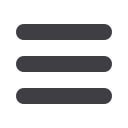
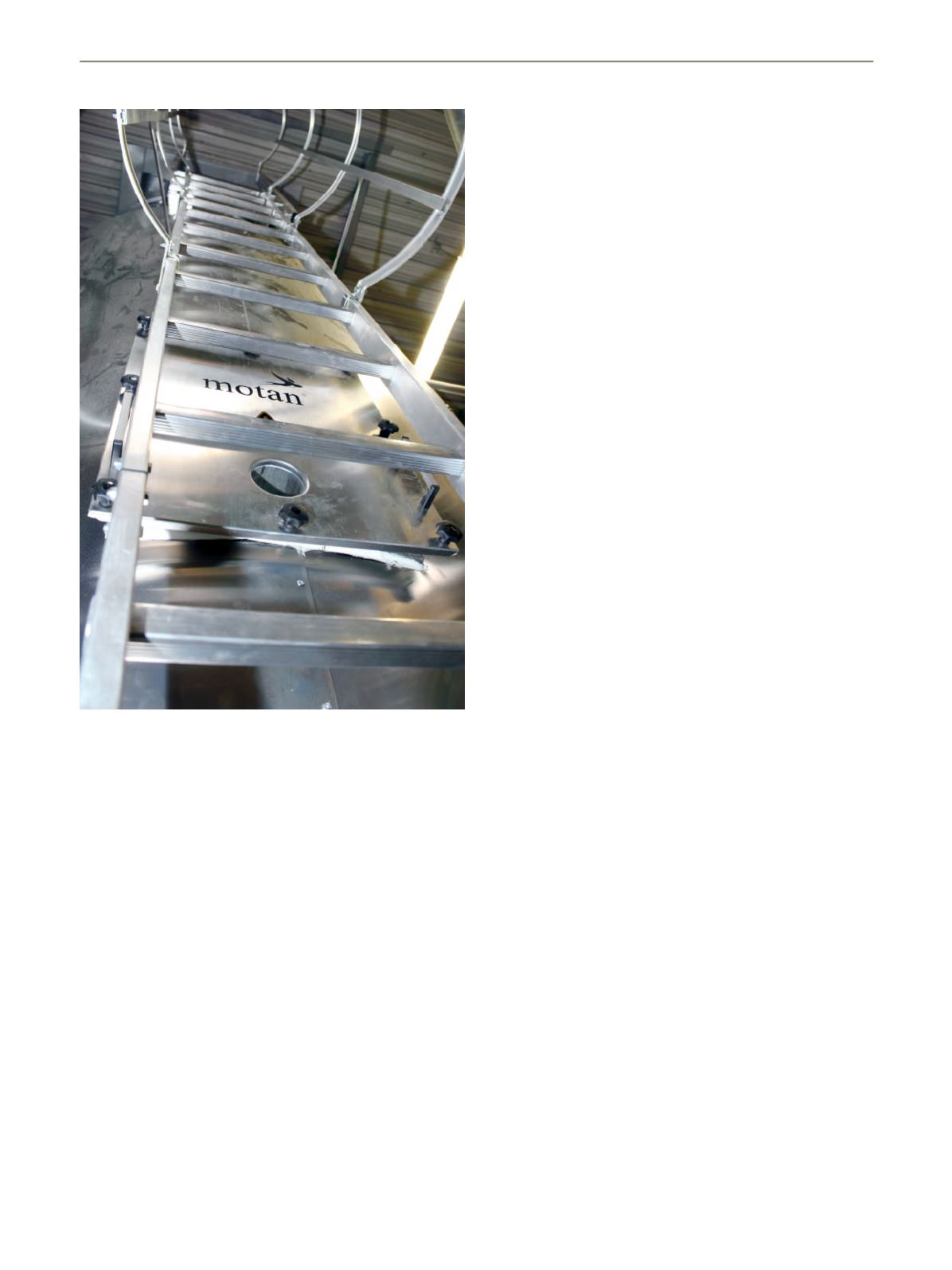
50
Peripherie
Extrusion 1/2016
Gelagert wird das Material in Doppelkammersilos von Zeppelin,
neun für Regranulat und drei für Mahlgut. In den Doppelkam-
mersilos sind die Kammern durch einen Mittelkonus voneinan-
der getrennt, wobei jede Kammer eine Lkw-Ladung fasst. Die
Chargentrennung hat einen praktischen Hintergrund: Bei jeder
Lieferung erfolgt als Materialeingangsprüfung eine hausinterne
IV-Messung, die alles in allem etwa 70 bis 80 Minuten dauert –
vorher darf nicht abgeladen werden. Falls trotz der Warenein-
gangsprüfung Probleme entstehen, kann das Material aus der
Kammer abgesaugt werden, ohne dass es sich mit Gutmaterial
vermischt hat. Von den Silos wird das Material mit einer Saug-
förderung zu den Kristallisatoren gefördert.
Vor seiner Verarbeitung ist PET bei Temperaturen von 160 bis
170 °C auf eine Restfeuchte von circa 0,2 Prozent zu trocknen.
Das Material erreicht jedoch bei cirka 80 °C einen Glasüber-
gangsbereich, wobei die Molekülstruktur von amorph in teil-
kristallin übergeht. In dieser Übergangsphase wird das Material
klebrig und neigt zum Verklumpen. Aus diesem Grund wird PET
zunächst bei 150 bis 160 °C kristallisiert, wobei es ständig in
Bewegung zu halten ist, damit es nicht verklebt. Nach dem
Kristallisieren – das übrigens getrennt nach Granulat und Flakes
erfolgt – muss das vorgetrocknete Material weitere fünf bis
sechs Stunden bei 160 bis 170 °C Trockenlufttemperatur auf
seine Verarbeitungsfeuchte fertig trocknen. Bedarfsabhängig
wird es anschließend zu den Extrusionslinien gefördert.
Optimierungs-Engineering –
eine besondere Herausforderung
Die Konfiguration der Produktionsanlagen bei Cyklop nimmt
Causemann weitgehend selbst in die Hand. So kommt es, dass
sich in den Anlagen Baugruppen von über sechs verschiedenen
Lieferanten befinden. Die Anlagen werden überdies ständig op-
timiert. Die derzeit letzte Maßnahme betraf den Umbau einer
Produktionslinie, um künftig neben Granulat auch Mahlgut zu
jeweils bis zu 100 Prozent verarbeiten zu können. „Die indivi-
duelle Konfiguration der Anlagen bei Cyklop ist für uns immer
wieder eine besondere Herausforderung“, erinnert sich Georg
Flink von der Kunststofftechnik Flink und Wortmann GbR, Bur-
scheid, der das Projekt als Vertriebspartner von Motan-Color-
tronic betreute. „Wir arbeiten bereits seit vielen Jahren zusam-
men – und schätzen den konstruktiven, partnerschaftlichen
Umgang“, stellt er fest.
In diesem Fall ging es zunächst darum, in die vorhandene Infra-
struktur einen Kristallisator Luxor HDC 1800 mit Rührwerks-
trichter, Fassungsvermögen 2.500 l, ausgerüstet mit einem für
Flakes geeigneten Trichterfördergerät Metro HCG 30 MG, zu
integrieren. Darüber hinaus war der ältere, bestehende Trock-
ner mit einem Trockenlufterzeuger sowie einem Trockentrichter
(3.000 l), beide von AZO, um einen weiteren Trockentrichter
von Motan-Colortronic mit 7.500 l Fassungsvermögen zu er-
weitern. Und schließlich war noch ein zum Durchsatz passen-
des Dosier- und Mischgerät Gravicolor GC 600 zu integrieren.
Wegen der Platzverhältnisse einerseits, aber auch wegen des
ebenfalls bereits vorhandenen und auf dem Extruder installier-
ten Fördergerätes, musste das Gravicolor auf der Rückseite des
Extruders aufgebaut werden. Vom Gravicolor wird das Material
von einem AZO-Fördergerät abgeholt und in einen Pufferbehäl-
ter mit 400 l Inhalt gefördert. „Es handelt sich im Prinzip um ei-
ne Kombianlage“, beschreibt Flink die Situation.
Die Materialförderung erfolgt bei Cyklop komplett mit Vaku-
umsystemen. Im Zuge der Optimierung der Cyklop-Produktion
wurden drei Fertigungslinien überarbeitet und an jeder Linie
drei Vakuumkreise installiert. Der erste Vakuumkreis für den
Materialtransport von den Silos zu den Kristallisatoren, der
zweite Kreis für den Transport von den Kristallisatoren zu den
Trocknungstrichtern und der dritte Kreis von den Trocknungs-
trichtern zu den Dosierstationen.
„Eine solche Anlage zu ‚komponieren’ ist eine spezielle Heraus-
forderung“, beschreibt Georg Flink die Situation: „Normaler-
weise sind Systemgeräte aufeinander abgestimmt. Hier musste
sich unsere Applikationsabteilung insbesondere mit der Anpas-
sung der verschiedenen Systeme zueinander befassen. So war
etwa der neue Trockentrichter an das Gebläse des schon vor-
handenen Trockners anzupassen. Dazu muss man wissen, um
was für ein Gebläse es sich handelt, welchen Staudruck es
bringt und was für eine Gebläsekennlinie es hat, und welche
Rohrleitungsquerschnitte bereits vorhanden sind. Schließlich
soll der neue Trichter nicht soviel Luft verbrauchen; nicht dass
am Ende der bereits vorhandene Trockentrichter den Betrieb
Technik bis unter die Decke – um die gewaltigen Durchsätze
sicherzustellen, wurde eine der Linien um diesen Trocken-
trichter mit einem Fassungsvermögen von 7500 l erweitert