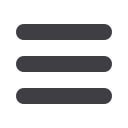
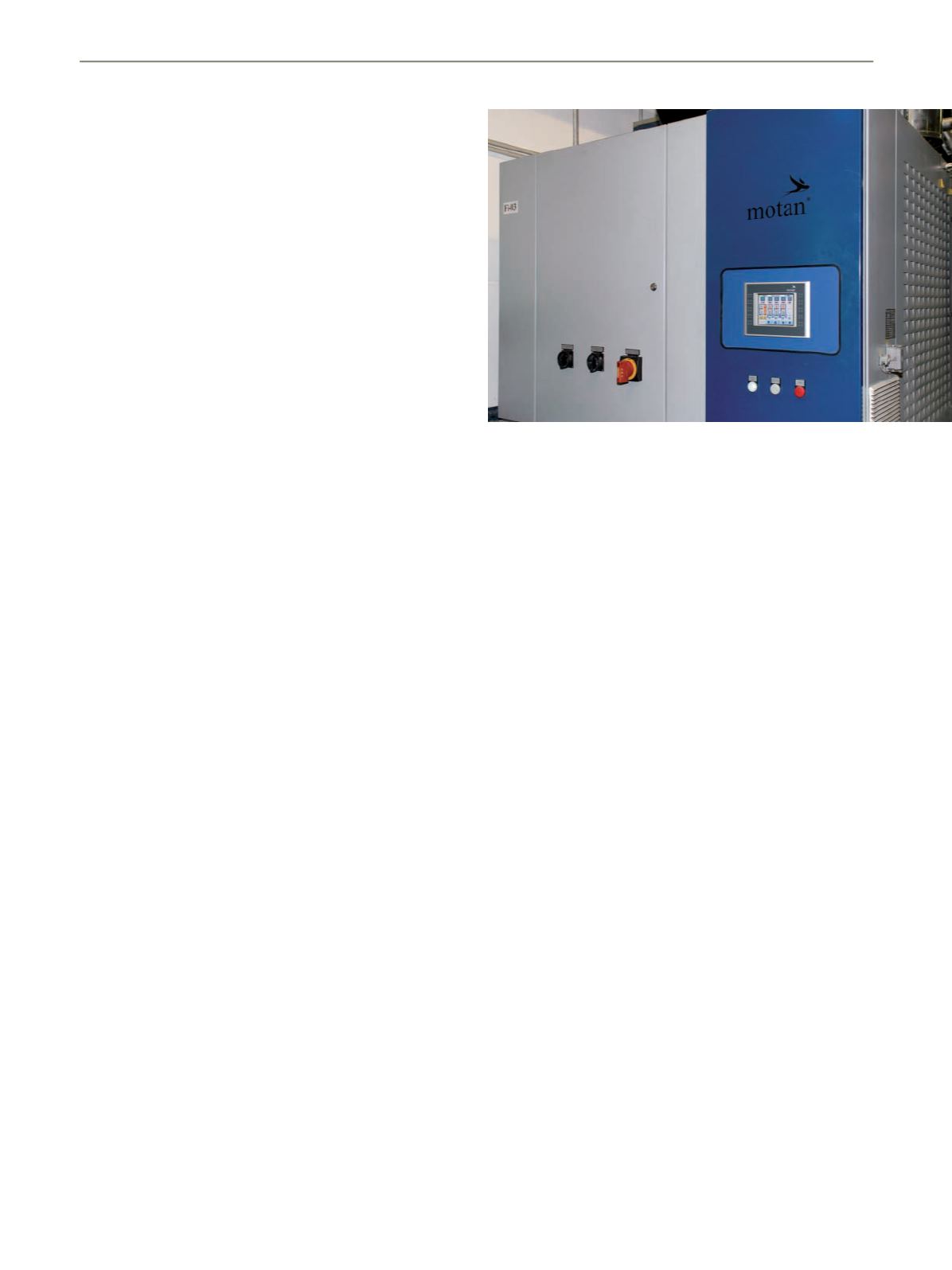
49
Extrusion 1/2016
kann PET naturgemäß nicht die Reißfestigkeit von Stahlbän-
dern aufweisen, doch die spielt bei der Transportsicherung eine
eher untergeordnete Rolle. Viel wichtiger ist hingegen die so
genannte Schockreserve, wenn es darum geht, impulsartige
Belastungen zu absorbieren. Hinzu kommt die Elastizität – sie
beträgt bei den Cyklop-Bändern je nach Ausführung bis zu 14
Prozent – um Spannungsverluste bei schrumpfenden Packstü-
cken auszugleichen. Stahlband hat hingegen lediglich eine Ela-
stizität von einem Prozent. Zudem rostet PET nicht, die Verlet-
zungsgefahr ist deutlich geringer, es kann auch bei empfindli-
chen Packstücken problemlos eingesetzt werden und es hat na-
türlich ein deutlich geringeres Gewicht als Stahl. Gegenüber
Umreifungsbändern aus PP bietet PET schließlich mit einer Glas-
übergangstemperatur von 60 bis 70°C den Vorteil, dass das
Packgut auch bei Hitze stabil zusammengehalten wird.
Umreifungsbänder herzustellen ist nur vordergründig
einfach
Im Werk Köln produziert Cyklop mit ihren Extrusionslinien plus
nachgeschalteter Peripherie rund 50 verschiedene PET-Umrei-
fungsbänder, die je nach Querschnitt eine Reißfestigkeit zwi-
schen 2.000 und 13.000 N haben.
Die Extrusionslinien laufen mit bis zu zehn Einzelsträngen, die
einschließlich der vor- und nachgeschalteten Peripherieanlagen
zwischen 90 und 100 m lang sind. Nachdem die Bänder den
Düsenkopf verlassen haben, werden sie zunächst durch ein
Wasserbad geführt um abzukühlen und in nachfolgenden An-
lagen zweifach verstreckt. Weiter geht es durch eine Prägestati-
on, der sich ein Relaxierofen anschließt, um das gestresste Ma-
terial zu entspannen. Es folgen eine Kühlstrecke, die Druckanla-
ge zur individuellen Beschriftung sowie die Wickelstationen für
die Konfektionierung. Die Extrusionslinien einschließlich der
vor- und nachgeschalteten Peripherie sind nahezu komplett
redundant aufgebaut. Das hat den Vorteil, dass beim Ausfall ei-
ner einzelnen Anlagenkomponente, etwa eines Mischers, auf
eine andere Mischstation gewechselt werden kann, ohne die
Extrusionslinie abzuschalten.
Die Produktion läuft rund um die Uhr an sieben Tagen in der
Woche. Lediglich um die Weihnachtszeit stehen die Anlagen
für eine bis zwei Wochen, wobei die Zeit für Revisionsarbeiten
genutzt wird.
All das klingt vordergründig einfach, ist aber tatsächlich eine
höchst komplizierte Angelegenheit, insbesondere was das Ma-
terialhandling betrifft. Welche Leistungen die Anlagen bringen
müssen, verdeutlichen die Durchsatzleistungen der Extrusions-
linien, die sich im Bereich von 450 bis 600 kg/h bewegen.
PET ist ein schwieriges Material
Zu Beginn seiner Karriere als Werkstoff für Umreifungsbänder
galt Polyester noch als technischer Kunststoff und war entspre-
chend teuer. Erst als Anfang der 90er Jahre PET-Getränkefla-
schen den europäischen Markt eroberten, wurde aus PET ein
Massenkunststoff. „Über die Entsorger und Wiederverwerter
stand uns plötzlich genug Recyclingmaterial zur Verfügung, um
den hohen Materialkosten der Neuware zu begegnen“, erin-
nert Bernd Causemann. Als General Plant Manager ist Bernd
Causemann bei Cyklop für die Konfiguration und Installation
der Umreifungsband-Anlagen an allen Standorten weltweit
Serienmäßig mit einer flexiblen Bus-Technologie ausge-
stattet, lässt sich die Trocknersteuerung Luxor-Net für bis zu
16 Trockentrichter und bis zu 24 Maschinenfördergeräte
erweitern. Neben den Einstell- und Überwachungsmöglich-
keiten an den Anlagen gibt es bei Cyklop eine zentrale
übergeordnete Station im Schichtführerbüro, von der sich
alle Daten einsehen lassen
sowie für die Produktion und Entwicklung in Köln verantwort-
lich. „Damals handelte es sich zunächst um Regranulat, weil die
Flakes in der Regel zu verunreinigt waren. Mitte der 90er Jahre
gelang es uns dann erstmals, Regranulat aus Flaschen für die
Polyesterbandproduktion einzusetzen“, berichtet Causemann.
Heute verarbeitet Cyklop nahezu keine Neuware, sondern
überwiegend Regranulat und Mahlgut (Flakes) aus DSD-Materi-
al, das gewaschen von den Recyclern kommt. Neuware kommt
nur dann infrage, wenn transparente oder weiße Bänder bzw.
Sonderanfertigungen verlangt werden.
PET zählt zu den empfindlichen, überaus hygroskopischen Poly-
meren, ist sehr hydrolyseanfällig, baut demzufolge bei thermi-
scher Belastung ab. Im Falle der Umreifungsbänder wirkt sich
das nachteilig auf die Festigkeit aus. Ein Maß, um den Einfluss
von Feuchtigkeit bzw. die Qualität von PET abzuschätzen, ist
die so genannte intrinsische Viskosität – auch IV-Wert genannt
– welcher eine Angabe für das mittlere Molekulargewicht ist.
„Beim Regranulieren von PET setzt eine Art "Downcycling" ein,
eine Abnahme der Schmelzeviskosität aufgrund der thermi-
schen Mehrfachbelastung. Bei den Flakes hingegen wirkt es
sich als erschwerend aus, dass die Flaschen immer dünner wer-
den, weshalb das Material noch schneller abbaut. 2004 hatten
wir noch IV-Werte von 0,75 bis 0,76 dl/g bei den Flakes, heute
liegen wir bei 0,69 bis 0,70 dl/g“, bringt es Causemann auf den
Punkt. Mit anderen Worten, ein Interessenkonflikt: Die Fla-
schenhersteller wollen dünne Flaschen herstellen, wofür sie
niedrige IV-Werte benötigen, Cyklop benötigt hingegen hohe
IV-Werte für die Verstreckung. Als idealen IV-Wert nennt
Causemann 0.83 bis 0.87 dl/g. Zwar lässt sich dem Problem
durch Zugabe eines entsprechenden Masterbatches begegnen,
wie Causemann erklärt, doch sei das auch eine Kostenfrage bei
zehn Euro/kg und einer erforderlichen Dosierung von bis zu
zwei Prozent.