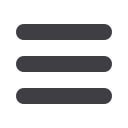
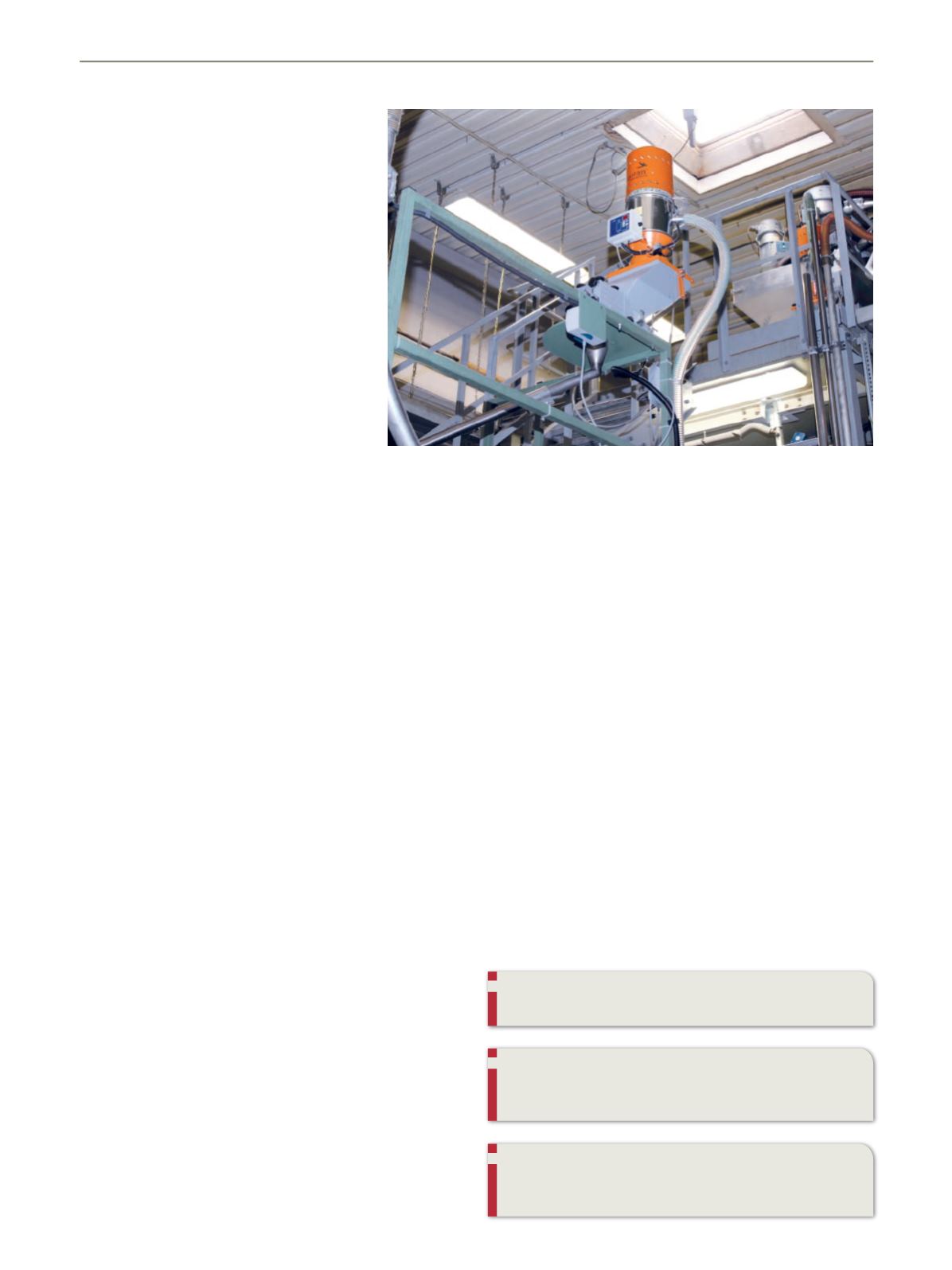
51
Extrusion 1/2016
einstellt. Es war eine richtig verzwickte strö-
mungstechnische Berechnung“, fasst Flink zu-
sammen.
Auch die steuerungstechnische Integration der
neuen Anlagenkomponenten in die bestehende
Konfiguration sei eine Herausforderung gewe-
sen, bestätigen Causemann und Flink. Was bei
Systemanlagen kein Thema ist, kann im Falle ei-
ner 'Komposition' mit Anlagenkomponenten
verschiedener Hersteller durchaus diffizil wer-
den.
Eine weitere Hürde stellten die Temperaturen in
der Produktionsumgebung dar. Insbesondere
die auf den Maschinen aufgebauten Gravicolor
sind in der Halle bei Volllastbetrieb sehr hohen
Umgebungstemperaturen zwischen 80 und
100 °C ausgesetzt. Um sicherzustellen, dass die
Geräte präzise und störungsfrei arbeiten, wur-
den die Pneumatikzylinder mit speziellen Dich-
tungen bestückt.
Ausgestattet sind die bei Cyklop installierten
Gravicolor 600 mit jeweils vier Dosiereinheiten für Granulat,
Flakes, Farbe und Masterbatch. Bei zwei der Linien wurden die
Dosier- und Mischgeräte sowie die Pufferbehälter mit 400 l Fas-
sungsvermögen trotz ihrer Größe direkt oberhalb der Extruder
installiert. Die Anordnung trägt nach Auffassung von Bernd
Causemann dazu bei, dass sich das Material auf der kurzen
Strecke vom Trichter zum Einzug nicht so schnell entmischt und
demzufolge homogener ist. Er sieht darin noch einen weiteren
Vorteil. „Für uns erfüllen die Pufferbehälter – deren Inhalt ist
übrigens mit Trockenluft überlagert – die Aufgabe eines kleinen
Silos. Falls während der Produktion ein Problem auftritt, hat der
Schichtführer rund fünf bis zehn Minuten Zeit um das Problem
zu lösen, ohne dass er die Anlage abstellen muss. Kleinere
Schwierigkeiten mit der Materialversorgung lassen sich in die-
ser Zeit durchaus lösen“, stellt er fest.
Bei der dritten Anlage wurde das Gravicolor außerhalb des
Hochtemperaturbereichs neben dem Extruder aufgebaut. „Die
anfängliche Befürchtung, es könne beim Fördern zum 400 l-
AZO-Trocknungstrichter auf dem Extruder zum Entmischen
kommen, hat sich nicht bestätigt. Wir haben einmal eine gute
Durchmischung und darüber hinaus die Förderstrecke kurz ge-
halten“, erklärt Georg Flink.
Anlagenkonfiguration –
Technik individuell zusammengestellt
Das aufgrund jahrelanger Erfahrungen gesammelte Know-how
drückt sich bei Cyklop dahingehend aus, dass es dort keine Pro-
duktionsanlagen „von der Stange“ gibt. Vielmehr konfiguriert,
teilweise konstruiert und baut Causemann die Linien nach eige-
nen Vorstellungen. So kommt es, dass sich in den Anlagen Ex-
truder von Barmag und Reifenhäuser, Schmelzefilter von
Gneuß und Kreyenborg, Temperiergeräte von GWK, Trane und
Weinreich, Trockner, Dosiergeräte und Absaugkästen von AZO,
Zeppelin und Motan-Colortronic – um nur einige zu nennen –
finden. Von Vorteil für die Eigenentwicklungen, etwa die Auf-
spuleinrichtungen oder die Übergabestellen zwischen den ein-
zelnen Baugruppen, ist der eigene Maschinenbau von Cyklop.
Auch die übergeordnete Anlagensteuerung ist eigens nach in-
dividuellen Vorgaben ausgelegt worden. Neben den Einstell-
und Überwachungsmöglichkeiten an den Anlagen gibt es eine
zentrale übergeordnete Station im Schichtführerbüro, von der
sich alle Daten einsehen lassen.
Fazit
„Mit dem Aufbau einer Produktionslinie ist es nicht getan, zwi-
schendurch finden bei uns immer wieder punktuelle Optimie-
rungs- und Modernisierungsmaßnahmen statt – die durchaus
eine Herausforderung sein können“, fasst Causemann schmun-
zelnd zusammen. „Wir haben in der Vergangenheit und auch
diesmal unglaublich konstruktiv mit Cyklop zusammengearbei-
tet“, ergänzt Flink. „Eine Herausforderung war beispielsweise –
neben den angesprochenen Anpassungsarbeiten – die Opti-
mierung der Verfahrenstechnik unter Berücksichtigung der ho-
hen Umgebungstemperaturen und der eingeschränkten Quali-
tät des Mahlguts“, stellt Flink fest. Das nächste Projekt wird be-
reits angedacht: Es soll eine Visualisierung (LinkNet 2.0) mit
dem Ziel installiert werden, das komplette Materialhandling ab-
zubilden.
Autor: Dipl.-Ing. Thomas Schwachulla
Redaktionsbüro, Leipzig
motan-colortronic gmbh
Otto-Hahn-Str. 14, 61381 Friedrichsdorf, Germany
www.motan-colortronic.deCyklop GmbH
Industriestr. 133, 50996 Köln, Germany
www.cyklop.deDosiergerät Minicolor mit Fördergerät Metro HES 250