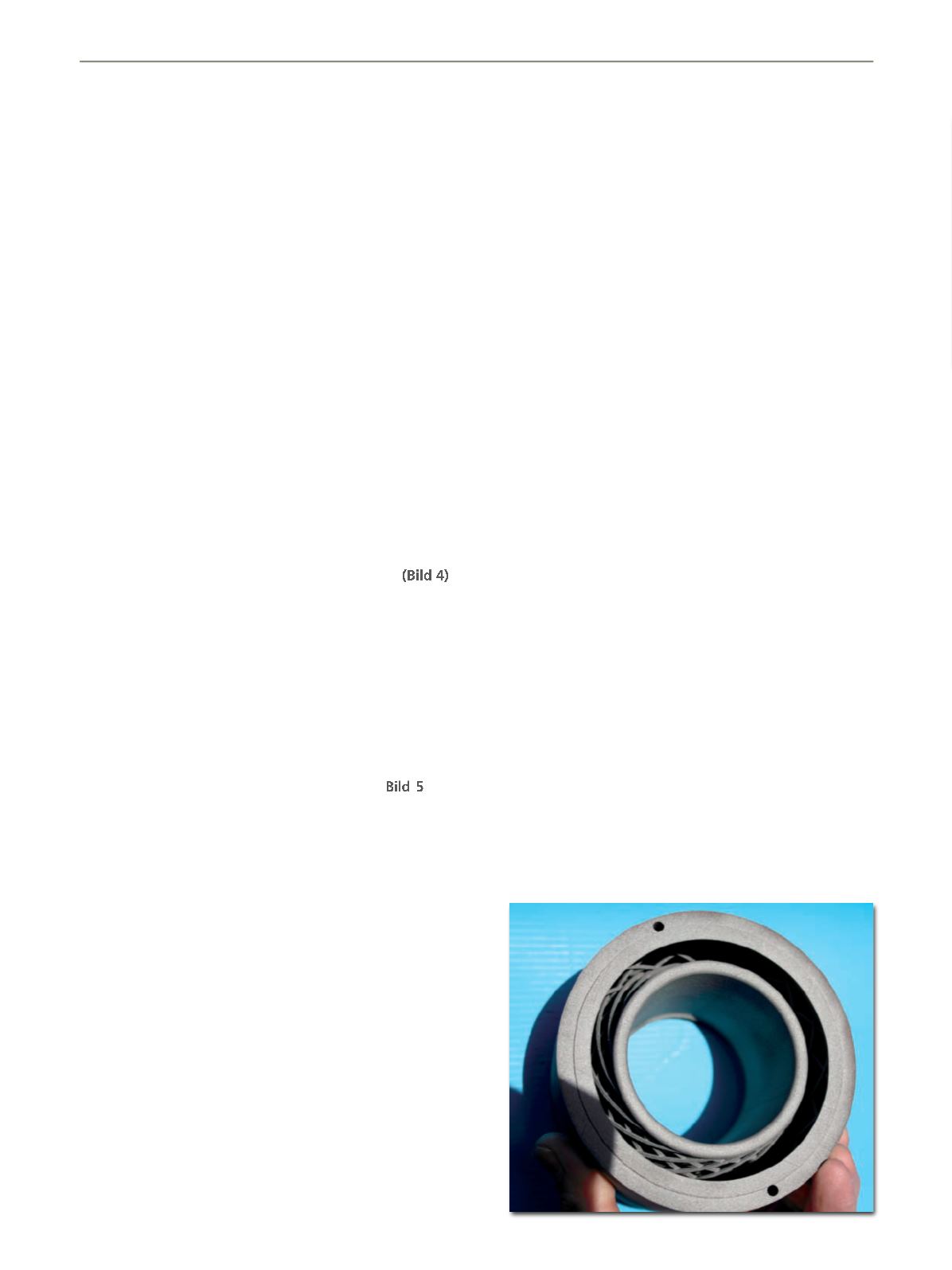
für den Pinolenverteiler, für die Herzkur-
ve und auch für den Wendelverteiler. Die
prinzipielle Entscheidung für ein Vertei-
lerkanalsystem hängt vorrangig vom je-
weiligen Einsatzfall und von den Prioritä-
ten, die der Anwender setzt beziehungs-
weise die die jeweilige Anwendung er-
fordert, ab. Aber alle Verteilerkanalsyste-
me:
• verlängern die Verweilzeit im Kopf,
• vergrößern das Verweilzeitspektrum,
• verschlechtern die Homogenität der
Schmelze,
• führen auch zu Unterschieden in den
Deformationen, je nachdem welchen
Strompfad das einzelne Polymermole-
kül durchströmt.
Mischköpfe überwinden die Nachteile
des Stegdornhaltersystems
Bisher wird in allen Rundköpfen die Ho-
mogenität der Schmelze, die in aller Re-
gel bereits nicht ideal homogen in einen
Kopf einströmt, in den etablierten Vertei-
lerkanalsystemen weiter verschlechtert.
Einzelne Schmelzebereiche benötigen im
Verteilerkanalsystem mehr oder weniger
Zeit und werden zusätzlich unterschiedli-
chen Scherbelastungen ausgesetzt. Bei
einer neuartigen zum Patent angemelde-
ten Mischkopflösung werden die Vorteile
des betriebspunktunabhängigen Steg-
dornhaltersystems, das zudem auch
noch von allen bekannten Verteilerkanal-
systemen die geringste Verweilzeit und
das engste Verweilzeitspektrum besitzt,
genutzt und die bisher vorhandenen
Nachteile in einen Vorteil verwandelt.
Dies wird erreicht, indem die Dornhalter-
stege als Mischstege ausgebildet wer-
den. Damit lassen sich sowohl die beim
Stegdornhaltersystem störende mecha-
nische Schwächung durch die Bindenäh-
te als auch Wanddickenunterschiede
über dem Umfang des aus dem Kopf
ausgetragenen Schmelzeschlauchs ver-
meiden. Darüber hinaus wird auch noch
mittels der Mischstege die Homogenität
der Schmelze im Rundkopf nicht weiter
verschlechtert sondern im Gegenteil, sie
wird verbessert.
Wird der Dorn mit Hilfe von sehr engma-
schigen Mischstegen am Kopfgehäuse
befestigt, dann erfahren alle Schmelze-
moleküle unabhängig welchen Stromp-
fad sie durchlaufen, nahezu die gleichen
elastischen Deformationen und es bildet
sich ein sehr engmaschiges Bindenaht-
system aus, das keine negativen Auswir-
kungen auf die mechanische Festigkeit
des extrudierten Schlauchs mehr besitzt.
Das inzwischen auch im Metallbereich
etablierte Laserschmelzverfahren [6,7]
macht es möglich, im Vergleich zu aktu-
ellen Mischern viel
komplexere und
auch extrem filigrane Mischergeome-
trien zu realisieren, mit denen auch die
Erhöhung des Fließwiderstands in Gren-
zen gehalten werden kann.
Mit generativ hergestellten Mischerste-
gen werden besonders vorteilhafte Lö-
sungen möglich. Über diese noch relativ
neuen Fertigungsverfahren lassen sich
effektiv mischende Steggeometrien ferti-
gen, wie sie mit konventionellen Ferti-
gungsverfahren nicht herstellbar sind.
Völlig neuartige Mischerstrukturen sind
realisierbar. Sie können sehr filigran sein
aber dennoch eine hohe mechanische
Festigkeit aufweisen. Damit kann die
Schmelze sowohl in Umfangsrichtung als
auch in radialer Richtung umgelenkt
werden
.
Momentan sind zwar die Kosten von im
Laserschmelzverfahren hergestellten Kopf-
komponenten noch relativ hoch, so dass
man zur Zeit noch darauf achten muss,
dass die Teile nicht zu groß werden. An-
dererseits lassen sich mit generativen Me-
thoden Köpfe viel kompakter bauen, so
dass selbst momentan bereits Köpfe, die
im Laserschmelzverfahren hergestellt wer-
den, auch von der Kostenseite interessant
sind.
zeigt in einer Schnittdarstel-
lung einen kompletten Rundkopf, der ge-
genüber konventionell
hergestellten
Köpfen interessante verfahrenstechnische
Vorteile verspricht, der aber bereits heute
im Laserschmelzverfahren sehr kosten-
günstig herzustellen ist.
Beispiel: Optimierung der
Wanddickenverteilung von
blasgeformten Hohlkörpern
Technische Anforderungen, die Blasköpfe
erfüllen sollten:
• Die Wanddicke des Vorformlings muss
sowohl in Abzugs- als auch in Um-
fangsrichtung beeinflussbar sein.
• Es sollte speziell in Umfangsrichtung
ein möglichst großer Dickengradient
erreichbar sein.
• Die Austrittsgeschwindigkeit der
Schmelze muss über dem Umfang
trotz unterschiedlicher Wanddicken
annähernd konstant sein.
• Beim Verfahren des Dorns sollte sich
die Austrittsgeschwindigkeit der
Schmelze nicht ändern.
Aktueller Stand der Technik
Köpfe für das Blasformen besitzen im
Allgemeinen am Ende der Düse einen
konischen Fließkanal, mit dem keine der
genannten Anforderungen befriedigend
erfüllt werden kann.
Alternative Lösung
Wenn man die Düse am Ende nicht ko-
nisch sondern zylindrisch ausführt, dann
ergeben sich für das Blasformen neue
verfahrenstechnische Möglichkeiten [8].
Man kann beispielsweise mit zylindri-
schen Düsen auch bei der Herstellung
von Stapelkanistern Wanddickenvertei-
lungen erreichen, wie sie bisher bei koni-
schen Düsen nur mit technisch sehr auf-
wendigen und auch teuren PWDS- oder
Flexringsystemen realisierbar waren. Be-
sonders vorteilhaft ist die neue Düsenge-
staltung bei technischen Teilen, die eine
komplizierte nicht symmetrische Geome-
Bild 4: Einteilig im
Laserschmelzverfahren
hergestellter Mischer
mit speziellen
Mischstegen, die die
Schmelze sowohl in
Umfangsrichtung als
auch in radialer
Richtung verteilen
26
Extrusions-Werkzeuge
Extrusion 1/2016